Not An Audiophile – The Podcast featuring Matthew Bond who started TARA Labs in Australia and is now Matthew Bond Audio in Oregon, USA. Matthew’s journey began in the mid to late 1980s in Sydney, Australia, where he started his cable designing business as TARA Labs. His breakthrough came when his Phase Two speaker cable was reviewed by Stereophile magazine and dubbed as class A, outperforming competitors like Monster Cable and Audioquest. This success led Matthew to relocate to the United States, where he continued to innovate and grow his business. Listen to Part 1 Episode 002
In our follow up Episode 017, Matthew Bond debunks popular cable myths including cable lifters, directional cables, copper competition, cryogenic treatments and nonsense quality claims.
Podcast transcripts below – Episode 002 and Episode 017
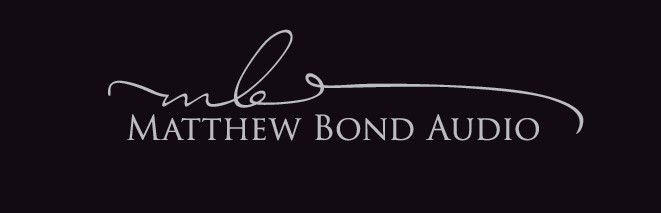
TRANSCRIPT
SEASON 1 – EPISODE 002 – Matthew Bond, TARA Labs & Matthew Bond Audio
Andrew: Matthew Bond is the man behind TARA Labs cable
Matthew Bond: Hey, I’m wearing, what we call pampers here. I’m not sure what to call them.
Andrew Hutchison: This is getting worse.
Matthew Bond: I’ve already used them.
Andrew Hutchison: Hello, Andrew here from not an audiophile podcast. this is episode two, season one, of course. And today we’re interviewing, Matthew Bond, who, is the man behind TARA Labs cable. He’s got a lot to say and, it’s all very interesting.
Andrew Hutchison welcomes Matthew Bond and Brad Serhan to the podcast
Without any further ado, today we’re joined by, somewhat famous, cable designer, Matthew Bond. he’s on the line from Oregon in the US. And just for light entertainment, we’ve also got Brad Serhan from Sydney. Hello, everybody.
Brad Serhan: Hi, Andrew.
Andrew Hutchison: Morning, Brad.
Matthew Bond: Hello, Andrew.
Andrew Hutchison: And hello, Matthew.
Brad Serhan: M morning.
Andrew Hutchison: And of course for Matthew, it’s. It’s the evening there, I guess. Yesterday.
Matthew Bond: Yesterday, yeah. Hey, you’ll have to tell me what happens.
Andrew Hutchison: Well, I mean, you know, I mean.
Brad Serhan: Actually, it looks good for you, Matt. It looks very good for you. Let me tell you. Tomorrow’s gonna be.
Andrew Hutchison: Yeah, I think in the good old days. And this is, this is a podcast that does obviously involve electronics. So I don’t think it’s completely out of theme to mention that. I think. I mean, there’s stories, at least, that back in the day, people were rigging horse races between time zones by using amateur radio or something, I think, you know. So there was no. No, the general public didn’t have access to radios, I guess, and they were sending Morse code backwards and forwards between wa and the east coast or something like that. And, Morse code. Morse code. Well, it was. It was a horse code. Because if you got the right horse code and placed the right bet, you, I mean, you had 2 hours. So, Yeah.
Brad Serhan: Yeah, I. Bloody marvellous.
Andrew Hutchison: Kind of irrelevant.
Oregon is halfway between wine country and craft beer hop growing oregon beer country
So you’re in Oregon, matthew. and not too far north of the californian oregon border, which by my reckoning, places you more or less halfway between fantastic californian wine country and fantastic, craft beer hop growing oregon beer making country. Is that.
Matthew Bond: You’re right, andrew. Yeah. The amount of beer that’s up here in terms of the variety and the, Yeah, it’s amazing. I like dark beer myself, you know, porters and such. But. Yeah.
Andrew Hutchison: Yeah.
Matthew Bond: we get everything here. It’s hard not to go to a, restaurant or a cafe now.
Andrew Hutchison: Yes.
Matthew Bond: And find that they’re selling six or eight different types of, micro brew.
Andrew Hutchison: That’s fantastic. And I think the bit. I mean, we’ve got a great craft, beer industry in Australia as well, but we’re really just copying what America was doing 20 or 30 years ago. But the advantage you guys have over there is the freshness of the hops, which of course if you’re making an ipa and maybe if you’re making a porter, I mean, fresh hops is the go. And of course it doesn’t get any fresher because I think it’s grown. A lot of it has grown not too far north of where you are. yes. So yeah, great place to be if you like drink, which, you know, I kind of do, but anyhow, we’ll go sideways from there.
So you, you started your cable, uh, making cable designing business in Australia
So you, you started your cable, making cable designing business actually in Australia. And you don’t sound terribly australian these days. But what’s your history there?
Matthew Bond: yes, I started in the mid to late eighties, in Australia, in Sydney, Australia. Met Brad right around that time.
Andrew Hutchison: Oh, so you knew Brad back then?
Matthew Bond: I knew him when he was wearing shorts.
Brad Serhan: I’m in shorts now, Matt, let me tell you.
Matthew Bond: Okay. yeah. so the business started in Sydney, okay. In the mid m, mid to late eighties, and then at some point in the few years after that I had to move to the United States, okay. Because of a magazine review, in stereophile, okay. Which had my simple product, the phase two speaker cable, dubbed as being class a. And beating out monster audioquest, Kimber straight, wire, all of them.
Andrew Hutchison: Wow.
Matthew Bond: There were about 15 or 18 brands of speaker cable competing in the review.
Andrew Hutchison: So how,
00:05:00
Andrew Hutchison: that’s of course amazing and obviously was a business breakthrough, in its time. But how did you, did you, you was making the cable and distributing it or selling it in the US? Is that how Stereophile got their hands on it or did you submit it to them? How did that work?
Matthew Bond: I was at the January CES show, consumer electronics show.
Andrew Hutchison: Okay.
Matthew Bond: In Las Vegas in January of 88.
Andrew Hutchison: Yeah.
Matthew Bond: And Dick Olsher happened to come into the room and he was chatting with me about cables and he said, well, you need to send me a set of, I guess it was an eight foot pair. you need to send me a set and I’ll listen to them and compare them to the other speaker cables.
Andrew Hutchison: Okay.
Matthew Bond: So I obliged. As you said, that was about, what is that about six months prior to the review happening?
Andrew Hutchison: Okay, that’s I mean, I. Did you think much? I mean you must have been, I mean I would have been slightly starstruck, I guess, by even having a conversation with him. But you felt at that point that this trip to the show, to the Ces, Washington, worthwhile all of a sudden. I guess because of that.
Matthew Bond: I mean, it was, it was fortuitous, but, I’d spent many years comparing different wire gauges, wire sizes, and listening to them. And then I was fortunate to get some research material that had been done by the National Bureau of Standards.
Andrew Hutchison: Okay.
Matthew Bond: And they published something called the DC to ac resistance ratio. This is back in the thirties.
Andrew Hutchison: Wow. Okay. Yeah. All right.
Matthew Bond: Tell us about that DC to ac resistance ratio in that they compared all of the wire gauges, american wire gauges, 22, 20,18 and 16,14, getting progressively larger, and the best in terms of the lowest dc resistance and the lowest ac impedance, if they call that resistance, was an 18 gauge wire.
Andrew Hutchison: Okay.
Matthew Bond: So it was. It was the most linear in terms of frequency response.
Andrew Hutchison: So kind of a sweet spot in. In wire. And so, yes. And so. And we’re talking about individual strand diameters at this point. Right?
Matthew Bond: So conductors. Yeah. An individual conductor.
Andrew Hutchison: Yeah, yeah, yeah. Okay, so. And now keep going.
Matthew Bond: Dick Olsher got this information as well. He didn’t get it from me, but he. He happened to get it as well.
Andrew Hutchison: Yeah.
Matthew Bond: And, so this. This knowledge has been. Is nearly 100 years old.
Andrew Hutchison: Well, you know, they do say nothing. Nothing. Nothing. There’s nothing new under the sun.
Andrew: Your cable won Stereophile shootout with 218 gauge conductors
so, so you, in your design that you had submitted to Stereophile to win this shootout, your. That was a cable that you sent did involve this, 18 gauge sweet, spot.
Matthew Bond: It did, yeah.
Andrew Hutchison: Okay.
Matthew Bond: 1 mm is the metric equivalent.
Andrew Hutchison: Yeah.
Matthew Bond: And, so a pair. When I say a pair, 218 gauge conductors. Insulated. Each of them. Insulated. Twisted together.
Andrew Hutchison: Yes.
Matthew Bond: Made a positive run. And then you twist another pair together to make a negative run.
Andrew Hutchison: Yeah. Okay.
Matthew Bond: And so that was. That was one channel.
Andrew Hutchison: Okay, so, in fact, I. You per, cable to run from, you know, say, the left channel of the amp to the left speaker, the cable run was really just four one mil, diameter conductors. Is that the gist of the cable construction?
Matthew Bond: That’s it, Andrew, yes.
Andrew Hutchison: Wow. Okay. So, I mean, I mean, you know, some of the simplest ideas are obviously the best. So, this was up against. And I’m imagining, and imagining it was a more affordable option than some of your american made rivals that were in this Stereophile shootout. Is that.
Matthew Bond: Absolutely. The cable was regarded as a. As a bargain. M. And de Golsha wrote that, that it was a bargain at its price. Other cables are going for. Well, I should say that the phase two speaker cable was 695 a foot. And so you could have a class a pair of speaker cables for a few hundred dollars.
Andrew Hutchison: Yeah.
Matthew Bond: And I was up against, cables costing 20 and $50 a foot.
Andrew Hutchison: Wow. Which, of course, back in, what?
Brad Serhan: Back in 88.
Andrew Hutchison: 88, yeah.
Matthew Bond: Yes. God knows what that is today.
Andrew Hutchison: It’s, big bucks, clearly. So, So yours was. Yeah, super affordable, considering class a rating by Stereophile. And so I just want to linger on that, success for a second, but I’m just not sure. I mean, you’ve covered it. I mean, you submitted the cables. They won the shootout. They were not just the best sounding cables, but the most affordable. And so you were making these at this point, presumably
00:10:00
Andrew Hutchison: in your own facility by hand or something? Or, I mean, what was the insulation material? How was that working?
Matthew Bond: Simple polyethylene.
Andrew Hutchison: Okay.
Matthew Bond: And when I say simple, a better insulation material than PVC. and I didn’t know how neutral polyethylene was as compared to teflon or other dielectric materials. Insulation materials. But, it’s a very good insulation material on a very good dielectric, too.
Andrew Hutchison: Okay.
Matthew Bond: There’s other choices. Like another good, good insulation or dielectric material is polypropylene.
Andrew Hutchison: Yeah.
You spent years experimenting with different wire gauges to determine best sound
And you run some experimentation at this point, or had you mainly concentrated on getting the wire sizing and I guess the composition. So this is some, I imagine, some high purity australian copper, was it? I hope.
Matthew Bond: Yes. But let me explain a little bit.
Andrew Hutchison: Sure.
Matthew Bond: I spent years, listening to different wire gauges. And the 1 next up is a 17 gauge at 1.14, then above that at about 1.2 is a 16 gauge conductor. The larger you go in conductor sizes, the more high frequency roll off there is. So if you wanted a warmer sound than 1 mm, you would go for something like 1.2 mm. But I had compared all of these and the one that sounded the most neutral is, is 1 mm, just happens to be. And, which is a nice size.
Andrew Hutchison: Isn’t it?
Matthew Bond: Amazing, really? Yeah.
Andrew Hutchison: I mean, it’s sort of the basic basis of the metric system is the. Is the best sounding wire gauge size.
Matthew Bond: yeah, I, listen to a number of things such as, not just wire of different gauges, but wire with and without insulation materials. So I had a very good idea of what insulation material sounded neutral or sounded the least bit, the least bit, of color, I was going to say.
Andrew Hutchison: So. In fact, I always wonder about this because I read something somewhere and I you know, I’ve never really made cables. maybe some silver interconnects once or something. But based on, you know, a bit of hocus pocus. Internet, talk maybe. Although I think it was pre Internet. So maybe, maybe just talk around the campfire. I don’t know. But the. But the, idea of no insulation at all is slightly intriguing. So did you. I mean, obviously it’s tricky to make practical, but did you, Did you, experiment with, like, no insulation versus some or whatever practical insulation you need in the real world? And this was, and I’m driving at back then. So prior to letting, Stereophile hear your current model at that point, yes.
Matthew Bond: Yeah. I’ve listened to, conductors without insulation, and when I’m not letting them sit around to oxidize, you know, people may be thinking that.
Andrew Hutchison: Yeah.
Matthew Bond: you know, I’d be listening to raw conductor, spaced about, Let me try to convert some millimeters now about 6 mm apart. That’s about a quarter of an inch. and then I would listen to the same, conductors and, with insulation on them. So I was able to determine which insulation sounded the most neutral or colored the sound, the least.
Andrew Hutchison: Yeah. Okay.
Brad Serhan: Were there large variations between, you know, what you heard? Was it sort of obvious?
Matthew Bond: no, they were subtle. They weren’t obvious. PVC actually sounds terrible. It distorts the mid range. And then, materials like polyethylene and polypropylene are the most neutral. And then, of course, you’ve got Teflon, which can be extruded at a very, fine coating, like as thin as human skin. one layer of skin. That’s pretty impressive when you can get wire coated with teflon at that thickness.
Andrew Hutchison: And you can safely, twist. Well, you’re not twisting opposite polarities, though, are you? You’re just twisting. No, you twist a pair and then. And then how. How far apart would the two twisted pairs be, the negative and m positive?
Matthew Bond: Well, between three inches and six inches. And here’s the funny thing. You think about speaker cable and you don’t think that capacitance matters, but, putting this, putting the positive and negative runs apart from each other.
Andrew Hutchison: Yeah.
Matthew Bond: Does make a big difference. So capacitance does matter.
Brad Serhan: Well, yeah.
Andrew Hutchison: Not as much as inductance that removes any capacitance. Having them that far apart, does it? Is that the point or.
Matthew Bond: No, it doesn’t. It doesn’t get much better than about
00:15:00
Matthew Bond: three inches. I mean, at three inches, you could have it. So at about 1012 centimeters, it’s far enough apart that it doesn’t matter anymore.
Andrew Hutchison: Yeah, yeah. Okay. Yeah. But, but certainly that’s that distance. The three inches is much better than, say, half an inch or something like that. That’s.
Matthew Bond: No doubt about it. You know, some dealers would use zip ties to put the positive and negative run together. I didn’t, I didn’t, I didn’t let on. I just let them do what they wanted to do.
Andrew Hutchison: Yeah, well, they were doing that with their own. With their own creation. Not with your cables, because you’re right. Did you have your cables separated by a series of spaces or something? Or how did you maintain that?
Matthew Bond: Well, original. Originally. Yeah.
Originally I was using sheets of cardboard and matchsticks and glue to put the cables together
Originally I was using sheets of cardboard and matchsticks and glue to put the. I know.
Andrew Hutchison: Some Australian made quality right there.
Brad Serhan: Oh, yeah. It’s hot.
Matthew Bond: Yep. Mate.
Brad Serhan: I’ll huff and puff and I’ll blow your house down. I mean. Yeah.
Andrew Hutchison: So, okay. So that got you where you needed to be, like, consistent. Three inches.
Matthew Bond: Yes, yes.
Andrew Hutchison: Okay.
Matthew Bond: And I, you know, I would, in the interconnect, interface, do the same kind of thing. Single conductors, not twisted pairs.
Andrew Hutchison: Yeah.
Matthew Bond: But, I was able to make interesting observations about how far the positive and negative conductor needed to be in an interconnected interface. And, that’s very interesting because there is a lot of capacitive coupling. When you get the positive and negative, say they’re insulated. When you get the positive and negative conductor twisted together, you get so much capacitance that the high frequency bandwidth is rolled off. In fact, in fact, for every doubling of capacitance, which is kind of common in a twisted pair, for every doubling of the capacitance, you reduce. You reduce the high frequency bandwidth by a full octave.
Andrew Hutchison: Okay. All right. And then. And what is it rolling off? At what sort of rate is it, disappearing at when you. When you.
Matthew Bond: At about six decibels per octave? Right. Right in there.
Andrew Hutchison: Oh, really? Well, okay. Which kind of makes sense, I suppose, if it’s effectively creating a capacitor. So. Yeah, yeah.
Matthew Bond: Very audible. And, And the magic happens when you get the conductors positive and negative for an interconnect interface at about a quarter, at about six, 7 mm apart. And you get an even better improvement when you can go to about 12 mm apart, which is what I do in the best interconnect cable I make.
Andrew Hutchison: Okay.
Andrew Hutchison: Right. Well, we, we note that you are making cables still today, but maybe we fill some of the gap in a little bit.
So you before we jump to what you’re up to right now. So the review goes swimmingly
So you before we jump to what you’re up to right now. So by the way, you’re being extremely generous with this, information. Because I’m not sure I’ve seen it floating around the Internet. It feels like feels like it’s not something that you sort of shout about. And it’s certainly not highlighted on the Internet. Maybe I’ve just in the wrong corner of the Internet and haven’t noticed. But the, so the so the review goes swimmingly. you’re now the king of, cables. Over nightly. I mean, I guess you’d been doing it for some years beforehand. But like all overnight successes. you know, it appears to the public at least that it’s an overnight, success. And so, what’s the step after that? So you’ve I mean, you’re obviously back at ces the next year, I would imagine. Or had you already moved at this stage to America?
Matthew Bond: I moved to the United States, to prepare for the CES show. I was there in late 87. Before the CES show in January of 88.
Andrew Hutchison: Okay.
Brad Serhan: Did you return to Australia after the 88?
Matthew Bond: Yes. Correct, Brad? I did.
Brad Serhan: Did you have the shot still?
Matthew Bond: Yes. It was for a short time. Yeah. And I had to sell it to sell the business and move. I packed everything up. And I had to back over to the United States by around, September of 88. So the review came in July. And three months later I was forced to move to the United States permanently.
Brad Serhan: Forced, just to permanently.
Andrew Hutchison: Fantastic.
Matt, I remember you had a shop called music by design
Brad Serhan: Matt, I remember you had a shop called music by design.
Matthew Bond: Right.
Brad Serhan: In bondi Junction. where you were selling all sorts of HiFi equipment. And and you had your workshop out the back, didn’t you?
Matthew Bond: Yes, but I wasn’t selling all sorts of HiFi equipment, Brad. I was badly voted sorry. In terms of loudspeakers. I was focused on your loudspeakers, because they were so good for the money. And they were really producing better sound.
00:20:00
Matthew Bond: additionally, you know, people from Perreaux the electronics amplifier, pre amplifier company from New Zealand. Came to me and asked me to stock their stuff on consignment. and have it in the shop and and display it and play it. Well, it wasn’t that good.
Brad Serhan: Oops.
Andrew Hutchison: Whoops. Hang on. We’re gonna that we you can absolutely say.
Matthew Bond: I mean, it’s all business anymore.
Andrew Hutchison: they actually are. I mean, we this is not going out live, Matthew. You can say whatever you like. And if you go over the what we consider to be the edge then we can always chop it out.
Brad Serhan: But what’s called pixelation. Yeah, we can pixelate it, so to speak.
Andrew Hutchison: But.
Matthew Bond: Okay.
Andrew Hutchison: I mean, obviously, I don’t know if you remember because I don’t know whether it used to be as bad, but there’s a fairly strong still, New Zealand versus Australia rivalry. And I. And, Obviously, any opportunity to chuck off at anything. Kiwi is always welcomed.
Brad Serhan: But,
Matt: Did you have DNM speakers as well? Didn’t you have
To the point about. Well, just quickly, Matt was making a point, no doubt about.
Andrew Hutchison: Oh, no, I want to hear about the sound.
Brad Serhan: But I was going to say there was Gary Morrison, who designed Plinius, who’s a magnificent designer. Wonderful, wonderful man. and he also designed the pure audio amps. And also, there’s a few Kiwis that we do admire, like Simon, from the wand. And, the Lambert speakers were pretty damn good. Weren’t they as well? Didn’t you have.
Matthew Bond: Yeah, they were the original Lambert loudspeakers with the, poly fabric, tweeter. Before Gary went to the ribbon tweeter, he had a better sounding range of loudspeakers, which is all that I was selling. So Lambert. A little bit of Richter, some. Sorry.
Brad Serhan: Yeah, sorry. Yeah, there’s Orpheus. Yep. That’s. But there was. You also had. Did you have, Some english stuff like, was it logic turntables as well?
Matthew Bond: Yeah, logic turntables. Mission electronics and mission loudspeakers, which were pretty good. The big pair.
Brad Serhan: Yeah.
Andrew Hutchison: But.
Matthew Bond: But no, I never had any DNM product. But I. But I’m.
Matthew Bond: There was somebody, a representative, a, Manufacturer’s representative who wanted me to stock, And sell DNM speaker cable. You remember him, Brad? I do. Okay. So, And it just sounded. It was inferior. It was tin, tin plated copper in a pvc ribbon. Basically the stuff that you see inside computers, hooking boards to boards.
Andrew Hutchison: Yeah. Okay. And, Somewhat well, in your. In what you’ve taught us so far for using probably the worst material. So,
perreaux asked you to display and play pro amplifier line
But just, just. We’ll just, just close the case on the perreaux thing. So perreaux asked you to, Ask you to, have a. Well, to, to, as you say, display and play the, the pro amplifier line. And you didn’t find the sound to be that impressive as you remember it was.
Matthew Bond: I recall it was thin and metallic sounding. Didn’t have any power. There was no drive from the power amplifiers.
Andrew Hutchison: Yep.
Matthew Bond: The mission electronics called Cyrus. There was a Cyrus one and Cyrus two great amplifiers. They could. Yeah, they could power the Lamberts or the missions.
Andrew Hutchison: Yeah.
Matthew Bond: and Brad’s loudspeakers, the Orpheus loudspeakers, they would, just blow away the perreaux electronics. There was nothing I could do. Months later, they, called me or they were calling me on a regular basis. But I finally told them, I said, you just got to pick this stuff up. It’s not going to work for me.
Andrew Hutchison: Yeah, yeah, yeah. Oh, that’s interesting. That’s a good little story. I like that.
You bought some Cyrus in the early nineties when you were selling them
so you would have, you would have dealt with, dealt with, Ian Bultitude, I guess, for the Cyrus stuff. Was that who you, do you remember who you were buying?
Matthew Bond: No. No. The importer at the time was a guy called David Seath. SDH was his last name and he was in Victoria.
Andrew Hutchison: Okay, so he must have taken over in the late eighties or something like that because I had dealt with him in the very early nineties when I started selling a bit of Cyrus. And,
Matthew Bond: Right.
Andrew Hutchison: Caught the tail end of the good stuff, the Cyrus two, Cyrus one, you know, in the plastic simple, square box. And then, yeah, they moved to the, their new, casting, the Cyrus three shaped chassis in the early nineties, which was, I don’t think it, frankly, it sounded, I don’t think they ever sounded as good as the more crummily built, Cyrus one and Cyrus two, which may or may not have been very well made, but they, they sounded just, they just sound like music. Lovely.
Matthew Bond: Lovely.
Andrew Hutchison: Alrighty.
Andrew, you started your audio equipment business in Oregon in late 88
So you, you’d, you had to pack up in a hurry and shuffle off to where the action was. And, and what was that action? What was, were you getting orders or were you getting some kind of manufacturing deal or something? What, tell us about that.
Matthew Bond: People were calling
00:25:00
Matthew Bond: in every five or ten minutes. The phone would be ringing. they would mail checks, more often. And, I had to, I had to hire two people immediately. Two younger guys. yeah, I can’t remember their names so long ago now, but, they would be making up the speaker cables, the phase two speaker cable, and interconnect cables as well. So this was 80, late 88 going into 89. And in late 89 I couldn’t stand, I forgot to say that I was still in Los Angeles, but I didn’t want to be there anymore.
Andrew Hutchison: Yeah.
Matthew Bond: An awful city to live in. And the drop and the commute is impossible with the traffic and the freeways.
Brad Serhan: So no such thing as, public transport?
Matthew Bond: No, there’s no public transport. Well, there’s some bus routes, but that’s all. Yeah. They need to do something.
Andrew Hutchison: they still do. I think it still is lacking in public transport. But anyhow.
Matthew Bond: Yeah, it’s terrible. So I decided to move to Oregon. I had a couple of people recommend where I should move to.
Andrew Hutchison: Yeah.
Matthew Bond: And I moved up to Oregon. I was blown away by the green trees everywhere and the small, population.
Andrew Hutchison: Yeah.
Brad Serhan: Was that Ashland at that stage back?
Matthew Bond: Yes. Ashland, Oregon, which is a really pretty town.
Brad Serhan: Yeah.
Matthew Bond: And you know, lucked out being able to get a, building that was being constructed about. I don’t know how to express it in square meters. So we’ll just have to leave that for now.
Andrew Hutchison: Divided by ten, is it? Yes.
Matthew Bond: Okay. So about 500 m² is what I had as a, as a factory.
Andrew Hutchison: that’s a piece, pretty serious space. Yeah.
Brad Serhan: Sizable.
Matthew Bond: Yeah, yeah.
Matthew Bond: originally I had about five or six people. That grew to about 30. About ten years later.
Andrew Hutchison: Yeah. Okay. Wow. So, I mean, I mean, I hate to use the expression overnight success, but if there’s ever been an example of it, this could be.
Brad Serhan: It certainly, it certainly does feel like it was wham, bam. Well, it was, it was quick.
Andrew Hutchison: So, I mean you, it was exciting times for you. I mean, you must have been, I mean, did you, you know, I guess we’re getting into sort of generalizations here and less to do with actual audio equipment. But I mean, psychologically, was it, did it feel great? Was it exciting? Was it scary? What, what, I mean, it must have been very interesting times.
Matthew Bond: Honestly, Andrew, I firstly, I was 28, 29, 30 years of age. And it was just happening so fast. And I was just working so hard.
Andrew Hutchison: Yeah.
Matthew Bond: I had some distributors in other countries, so I had to travel to visit with them and do, presentations describing the products. Technically, doing, what are they called? PowerPoint presentations.
Andrew Hutchison: Indeed. Yeah.
Matthew Bond: Maybe they came later, I’m not sure.
Andrew Hutchison: It started about then, I think. Yeah, yeah.
Matthew Bond: I was, I was doing quite a bit of traveling internationally. And over the years I’ve, I’ve trained probably over a thousand salespeople in different countries, different continents.
Andrew Hutchison: Yep. How to.
Matthew Bond: So I was just busy and you know, I had people come, come to me that that would work for me to run the business. Bookkeeping and accounts and all of that.
Andrew Hutchison: Yeah. Yeah.
Matthew Bond: So I did not at any time do anything more than. Didn’t have to do anything more than just stay creative. Designing cables and traveling and teaching.
Brad Serhan: There’s not much time for that euphoric you know, that euphoria, that wonderful sense. Wow, I’m here.
Matthew Bond: Oh yeah.
Brad Serhan: So head down, bottom up.
Andrew Hutchison: Yes, well that’s. I suppose that’s the reality. The. If you’ve got orders piling in, I mean I’ve. I had a time earlier, early this year where we just had a run on repair, requests, that was just every hour and big jobs.
At this stage the cables are all kind of handmade. I mean, I realized that they’re hand stripped
And it happened, it went on for about a month and we immediately became four and five months behind. And it was actually not terrifying, but it was comforting in the sense that, you know, where your next, you know, meals coming from. But on the other hand, you run out of space in the workshop to put people’s goods. And then further to that you, it’s, you’re like, I’ve got to get all this stuff done at some point. It’s a little bit in the same way as what I’m alluding to with you was that you had all these orders, you’ve still got to make them all. And I guess training people was. I mean this is, you know, at the risk of sounding like an old, good old dude, but you know, like, was it easier to
00:30:00
train people back then? I mean, you clearly needed people with soldering skills and real care and attention to make these things happen.
Matthew Bond: Yes.
Andrew Hutchison: I mean, because at this stage the cables are all kind of handmade. Is that the gist of it?
Matthew Bond: It’s still the case today. But to go back in time, I taught two people at the same time and then a third person came along and that person became the factory manager, was a lady named Mary, and she was doing a fabulous job making the cables. it doubled to six, then doubled to twelve. And you know, we were really pushing out a lot of product. Interconnects were more difficult to make than speaker cables because the speaker cables were coming off a roll and just needed to be terminated.
Andrew Hutchison: Yeah, I guess. I guess what I meant. I mean, I realized that they’re hand stripped and soldered. But, The actual. Yeah, so the cable itself is coming off a roll at this point. You’ve got someone making it, a cable maker making it for you, presumably.
Matthew Bond: Yes, but we’re doing a lot of assembly in house.
Andrew Hutchison: Yeah, yeah.
Matthew Bond: You know, to make a pair of interconnects today we’ve got a pair of tubes, Teflon tubes. Conductors get inserted into the Teflon tubes, then a mesh constrains the twisted pair of tubes and then around that is a spiral cut tube, around that is more mesh. And so we’re definitely building the cables by hand. There’s quite a number of parts going into it.
Andrew Hutchison: Yes, absolutely.
Brad Serhan: Oh, that’s incredible.
Matthew: Tara Labs stands for the absolute reference audio in labs
Andrew Hutchison: And so I don’t know whether we, it just occurs to me that we haven’t possibly mentioned the business name, which was at this stage. It was Tara Labs, which is what you had always, worked under, you know, in Australia. And then, and then, well, you know, you’re then selling, based in Oregon, selling them on a worldwide basis. Tara Labs is an acronym, as I remember, for something, but I can’t remember what it is. Can you just illuminate us, please, Matthew?
Matthew Bond: The awful resistance audio. No, but seriously, seriously.
Brad Serhan: But seriously, folks, did it have something to do with time? Matthew, I can’t.
Matthew Bond: No, no. Well, we have a brand for the product, but Tara stands for the absolute reference audio in labs.
Andrew Hutchison: Okay.
Matthew Bond: And space and time was a brand name that we used for the speaker, cable, space and time, phase two. but everything.
Brad Serhan: That’s right.
Matthew Bond: Everything later became, came under the name Tara Labs. Tara Labs.
Andrew Hutchison: Yeah. Okay. And I mean, so, so this continued through the nineties. Is that the gist of.
Matthew Bond: That’s right, yeah.
Andrew Hutchison: Okay.
Matthew Bond: Yeah. Yeah.
Andrew Hutchison: And at some point, I guess the heat went out of it. I mean, is the, is the brand still around in some form these days or not?
Matthew Bond: Oh, yes. It’s a smaller business now than it used to be. But I, That we’re still. Or they are still making quality products.
Andrew Hutchison: Yeah.
Matthew Bond: And, Really, good products at, a whole range of price points.
TARA Labs invented rectangular section conductors in 1992
Andrew Hutchison: Okay. All right. Using, using your ip, I guess. I mean.
Matthew Bond: Yes, yes. Well, I was the sole founder of Tower Labs and, And everything was my design.
Andrew Hutchison: Yeah.
Matthew Bond: So, so, you know, I spent most of my time listening and creating new cables. based largely upon the phase two design. I created improved and better products, parts that were more revealing. Then in about 1992, I introduced a product called, in, introduced a product called rectangular solid core, which were.
Andrew Hutchison: Yeah, yeah, I’d forgotten about that. Yeah, there was, when I had, when I was selling tara labs, later in the nineties, I think it was maybe mid nineties or something. It, Yeah, there was rectangular section conductors. So what, what?
Brad Serhan: Yes.
Andrew Hutchison: So you got experimenting with that, obviously, during, you know, the early nineties, I guess, during your, designing phase. And what was, what was the advantages or disadvantages? Well, it’s clearly, the disadvantages are making it. The advantages were obviously audible improvements.
Matthew Bond: Yes. Basically it works like this. If you’ve got an 18 gauge conductor or 1 mm conductor, we say that’s an optimum diameter for having an even dc to ac resistance ratio, but with a rectangular conductor. So imagine that you take the 18 gauge 1 mm conductor and you flatten it.
Andrew Hutchison: Yeah.
Matthew Bond: you can tune the speed, the, you can tune the frequency response to some degree.
Andrew Hutchison: Okay.
Matthew Bond: And you can make it like two or three. If you could melt two or 3.5 millimeter
00:35:00
Matthew Bond: conductors. If you could take three of those or two of those, rather, and melt them together and make a rectangle, then you’ve got the high frequency roll off of a 0.5 mm conductor, which is to say you’ve got greater linearity with frequency. And, but you’ve got the same dc resistance as your round, solid, 1 mm conductor.
Brad Serhan: Clever.
Andrew Hutchison: can I just. I just like to say I’d like to have a break for 1 second.
Loudspeakers made in Brisbane, designed by Australians, manufactured by Australians
And it’s that time in the show again where we talk about our own products, pretending it’s an ad. Dellichord Loudspeakers made in Brisbane, designed by Australians, manufactured by Australians, using australian materials in an australian factory. If you like the idea of an australian speaker, we can help you. Have a look at the website now. Dellichord.com.au. Thank you very much for listening back to the show. Matthew was regaling us with his, in part one of the, of, today’s podcast. he was regaling us with his, somewhat amazing story, of seemingly overnight success in the cable business. and we were up to, I suppose, some time in the early nineties when you, I suppose, under a successful regime, could design whatever you want. And, you developed, the parrot sounding cables. Who’s got the parrot? Someone’s there.
Matthew Bond: Brad, are you playing with something?
Brad Serhan: No.
Andrew Hutchison: Poly.
Brad Serhan: What a cracker. I mean, no, I I’m not.
Matthew Bond: I.
Brad Serhan: Seriously, it’s, it’s from my front window. We’ve, we have a fair bit of bird life here. There’s a few parakeets, crows, magpies.
Matthew Bond: Okay.
Andrew Hutchison: It sounds like.
Brad Serhan: Oh, yeah. And kookaburras went. And if the kookaburras start, well, it’ll be worth having on. On the show.
Andrew Hutchison: Absolutely. Okay. Yeah, that’s, that’s.
Brad Serhan: My apologies.
Andrew Hutchison: No, that’s fine. So, Yeah, the,
Matthew, how do you make a rectangular conductor? How’s that work
So you, Matthew, you had or were working on or had. Well, you ultimately launched the rectangular. I, guess it’s, I guess all cables extruded to some, some degree. I mean, how do you make a rectangular conductor? How’s that work?
Matthew Bond: It’s extruded and, they start with a, round conductor. Large, round conductor. And then it’s fed into something that melts the cable or softens it. And then it goes through a die. And that die makes it, shapes it.
Andrew Hutchison: Yeah. Okay. Simple as that in one way. And, but, and so it had certain properties. I mean, you literally, as you were alluding to, you fine tuned the, sound, I suppose, to some degree of your original 1 mm round diameter conductor. And you. And you got greater high frequency extension. Is that, is that the gist of it or what were the other advantages? That rectangular?
Matthew Bond: No, that that’s it. Well, it doesn’t have the high frequency roll off that an equivalent gauge in a round conductor has.
Andrew Hutchison: Okay.
Matthew Bond: So the rectangular conductor just wins. And, if you make it smaller, you can. You can have a, Having to think now, 22 gauge is pretty, small. But I’m not sure how to convert that to millimeters right now.
Andrew Hutchison: Honestly, I’m not sure.
Matthew Bond: With me, I’m guessing it’s like anyway.
Andrew Hutchison: .6 or something, is it or, .7.4.
Matthew Bond: Maybe some number like that. And so that was also made into a, into a, rectangular conductor. So we had small conductors extruded and that became the measured 25 thousandths of an inch across and eleven thousandths of an inch high. And I’m sorry, but I can’t convert that to metric.
Andrew Hutchison: It’s about point. So this is about 0.5 by 0.25 or something like that. Is that. Did you. How many thou was it? Was it 1020?
Matthew Bond: 5000Th across?
Matthew Bond: I think this 44 millimeter.
Andrew Hutchison: 44. I think a mil is 44 or 41 thou, I think, from memory.
Matthew Bond: Oh, you’re right, Andrew. That’s correct.
Andrew Hutchison: What are you learning? I’m always run.
Brad Serhan: Must be back when you’re doing your car days manufacturing cars, Andrew.
Andrew Hutchison: Oh, yeah. When I wasn’t doing other things, yeah. you know, I. Vague memories of it. I mean, I, you know them. M. Yeah, I sort of work in both languages to some degree as far as measurement, but, But yeah, thousands of an inch is still a popular, you know, old school mechanics. You know, I’m measuring things, you know, in thou. So, It. So, yeah, so about half a mil by 0.25 of a mil. Matthew, is that. That’s that you reckon? Or a little bigger than that?
Matthew Bond: I think it’s smaller than that. I think it’s smaller than that.
Brad Serhan: It’s minutiae. Let’s get going.
Matthew Bond: It’s a small conductor. And that can be insulated in polyethylene or teflon. And, then the interesting thing is
00:40:00
Matthew Bond: that the little rectangular conductor becomes flexible because of the extrusion of the polymer over it.
Andrew Hutchison: Yeah.
Matthew Bond: and, it can. Then you can have a group of them twisted around the Teflon tube. And that means you can get a 14, two millimeter square conductor or a four millimeter squared conductor. you can. In terms of complete cross section or current carrying capability.
Andrew Hutchison: Cross section, yeah.
Matthew Bond: So then you can build with these insulated rectangular conductors, you can build a very large cable. And at tower Labs, we would build, some cables that would be two gauge in size, which is pretty phenomenal. And these cables were called the omega. And Michael, Fremer from. Originally from Stereophile, now with Tass, the absolute sound magazine, he still raves about the part, and it’s in his system permanently.
Andrew Hutchison: Is that right? Okay, that’s an impressive, salubrious connection there. So, So he. Yeah, so he’s had them for 20 odd years. obviously.
Matthew Bond: Yes.
Yeah. . Interesting. A long time. Yeah. Okay.
Andrew Hutchison: Yeah. Okay.
Matthew Bond: Yeah. A long time.
Andrew Hutchison: Yeah. Roddy. Yeah. Interesting.
Matthew Bond audio makes extremely low-cost speaker cables
so continued success with Tara labs. but jumping forwards, you. You have a, new company, I guess, or a new business name.
Matthew Bond: Matthew Bond audio. Yeah. And, audio. I’m doing things a little differently. We hit. We. At our labs, I hit the maximum, in terms of developing product.
Andrew Hutchison: Yeah.
Matthew Bond: And, the company at the time, with partners, had determined that they were very happy with the product range and didn’t want any new inventions or advancement in technology.
Andrew Hutchison: Okay.
Matthew Bond: So after being bored for a year or so, I decided to leave.
Andrew Hutchison: Yeah.
Matthew Bond: it was an amicable separation.
Andrew Hutchison: Yeah.
Matthew Bond: And, I created Matthew Bond audio so that I could make it a new design of speaker cables, with extremely low inductance and, interconnect cables with extremely low capacitance. And, I make some cheaper cables, less expensive cables, too. the insight and intrigue series of cables. Okay, so I’ve got a good range of products from about a few thousand dollars up to 15, or $18,000 retail. not the most expensive on the market. There are kales going for 50 and $60,000 from audioquest and other makers. Absurd prices. in my mind, I can justify $15,000 retail because it takes about $3,000 to produce a very high end speaker cable. But 50, $60,000, that’s just pure greed.
Andrew Hutchison: Yeah. look, I was lucky enough to be at an audioquest demonstration evening, and, where they did play those 50 $60,000 cables. And they sort of step you up through the range and illustrate and demonstrate the, improvements along the way. And I have to say they do get better and better. And there’s no doubt that the $50,000 cable sounds better than the, the 8000 or the $2,000 cable. But if we spent the $50,000 on a better pair of loudspeakers and a better amp, not to mention a better stream, a cd player or turntable, I mean, obviously there would be, A considerable increase in performance, I would have thought.
15% or so of system value should be cables, not 30%, Matthew says
Do you have any idea or any sort of philosophy, Matthew, on the. How much you spend or what you should spend or the balance of expenditure on cable versus hardware? to.
Matthew Bond: I do, as a matter of fact, something that I created about 20 years ago. And that is a simple rule of thumb. 15% or so of the system value should be cables, not 30%. That would be. That’s just craziness. Loudspeakers are extremely important. And, the source, components are very important also. But if you want a really amazing changing system, I think loudspeakers make the biggest difference of all components.
Andrew Hutchison: Yeah. I have a feeling Brad will agree. But, I’ve pondered this. I actually concur. As far as the cable expenditure. That’s pretty much what I’ve said forever. As I’ve said, about 10% of the value of the speakers. Which, Which is actually probably a bit less than what you’re saying. Because you’re
00:45:00
Andrew Hutchison: alluding to $15,000 of the value of the complete system. but I also said that as a minimum, you know, that that was, you know, anything less than that was probably you were. You were not getting that part of the system potentially right. But,
Matthew Bond: Right.
Andrew Hutchison: But, Yeah. So, yeah, this this I grew up at a time and slightly tainted by the Lynn. The whole Lin name era. and I say tainted because, you know, mister Lynn used to say, yeah, that the turntable was the only thing that mattered. And you should spend about $3,000 on a turntable. And probably $250 on a pair of speakers. And at the time, I felt that was kind of wrong. But I. I guess it depends what aspect of performance that you’re chasing. But you like to spend more money on speakers for what? For what reason, Matthew, what’s what’s your, What do you feel you get when you spend more money on a loudspeaker?
Matthew Bond: Well, just to cover your point, Andrew, about the turntable in its day, that wasn’t was a pretty important component, you know, Rega or Rega, however you say it, in Australia, a Rega turntable, was a very good. Purchased at about six or $700 australian some 2030 years ago. I had a Linn LP 12 very early on.
Andrew Hutchison: Yes.
Matthew Bond: the basic Linn LP twelve was my go to turntable. It felt. It sounded better than other turntables. But the rega was very good at about six or $700. And, I went to the trouble of rewiring the tone arm and even creating, at my storm music. By design, I would create a way that the VTA could be adjusted in a rega tonearm and RB 300, I think.
Andrew Hutchison: Yeah, it was the original one.
Matthew Bond: Yeah, yeah, yeah. Anyway, they’ve got quite a range now of turntables and, Sure, they’re doing very well.
Andrew Hutchison: Yeah, but keep going. Yeah.
Brad says loudspeakers should be 30% to 50% of the expense
Matthew Bond: Coming back to what I was originally, saying, I would say 15% to 20% on cables, but the loudspeakers ought to be 30% to 50% of the expense.
Andrew Hutchison: Okay.
Matthew Bond: I just feel that they’re so important because I could play a pair of, say, $20,000 loudspeakers and I could use a small triode amplifier putting out 10, 15, 20 watts per channel.
Andrew Hutchison: Yeah.
Matthew Bond: And a trio tube amplifier, of course.
Andrew Hutchison: Yes.
Matthew Bond: And m if the loudspeakers have 89 or 90 decibels or 92 decibels spl that reasonably efficient, then, I’m going to have a really good sound.
Andrew Hutchison: Yeah, yeah.
Matthew Bond: I mean, back when I was, 18 or 20, I had, quad. Two amplifiers. The original quad amplifiers.
Brad Serhan: Classics.
Andrew Hutchison: Yep.
Matthew Bond: Yeah. Pair of infinity loudspeakers and the Linn LP12 turntable.
Andrew Hutchison: Well, that’s actually, you know, it’s a pretty good combination, isn’t it, really?
Brad Serhan: That is a good.
Andrew Hutchison: I mean, I don’t know. We don’t know which infinity is, but, I mean, infinity made some great speakers back then. So,
Matthew Bond: Yeah, they were called RS7s. I recall they were three way loudspeaker.
Brad Serhan: Did they have a ribbon?
Matthew Bond: They had a ribbon and the emit tweeter. And this is how I got into the wiring cable business to begin with.
Andrew Hutchison: Okay.
Matthew Bond: One of my. The left channel tweeter went dead. So I carefully unscrewed it, not showing whether there was gonna be springs and wires flying out at me. So, yeah, to undid the tweeter and I looked at the back of it where the wire was, and it was this cheap automotive clips and, the worst wire of all, and I didn’t know what it was. Insulated in.
Brad Serhan: But basically damn stream.
Matthew Bond: Yeah. I had I had the notion, the idea that the, Wire was really bad.
Andrew Hutchison: Yeah.
Matthew Bond: So, You know, I’d been messing around with wire. And I rewired the infinity loudspeakers. Both channels, got the new emit tweeter. And The change or the improvement was absolutely stunning.
Andrew Hutchison: Okay. Wow.
Brad Serhan: So that was the catalyst in a way, for you to.
Matthew Bond: It was the catalyst. Yeah. It really was, Brad.
Brad Serhan: It was a penicillin moment, if you like.
Matthew Bond: It was you know. Because so I thought I have to really get into Making speaker cables and interconnect cables and all of this. And, at the same time monster cable was out with a product called powerline two. And I foolishly got a set of those, brought them home. And they sounded God awful.
Brad Serhan: In the nicest possible way.
Andrew Hutchison: Did you connect them up to the Perreaux gear just so they could feel at home?
Brad Serhan: the pro now is magnificent. So to be fair. Yeah.
Matthew Bond: I mean, it may be. Maybe. I don’t know.
Andrew Hutchison: Oh, yeah.
00:50:00
Andrew Hutchison: No, we I was I was I was actually repairing something the other day. And It had a it was an older one. It was actually probably not as old as when you were selling it. But when it finished, it sounded quite good. But it’s it’s it does have that mosfet. It was a power amp. It does have that kind of Mosfet. Slightly soft sound. And I think I know what you mean with the the lack of drive. Is that they don’t seem to have as much sort of don’t have that bipolar transistor grip in the bass that say, well, obviously say an a fire absolutely has. So I yeah, they do have quite a, Z sound. Which I guess is if that’s not what you want is it’s not going to be to your taste. And they don’t sign sound like that anymore. Of course, the newer ones are actually well, I guess they don’t use Mosfets anymore. no one seems to. Actually almost no one. So, you know, I think they’re quite different.
Brad Serhan: But just a quick one on that. On the Lin son deck. In that period of time. Matt and Andrews. That there is the garbage in, garbage out principle.
Andrew Hutchison: Yes.
Brad Serhan: Coming from Julie. Oh. Ivan.
Andrew: It’s really important to have good front end
Andrew Hutchison: Ivan.
Brad Serhan: Sorry.
Andrew Hutchison: Yeah.
Brad Serhan: within Sondek. And then the name combination. But it was quite a powerful thing back in the eighties. With the english HiFi. media. Which was prolific back then. With a whole lot of magazines like HiFi news, record review. HiFi answers. Popular HiFi Jesus
Andrew Hutchison: No, there was unpopular HiFi, the.
Brad Serhan: Not so, but hi fi questions.
Andrew Hutchison: Yeah, yeah.
Brad Serhan: And answers. There’s a lot, put it that way. And, they’re very supportive, and, they proselytized that whole theme in a sense. You know, garbage in, garbage out. Get the decent turntable.
Matthew Bond: Good front.
Brad Serhan: Great front end. And then you could have a cheaper pair of speakers to. To run off it, so.
Matthew Bond: Well, I think that’s just, I think it’s ass backwards. it’s really important to have, a good front end. There’s no doubt about that. There is no doubt. No doubt. Today we’re streaming digital electronics. We’ve got, the potential to have much better source material than we’ve ever had. and again, the loudspeakers are really important. And I have had a whole range of loudspeakers over the years. electrostatics, ribbons, mag, magnepans, sound labs, she just caught an array. Yeah, these loudspeakers, you know, had some incredible loudspeakers.
Matthew Bond: But I guess what Brad is making now and. Andrew, I don’t know what you’re making. I I would love to hear a pair of your loud speakers at some point.
Andrew Hutchison: Well, thank you. They’re, they’re, Well, probably the one that we are probably the most proud of because it’s the better product is, in fact, an active loudspeaker. So it sort of rules out some of the, Well, rules out, you know, half of your, half of your product range because we don’t need any speaker cable. But, But yeah, you know, I mean, in fact, just to jump sideways, do you. Do you come to Australia anymore? Do you get out here much? What’s the situation there?
Matthew Bond: Just, well, my parents, unfortunately, have passed away.
Andrew Hutchison: Yeah.
Matthew Bond: So I don’t have a reason to come down there.
Andrew Hutchison: Yep.
Matthew Bond: I try to get back there about once every two or three years.
Andrew Hutchison: Okay. So pretty.
Matthew Bond: And it’s. It’s wonderful getting there. You arrive at about 06:37 a.m. in Sydney and force yourself to get through the whole day without falling asleep.
Andrew Hutchison: Indeed. Yeah. Yeah.
Matthew Bond: And, you know, I love getting a meat pie and sausage roll.
Brad Serhan: And the maggot bag is they called.
Matthew Bond: What are they called?
Brad Serhan: They called a maggot bag and a coffin. The sausage rolls called coffin. Coffin.
Matthew Bond: Remember me?
Andrew Hutchison: Yeah. We don’t. Yeah, that’s a new South Wales thing. That’s. Well, I don’t know. We just have pies and sausage rolls. But, you know, try not to eat them too much. But yeah.
Brad Serhan: Yummy.
Andrew Hutchison: It is weird. Yeah. And I think we do fish and trip. Chips. Trips. Chips. Trips properly. not to say that America doesn’t, but I’m bloody sure England doesn’t. I mean, England might make the most magnificent amplifiers and speakers, or at least they think they do. But I tell you what they can’t do is fish and chips. And yet they’re supposed to be renowned for it. I know. We’re going sideways. Is that right? I hate the fish.
Matthew Bond: Yeah, he’s right.
Andrew Hutchison: It’s overly, overly battered, overly fat, soft, gooey, bloody. The worst. The worst.
Brad Serhan: Flaccid chips. Is there anything worse than a flaccido domingo chips? Wow.
Andrew Hutchison: So, Yeah.
Matthew says when you fly into Sydney, it’s stunning from the air
Do you think when you fly in, Matthew, and agree with me that when you fly into Sydney, at least it’s. It’s flying into the most magnificent looking city from the air in the world.
Matthew Bond: It’s stunning to have the left hand window seat.
Andrew Hutchison: Yeah.
Matthew Bond: As they fly in towards, mascot. And, you look out the window and you’ve got the harbor bridge and the opera house.
Andrew Hutchison: Yeah, absolutely.
Brad Serhan: It’s.
Andrew Hutchison: Morning. Yeah.
Matthew Bond: Yeah.
00:55:00
Brad Serhan: In the harbor.
Matthew Bond: And.
Andrew Hutchison: The harbor that. The harbor and just the beaches and just, you know, if it’s. And I guess I’ve done it more, actually, coming from the us, I think, back to here. And, I mean, it’s, you know, it’s, this. I mean, San Francisco, obviously, which you’re not too far away from. I mean, obviously 5 hours or so away or whatever you go there from time to time, I guess. But I mean, it is a, magnificent harbor as well, but it’s so often shrouded in, fog and mist and what have you.
Brad Serhan: A mystery. A mystery fog.
Andrew Hutchison: Yeah. Whereas Sydney, it’s bright and shiny and I mean, the light. The light in this country is so. Well, you could say it was harsh, but it’s, It’s very bright, bright colors. And, of course, northern him is northern hemisphere. In many areas, not so much so,
Brad Serhan: Although it ages the shit out of us.
Andrew Hutchison: Oh, God. Yeah. Yeah. It doesn’t do our skin any good.
Brad Serhan: Uv.
Andrew Hutchison: Yeah. So, we’ve,
Matthew: In a speaker cable, it’s important to reduce inductance
So you say you’ve got your new business, you’ve got your new designs, and the new designs, are, ah, somewhat, well, using new ideas. So. And I see that on the website you’ve got like a. I don’t know if braided is the correct term, but you’ve got a. A cable that appears to be a mass of conductors, and they’re interwoven to some degree. What do you. Can you tell us, Matthew? Obviously, that’s a different thought process than than your previous captain.
Matthew Bond: Well, we’re talking there about inductance, and the speaker cable m. It’s important to have positive and negative conductors close together to lower the inductance, hopefully to a point where the loud speaker and the amplifier are coupled with the electrically shortest amount of, cable possible.
Matthew Bond: So we’re trying to take the cable out of the interface.
Andrew Hutchison: Yes.
Matthew Bond: By lowering the inductance to a point where it’s, it’s, it’s not audible to the, To the listener.
Andrew Hutchison: Yes.
Matthew Bond: And Just explain that a little bit. The electrical current or the signal are flowing, in the conductor from the amplifier creates an electromagnetic wave and the wave travels through and around the conductor. and as you guys probably know, this electromagnetic m wave induces a current that flows in the opposite direction and that opposing current impedes the flow of the wanted signal. And this force is known as back EMF.
Andrew Hutchison: Yep.
Matthew Bond: In a speaker cable, it’s important to make the inductance as low as possible to reduce the back EMF m. And that’s.
Andrew Hutchison: And so there’s a sense of that.
Matthew Bond: Design you see on the website. Andrew?
Andrew Hutchison: Yeah. Yep. Okay. And what do you feel, Matthew, is the, Is there a key audible, obviously audible, but a key audio quality benefit related to much lower induction?
Matthew Bond: Absolutely. it is as if there is no speaker cable in the interface. So the best way to compare that is to have an amplifier behind the loudspeaker with a short like 1ft pair of simple, cables compared to a longer shed. And you really hear the difference in your loudspeakers. Andrew, where you’re going active, you’ve got a short piece of speaker cable going from the amplifier to the to the drivers. And that’s the best possible interface. I support active loudspeakers. I understand why you would do it. There are, you know, without active amplification, without active loudspeakers, you’ve got the challenge of finding a set of speaker cables that sound good. And the problem for me is that there are too many, what I call cocktail cables out there. A mix, of, materials, in some cases copper, silver, platinum, I don’t know. They just make up this stuff and, you know, it sounds different. So, yeah, you know, we don’t have, in the lexicon of audio words, we don’t have something that reviewers I found and cable manufacturers definitely don’t know the basics of audio cable design. And a lot of this can come down to measuring the capacitance and the inductance, assuming that the resistance is low. Ah, enough. Yeah, so we’re not talking about cables that, are, you know, in one case made of carbon fiber and being so resistive that the signal can’t flow from the one component to the other. Who did that?
Brad Serhan: What? That’s.
Matthew Bond: Am m I allowed to say I’m, not?
Andrew Hutchison: Well, we can always
01:00:00
Andrew Hutchison: bleep it out if we feel that it’s an issue. And it’s that time in the show again, where we talk about our own products, pretending it’s an ad. Dellichord loudspeakers made in Brisbane, designed by Australians, manufactured by Australians, using australian materials in an australian factory. If you like the idea of an australian speaker, we can help you. Have a look at the website now. Dellichord.com.au Thank you very much much for listening back to the show.
Matthew Bond from Matthew Bond audio discusses carbon fiber audio cables
Hi folks. Andrew here at not an audiophile. today we’re with Matthew Bond from Matthew Bond, cables, or Matthew Bond audio, in fact, that mainly makes cables, in the US. And we’ve of course got the, ever popular Brad, Serhan also assisting in the background doing what he does best, silence. So, it’s all about the noise.
Brad Serhan: Floor, by the way, and you’re keeping the noise anyway. You continue, mate.
Andrew Hutchison: Sorry. Well, Matthew mentioned, as he describes them, cocktail audio cables, which, is an expression that I quite like because the point is that you’re mixing different materials, sort of in a concoction to create some kind of new flavor sensation. Is that, is that, that’s the gist of it, Matthew. And then you, you mentioned someone once made a, ah, cable, or the most ridiculous material perhaps, was a cable from carbon fibre, which might have been at the time when carbon fibre was first invented and everyone was using it for everything. got any thoughts on the carbon fiber? potential, if you like.
Matthew Bond: I just want to say this before I go to carbon fibre, and, and that is that I, There are so many cables out there, they all sound different. None of them sound perfect. There are words like clarity, detail, transparency, and they get often used in reviews, magazine reviews. And this is where I think the reviewers are doing us a disservice, because there’s no way of saying, there’s no way of, there’s no lexicon that helps us to understand what is perfect. And electronics, theory. As I said earlier in the podcast, if we go back to the 1930s, there was knowledge and science back then. it got rediscovered by Dick Ulster in 1988. I’m working with it now. So it’s nearly a hundred years of, knowledge that just isn’t observed or really understood.
Andrew Hutchison: Yeah.
Matthew Bond: In the lexicon of audio, we don’t have words that help us to understand that the cable is nearly perfect, that it’s, in the case of a speaker cable, that its inductance is so low that the interface or power transfer from the amplifier to the loudspeakers is optimal or nearly perfect. You know, we’ve got all these other words that really lead us into colorations and distortions of the audio signal by saying, oh, this loudspeaker cable, has a warm and palpable mid range.
Andrew Hutchison: Yeah.
Matthew Bond: You know, it’s as if we’re reading something describing wine. You know, I’m going to have black BlackBerry fruits and, Yeah, Chocolate on the palate.
Andrew Hutchison: Yeah.
Brad Serhan: You know, Chuck book thrown in for good measure, apparently so, yeah, that’s a.
Matthew Bond: It’s a pretty decent carbon, though. Back to carbon, though. So this was used some 1520 years ago as a conductor. And in many reviewer systems, the cable just didn’t work. So it was used in the interconnect interface. And, what happened with all of the complaints is that the manufacturer, started putting conductive metal conductors in parallel with the carbon fiber conductor.
Andrew Hutchison: Really?
Matthew Bond: So that there would be a signal going from the, source to the load components. And, the electrons and the signal are going to find the path of least resistance, of course. And so we’re listening to a new cable, not a carbon fiber cable.
Andrew Hutchison: Yeah.
Matthew Bond: Manufacturer had a $250,000 pair of loudspeakers some years. Not loudspeakers. Excuse me. Loudspeaker cables, $250,000. Yeah, I just didn’t have my checkbook ready. And, And, He said, first he claimed that there was no resistance in the cable. And I’ll explain why. He used a tank of liquid nitrogen purged into tubes inside which were the conductors.
Andrew Hutchison: Yeah.
Matthew Bond: And, his explanation was that the,
01:05:00
Matthew Bond: cables had no resistance because they were frozen. He didn’t say to what exact temperature. Of course. We’re looking for zero degrees kelvin or -270 I think.
Brad Serhan: 273.
Matthew Bond: Yeah. Excuse me, guys. I was off.
Andrew Hutchison: Yeah, I know you off my throat.
Brad Serhan: It’s critical, though.
Matthew Bond: It’s critical. That last. Cool. So at 273 degrees, celsius -273 celsius. I asked him about that and he demurred, let’s say. And then he claimed that the inductance was also zero, which I said to him was impossible. And he said, why is that? I said, well, if you take an inductance, a component in a crossover, and freeze it to any temperature, you’re still going to have inductance.
Andrew Hutchison: Absolutely. I would imagine. I haven’t tried it.
Matthew Bond: He said, well, I don’t have any inductors in my speaker cable.
Andrew Hutchison: Oh, sorry, inductors or inductance. I mean, obviously no inductors.
Matthew Bond: He said, the components. And so I didn’t know what I was talking about.
Andrew Hutchison: Yeah. yeah. That was his comeback.
Matthew Bond: I tried to explain to him that the same principle would apply to the inductance in the speaker cables, but he said, no, that is, that’s zero also. Anyway, I, I gave up and walked away. And this is a guy that’s been in the business for, I guess, 40, over 40 years and should know better. But anyway, yeah, so you, there’s some amazing stories to tell you about cables in the cable business.
Matthew: There are some cable makers who make deliberately colored cables
Andrew Hutchison: Well, yeah. So you’ve gone off, we’ve turned a corner into a different side street here, which is, we’ve gone down sideshow alley, effectively, which is, into the slightly kooky side of the cable business. because clearly that is a part of. Well, maybe it’s a. We don’t know. I haven’t analyzed the cable market, but I guess there are some makers who, I guess their design goals are, to make the best looking cable that has some unique feature. And, you know, you mentioned platinum, I think, when we were talking about cocktail cables. no, not plutonium, platinum. And, you know, so, I mean, is that, that’s a sector of the cable business that’s not doing people such as yourself many favors. Because if you are, looking at it, from an R and D point of view of making a seriously better and transparent sounding cable. There are others who, as you allude to, literally making a fully flavored cable, one that’s actually purposely colored sounding, which, I guess is, I guess is how, you know, I mean, that’s how you, it’s easier to hear a more obvious tonal shift. And, you know, there’s a, the brand of cable that I think you might have been alluding to is certainly a cable that you can plug many of their models into your system and go, oh, well, that’s made a difference because they, they certainly had an obvious character. But, and there’s others I can think of. I, don’t know what you think of. There’s a few different versions of this style of cable. They’re very very flat ribbon style speaker cables. Have you got any thoughts on those, Matthew, as to whether that’s whether that’s all show or is there some function to those cables?
Andrew, talk about non uniform current versus frequency distribution in the cable
Matthew Bond: Well now we’re going to touch upon non uniform current versus frequency distribution in the cable.
Andrew Hutchison: Okay.
Matthew Bond: What that means is that the conductors that are at the center one positive, one negative are coupling capacitively, the inductance being lower in that pair of positive and negative conductors. And then we’ve got more conductors moving to the outside of the ribbon cable and they have obviously lower capacitance but higher inductance.
Andrew Hutchison: Okay.
Matthew Bond: So it’s a screwed up cable and
Andrew Hutchison: Okay.
Matthew Bond: And it’s not delivering what I would call something close to perfect in in terms of signal transmission or current versus frequency.
Andrew Hutchison: Yeah. See here’s the thing. It’s interesting isn’t it, that the the better the cable genuinely is the the less actual sound of course it has of its own, would you say? I mean it’s it’s because I mean it’s like amplifiers that don’t have a lot of character. And I can think of one in particular that I mean people say you know the ideal amplifier is a straight wire with gain. But people hate those amplifiers. They they want to, they want some particularly sweet sounding tube amp or some incredibly highly detailed and somewhat to my ear bright nasty sounding transistor amp. They they want an amp with character it seems when in reality you know in the good. Yeah. That the
01:10:00
Andrew Hutchison: theoretical You know hope is that you have this amplifier that has no sound quality. It just literally makes the signal big enough to drive a loudspeaker. Is that that what your cables were doing and your current ones?
Matthew Bond: Andrew M. My goal is to produce A cable that is absolutely neutral.
Andrew Hutchison: Yeah.
Matthew Bond: And absolutely having no electrical or electrical. Electrical colorations distortion in the interface. the amplifiers that you mentioned are not unlike listening to different cables. But the goal in my view should be to have a system that recreates live musical event. So maybe it’s a small recording in a studio, but it’s been miked and mastered particularly well. And Mike’s amplified and mixed. And all this is done so well that when you play it on a two channel stereo system you get the images in the space between the loudspeakers. Maybe even around the loudspeakers in some cases. I’ve heard such recordings played back.
Andrew Hutchison: Yes.
Matthew Bond: And If you can get that happening where it seems like there is a real female vocal in the center and there are musicians playing. Well that’s nirvana. That’s it.
Andrew Hutchison: Yeah, agreed. Of course. And It’s actually really hard to achieve, which is kind of I guess Many audio enthusiasts frustration is that They Well half of them don’t know what to aim for because they’ve never really heard a truly great stereo system because it’s actually really hard to find one demonstrated for a variety of reasons. And then the others Well I think they go about it in a. In an odd way and there’s whatever, whatever makes you happy. But yeah, you know it when you hear it, that’s for sure. Yes and I. At Munich this year I heard a couple of things that I just found jaw droppingly amazing. And those demonstrations get no press so I don’t understand the world. And It’s one reason why I’ve kicked off this podcast is just to mainly maybe just talk about some of the other things that are out there that people just do not see in what has become what is the mainstream audio media. Which I guess is a lot of YouTube reviewers these days. Clearly Stereophile are still at it, absolute sound is still at it. And some of those english magazines are still at it. But But yeah, the brands that I’d never heard of before. And some of it was expensive equipment and some not so much, but amazing demonstrations just as you were alluding to. Very lifelike the timer of the sound and the way the balance. Very natural. And That’s hard to achieve, And As I say, you know it when you hear it. but I tell you what, it’s It’s mostly not how the audio business seems to work.
Matthew Bond: I guess it’s no, we choose products based on given Colorations. And Some people would like a forward sound, some people will like something that’s well balanced, some people will like more. More detail, some people want it softer.
Stereo should have image outlines that defy our imagination, Brad says
That’s interesting of course, but it’s To my mind not what a real audio file should be trying to put together. We should have the recreation of the, of the live musical event and There should be image outlines that defy our imagination and get us to believe that we’re listening to a live performance.
Andrew Hutchison: Yeah, absolutely. Look, and I guess there is, there is personal preference and taste in here somewhere. because you know people like different music and different music is presented completely differently. Obviously if you go to a stadium rock event or pop music event. It’s completely different to, you know, hearing some small jazz group in a tiny club, playing almost acoustically. So, you know, I guess not every stereo will do all of those things. But, I mean, so maybe that’s what leads people up particular paths. as far as. I mean, there’s people who like, you know, there’s a swag of people that love LS3/5a. And a majority of the listing public. And the industry thinks that they’re a joke. but they do certain things incredibly well. But you’d have to be happy with a small scale of performance. whereas, of course, other gigantic loudspeakers do an excellent job
01:15:00
Andrew Hutchison: of reproducing the sound of a bird. And,
Brad Serhan: Brad, I’m sorry about that. That’s an. That’s that’s the local indian miner.
Andrew Hutchison: oh.
Brad Serhan: Is it also not any.
Andrew Hutchison: Is that the dark one? Is that the blacky brown colored one?
Brad Serhan: No, that’s not that one. That’s. That’s the imported one, if you like. But this is actually a local one. And it’s,
Andrew Hutchison: Oh, the gray.
Brad Serhan: Quite territorial.
Andrew Hutchison: The gray colored.
Brad Serhan: The gray. It’s gray with a yellow beak.
Andrew Hutchison: Yeah.
Brad Serhan: Yeah.
Andrew Hutchison: And rowdy.
Brad Serhan: That and rowdy. And I apologize. That’s popping.
Andrew Hutchison: It’s not a problem. But it’s just as, I mean. So, I mean, I guess, Matthew, you. You can accept that people have different, I guess, persuasions or interests in music. But ultimately you still want a cable and an amplifier. But to talk cables that is largely transparent. That’s,
Matthew Bond: That’s right.
Andrew Hutchison: That’s the goal.
Your cables are not inexpensive. But is there a modern day, affordable cable
So have you got, Your cables are not inexpensive. People who have a decent budget should perhaps look into them. But for someone who’s wanting to spend $10 a foot or $6.95 a foot. But these days, like your cables were back, that got you started. Is there anything that’s any good that springs to mind? Not that we want to advertise. I mean, it’s not really conflicting with, what you’re selling. But I guess what I’m saying is there a modern day version that clearly has to be made less expensively than yours were made back in the day. But is there a modern day, affordable cable that you like?
Matthew Bond: Yes. Well, the phase two has evolved into what we call the intrigue speaker cable. And I intend to reintroduce the phase two speaker cable at a reasonable price so that people can have it. And an interconnect to match so that people can have access to something that’s affordable and it’s coming out in the next few months.
Brad Serhan: really good news.
Andrew Hutchison: Sounds like a setup that we’ve. I had no idea. Okay, so that’s, that’s, that’s great news. So you’re going to, you are going to have an affordable cable.
Matthew Bond: Oh, yeah. So, I. The reason is that, in the beginning of the podcast, we talked about, my discovery with wire diameter or size, and insulation, and then how the phase two speaker cable was made. Your listeners are going to be able to say to themselves, I think I can make a pair of speaker cables. And they’re right.
Andrew Hutchison: Yeah.
Matthew Bond: So for a very, for a very affordable price, they can put together a pair of speaker cables that will blow away most of the competition.
Andrew Hutchison: Okay. But for those that are less handy, you going to make, we will be.
Matthew Bond: Developing a reintroduction of the phase two and a matching, interconnect.
Andrew Hutchison: Wow, that’s that’s exciting news.
Andrew Hutchison: You were going to say something.
Brad Serhan: The question I was just, pondering. I just want to go back to something that we were doing back in the old Orpheus days. And we were fiddling around with, internal speaker cable wiring. So, And just remembering how particular the cables had an effect. But I should mention that later on we’ll come back to it. Sorry. Well, actually, it’s a prompt.
Andrew Hutchison: Was it your speakers, Brad, that had just single strand, fairly stiff sort of aviation kind of cable in them?
Brad Serhan: Is that what was stiff but not aroused? Put it that way.
Andrew Hutchison: How do you make, how do you make that happen?
Brad Serhan: Well, that’s why I learned that from Matthew Bond, actually. Now, but in all seriousness, I’ve taken a. I’m so glad because when you mentioned the fact that you’re reintroducing, the cheaper cable, more accessible in a sense for a lot of people. It reminded me of the days when I was wiring with some of the early days, I was using summer Matthews solid core.
Andrew Hutchison: Maybe that’s what the cable was that.
Brad Serhan: I gave me permission. And then when I ran out of that because Matt went to the states, left me here alone. in all seriousness, but so we’re using that solid core internally and it made a difference. The interesting thing about that was that we were using also stranded cable in the mid, mid nineties, went back to stranded cable on the cheaper, awful speakers. Matt and I sort of stuffed this. We couldn’t get any more of Matt’s stuff, which is fair enough. but I was using some solid core which was 0.5 mm matte with. No, it was one mil. It was what you were saying. actually it was one mil with Teflon on it.
Matthew Bond: Very good.
Brad Serhan: And we were using that. We did blind tests. So we got the stranded cable and then we had two or three pairs of speakers and we sort of. And we did sort of these tests. And the one thing that you could pick out with the. Even though I didn’t know what was inside, kept my business partner at the time and Nick Hanson had set up so we could sort of. I blind test. And the one
01:20:00
Brad Serhan: thing that gave way was listening to the clash. I fought the law and the law one. Not a bad recording.
With the stranded cable, it was like. Everything was well defined in its space
But you mentioned the fact that outline the outlines of the actual performers, the instruments, the brass or whatever it might have been. With the stranded cable, it was like. It was bird. You know, if you have. Haven’t filed a metal. You know, metal piece. And it’s sort of. You’ve run your hand on. It’s rough and it can catch your skin. Whereas with the solid core it actually. It was defined. A defined body, if you like that. That’s the way I describe it. Everything was well defined in its space. So, It was blacker. I. All the blacks were blacker.
Matthew Bond: Yeah.
Brad Serhan: If you like, around this instrument. So this sort of quietness to it and an outline of the image. A more defined outline. So even in a short cable run inside the box it made a difference.
Matthew Bond: Yes. And Brad and I have a. Have An experience, That we shared. I’m not sure if I could go into that, Brad, but something to do.
Andrew Hutchison: With the stiff but not around.
Matthew Bond: Seriously now. There was a track that I would play, Andrew, that I thought the vocalist was singing showcase. And it was actually suitcase. When we had the. When we had modified the system. Changed the system.
Andrew Hutchison: Okay. Yeah.
Brad Serhan: This was at the CES in 2008 or 9.
Andrew Hutchison: Yeah.
Brad Serhan: And. And It was quite a revelatory moment because Matt put on this great blues, singer.
Andrew Hutchison: Yeah.
Brad Serhan: Great recording. And, Matt Bond. Well, it was a change of speakers. But we changed speakers from one pair of speakers to another pair. And then Matt stopped the whole proceedings in front of a whole lot of people. Said like a mad professor and stuck his finger in the air, waggled, said, it’s suitcase. He went to the station with a showcase in his hand. I’ve not seen many people go to a station with a showcase. Maybe some trying to flog watches. But the key thing is it was a, suitcase. So, yeah, it was a, Wonderfully, wonderfully. A wonderful shared experience, that one.
Andrew Hutchison: I think I was there, which I’ll.
Brad Serhan: Tell you a bit about later, because that was the catalyst for the Mu2.
Andrew Hutchison: Is that right? Okay. Oh, yeah.
Brad Serhan: But that’s another story. Let’s refer back to it.
Andrew: So this strap, this single stranded cable bra that you were using
Andrew Hutchison: Okay. Well, I’m, And, yeah, just. Just to close that, we probably might wrap today up, because I think we’ve all done very well, as. As a tv show once used as a catchphrase. I think that was. You’ve all done very well. But anyhow, the point is that, So this strap, this single stranded cable bra that you were using was. Did have white insulation on it. Is that. Is that.
Brad Serhan: Yeah, it did. It was, It was. It was a Phillips, cable, which was. Had Teflon. And it was one mil diameter and mattered past the 1 mm diameter theory, on to me, in a sense. We were using his cable internally.
Andrew Hutchison: Yes.
Brad Serhan: And then when I ran out of actually very quick stuff that. We’ve got time, we can cut it out. So, Matt, I was using your cable internally for quite a while, and then I ran out. You were in the states and all that sort of stuff, and I got another solid core, and it must have had a different insulation on or whatever. But, we bung it in, the Orpheus minotaurs. And, a mate of mine, Fred, sneering, her and pair of minotaurs, he was testing them. I can’t quite remember. He said, they sound shit. He just was straight to the point. They don’t sound right.
Andrew Hutchison: Okay.
Brad Serhan: And I realized, oh, God. That’s the, That was a different, solid core manufacturer. So I had some stairs, leftover stuff from. From UMat, and basically rewired it and restored it back to its glory. So even solid cores, our, oils ain’t oils, and solid cores ain’t solid cores.
Matthew Bond: There.
Andrew Hutchison: M. You go. Okay.
Brad Serhan: M. So it might have been the insulation, as Matt was saying.
Matthew Bond: Yeah.
Andrew Hutchison: On that front, we probably didn’t cover. And we will maybe make this the final point, because I feel like, matthew, that we’d love to have you back at some point in the near future because you’re. I’ll come back to my point about copper purity is my question. But,
Brad Serhan: Yes, Andrew.
Andrew Hutchison: Yeah. Just.
Matthew says new speaker cable will retail for about $1200 in Australia
But before I become back to that, I do want to, wrap up also on your new cable, which is great news. So that’s. You said perhaps out in the next few months or something like that.
Matthew Bond: Yes, I’ll have some. I’ve already got the interconnect product produced and it sounds wonderful. And here in the states it’s going to retail for about $1200. But I am going to be sure that we, I’m going to be sure that we have price parity in Australia. So it’s going to be available to australian audiophiles before the end of the year.
Andrew Hutchison: Yeah.
Matthew Bond: That is December 2024.
Andrew Hutchison: Yeah. Roddy, not good news.
01:25:00
Andrew Hutchison: So not far away. And, and so the the speaker cable, similar price point do you think.
Matthew Bond: Or a little bit higher. About $1500 australian for a pair. And I don’t know whether these numbers are high or low. I just know that that’s what we can sell them for in Australia. I think that if you’re buying a pair of loudspeakers for $5,000 then a pair of speaker cables for about 1000 or $1,500 is about right.
Andrew Hutchison: Yeah. No, it just doesn’t sound completely unreasonable at all. And it does fit with your 15% of the value of the system, That you’re alluding to earlier. So look, I think that’s Not that we’re here for marketing advice and you wouldn’t ask me about marketing advice anyhow, but I think that’s probably right in the sweet spot of serious cable purchases, budgets I would have thought. I mean clearly it’s not the average Joe who’s putting together $3,000 system. It isn’t going to be for him. But, but Yeah, I think for many many customers buying good stereo systems or building them and Improving them with you know additions etc. That, that’s Right in the sweet spot I think. Yeah, absolutely.
Matthew Bond: Well that’s good.
Brad Serhan: It’s in, it’s in the realm. It’s in the realm isn’t it? It’s just, it’s, it’s a. Yeah, it’s a good price point.
Andrew Hutchison: I think once you get to three or 4000 it’s. I think for a lot of people that’s into That’s definitely into esoterica and And then you know, I mean, and I don’t know my experience. I mean I did import straight wire cables for many years, And made some success out of it. But it’s, it’s a brand that’s not probably well marketed anymore. They still make good cables. And certainly That, that segment was, I mean it was under a thousand, was more popular but then we were probably. I don’t know, but we, but we. But of the more expensive cabals, over a 1000, 1500 was the sweet spot. But that’s a few years ago and I think prices have changed since then. I think that Covid and the inflation we’ve seen worldwide in recent times means that an old price point of just under 1000 is probably now 1500. So, you know, I think. You know, I mean, I think it’s the same over there. Is it, Matthew, that the pricing has gone up to hell?
Matthew Bond: So it’s amazing. I mean to go to the supermarket and get your regular bags of groceries. food has doubled in price.
Andrew Hutchison: Wow. Has it really? Okay.
Matthew Bond: Yeah.
Andrew Hutchison: Ah, yes. Well I guess it’s probably similar here. Although I am a sucker for a special. So if you only buy anything, I mean, so woolies and Coles and even Aldi, where we go to all three. But they, they’re they have specials all the time. I just buy the specials and prices probably have not doubled, but they’ve certainly everyday pricing is absolutely doubled up. Thank you.
America used to have the cheapest fuel in the world almost
So just on that front, fuel pricing in America has gone through the roof, hasn’t it? Used to have the cheapest fuel in the world almost, except for Saudi Arabia. But how much is a gallon of gas these days?
Matthew Bond: What’s, what’s what kind of octane?
Andrew Hutchison: well how about the good octane? If you had a proper car, like an interesting car that needed in Australia in terms, we’d say 98, which over there I think is a lower number. but you know, one of the more expensive petrols, not diesel, actual,
Matthew Bond: I can tell you, $4 a gallon. For supreme.
Andrew Hutchison: For supreme. Okay, $4 a gallon. So Aussie dollars, that’s, I don’t know. Is that 650 or something a gallon then divided by what’s 2.2 us gallons? 3.76 or something, isn’t it? And I. And now my head hurts. But anyhow, I think, I think your fuel, I think your fuel is still cheaper than ours. But it used to be dramatically cheaper.
Brad Serhan: Yeah, yeah, we’re about to down in Sydney, right? About $2 for what we used to call super or never standard and super. Now, it’s 98. If you’re talking $98, sometimes $2 a litre.
Andrew Hutchison: Yeah. But then in us dollar terms that’s a dollar 30 or something. And it’s or dollar a bit more. And So multiply that actually. Yeah, I mean it’s Yeah, yeah. Us fuel price.
Andrew: There must be a lot of Americans complaining about high gas prices
So you’ve I know we’re getting distracted here from, but just talking prices for a second. I mean, fuel is kind of a bit of a guide and always. So, I mean, there must be a lot of Americans complaining about the price of fuel because they’re the driving f 150s, right? So.
Matthew Bond: Right. Well, Andrew, the thing is that, the fuel is not the same price in the, in every state. In California, it’s more like instead of $4 a gallon in Oregon, it’s $6 or $7 a gallon in California.
Andrew Hutchison: Is it, is there that much difference?
Matthew Bond: Oh, yeah. And then in Alabama, Mississippi, it’s about one third cheaper than Oregon.
Andrew Hutchison: Okay.
Matthew Bond: So they’re paying, they’re paying about 250 a gallon in Alabama.
Andrew Hutchison: So that’s what, that’s a state tax
01:30:00
Andrew Hutchison: thing.
Matthew Bond: specifically, taxes really have a, have an impact.
Andrew Hutchison: See, California, it’s A lot of people, a lot of Californians are complaining about, all sorts of things about California. So you’re observing that, just in the, and the price of fuel. Well, that’s probably where I saw the crazy pricing and the complaining was more of a California price. okay, so you’re getting a bit of a free lunch there, but as far as, in the supermarket for groceries and everyday expenses, there much of a muchness across different states or is there still differences there?
Matthew Bond: No, no, you’d be right in saying it’s much of a muchness.
Andrew Hutchison: Yeah. Okay.
A decent craft beer here is somewhere between ten and $20 Australian
All right. And then ultimately, And I don’t know whether you enjoy a, tipple or not, but I mean, alcohol, this beer we were speaking of earlier is, has also gone up, but is still less expensive than here or because we do have the highest alcohol taxes in the world. So, and I think we really do. I mean, it’s outrageous. a decent craft beer here is somewhere between ten and $20 Australian. A can. One can, which is.
Matthew Bond: Are you serious?
Andrew Hutchison: Completely serious.
Matthew Bond: $10 for a can of beer.
Brad Serhan: Oh, I could see can or just a. What’s a skin or a pint?
Andrew Hutchison: You won’t get a pint in a bar for less than about 1213, $14. And it’ll be rubbish for that. A proper one will be, I guess, 14, 1516 onwards. and yeah, if you go to a craft beer, bottle shop, which is a, you know, it’s a bit of a boutique, I guess, but there is, there is no cans in the fridge for less than $7, give or take each, assuming, you’re just buying one. And there are cans in there for 20 and 30 and $40.
Matthew Bond: Unbelievable.
Andrew Hutchison: So yeah, you’re Jesus. Yeah. It’s odds. It’s utterly ridiculous. so yeah, if you want to buy a beer from Oregon in Australia in a craft beer shop, it will be between 15 and $30 a can. It’ll be a pint, an american pint. But, so decent sized.
Brad Serhan: What’s interesting is that I’m not a drinker. I’m not much m of a drinker. I’m not a drinker. But I’m thinking about the fact that that sort of Oregon beer that you’re talking about now with food, you can have slow, get slow good digestation, but you can’t have slow digestation with beer because it’s just go flat. Say, jesus, you just gotta, you can.
Andrew Hutchison: Sit on it for a while. But yeah, I mean, really, 20 minutes is, you know, but in 20 minutes it’s done. I guess it’s lost its mojo a bit. But,
Brad Serhan: Yeah. That’s a lot of money, isn’t it?
Andrew Hutchison: So do you, do you buy much local craft beer, Matthew, at all? And if you do, do you know what the price?
Matthew Bond: I’m not much of a drinker, but I know that I can get a schooner size or a pint of beer or craft beer for around six, $7.
Andrew Hutchison: Yeah. Okay. Yeah. In a, in a, in a restaurant or in a bar?
Matthew Bond: Yes. Yes. In a restaurant.
Andrew Hutchison: It’s a bit cheaper. And then is that including, you know, you’re tipping on top of that as.
Matthew Bond: Well or you’d be tipping on top of that, you know. And the regular tip is 15%.
Andrew Hutchison: Yeah. Yeah. So, yeah, it’s, it’s not a long way cheaper than here, but, yeah, the world is a more expensive place.
We would love to get you back on the show to talk about new cable
And so getting back to speaking cable, your, your speaker cables, I think at those and endurin, endure interconnect at those sort of prices are, you, know, probably on the money, I think. The interconnect, well, a lot of people don’t need an analog interconnect anymore, but the speaker cable, they still need. And I think that’s you know, I think you might have some success with that. So we would love to get you back on the show to have you tell us more about that new cable. I think when that’s, when that’s something that’s, finalized or you’ve got some imagery of it or it’s out there in the field or, you know, what have you. So, yeah, I’d like to speak again. And I’m sure there’s some other cable theory stuff that you could enlighten us with as well.
Matthew Bond: I’d love to.
Andrew Hutchison: Love to come back. That’d be great.
Andrew: I want to thank Matthew Bond for joining us today
Well I want to thank Matthew Bond today from Matthew Bond audio. Formerly Tara Lab cables, pretty well known brand and I think in the nineties which I suppose is a while ago now but you know it was a big deal. we’ve heard his great story of somewhat initial overnight success. I mean amazing overnight success. And then And then still you know at it still today as we all are. And thank you Brad for, for dropping in with a bit of extra input and for that matter organising getting Matthew on the phone so to speak now.
Brad Serhan: My pleasure Andrew. And thank you Matt for joining us.
Matthew Bond: Brad. Thank you Andrew. My pleasure. Thank you so much.
Andrew Hutchison: Thank you. Much appreciated. All right everybody, thank you for listening. And we you can find the podcast, all of our podcasts and information that goes with the you know photos, links to different things we’ve mentioned today all on the Not An Audiophile.com website. And there’s a specific page for this podcast which doesn’t exist now but it will by the time we’ve edited it and put it up. So
01:35:00
Andrew Hutchison: on that front Matthew send us some pictures and we’ll publish them on the website. And thank you guys and we’re off. We’ll see speak again soon. Thank you. Bye bye.
Brad Serhan: All right, thanks guys.
Matthew Bond: Bye.
01:35:09
SEASON 1 – EPISODE 002 – Matthew Bond, TARA Labs & Matthew Bond Audio
So anyway, the bottom line is I got the two pairs confused. Yeah, okay. you actually got them confused, confused. Like you didn’t get them audibly confused. couldn’t remember which pair was which. The ultimate blind test. No labelling.
Hello, welcome to Not an Audiophile. I’m Andrew Hutchison and today we speak with the assistance of Brad Serhan to Matthew Bond, the founder of TARA Labs Cables. We’ve spoken to him before. He mentioned in the previous interview that he’d done a lot of experiments with various cable configurations and today he discusses more of those and how they worked out.
Hello, Matthew, how are you going? Andrew, I’m doing well, how are you? Yeah, great, yeah, great. And you’re sounding good. Sound quality’s great. The amazing modern technology. It’s quite convenient, isn’t it? So much better than getting on a plane to do an interview like this. Hey, last time we spoke, we talked a little bit about…
at some length perhaps about the history of TARA Labs and some of the technology that you had experimented with and developed that got the world interested in your cables and you had to move to the US and start this amazing business from there and it grew almost exponentially I guess. But we did cover some of the tech behind it but I believe you’ve got a number of other
technically or technical related subjects that you’d like to cover today. And I’ve got a question as well about something that I heard on the internet on a podcast actually. And it sounded a a bit kooky really, but I’ll come back to that because I’ve got to form the idea in my head because it was quite complicated and a bit strange, but we’ll come back that. So,
And Brad, have you got questions for Matthew today along the lines of, you know, cable technology? Yes, I do. Andrew, I’ll have a couple of questions as we proceed through. Sounds a little bit like an inquest today, doesn’t it? Sounds very, or some sort of police thing, you know.
As if someone’s done something wrong. There’s a weight in the air. And it’s because we know Matthew is going to expose some flaws in perhaps some marketing arrangements of some cable brands, perhaps. I don’t know. He didn’t say that, but I suspect that something like that is going to happen. Matthew, far away, you’ve got thoughts. Tell us all about them. OK, if you just want me to…
get into it. Yeah, get into it. I do have thoughts.
What I’d probably like to start with is something that I call the Nines competition, which is a question of copper purity in a conductor. Sometime about 30 or 35 years ago Hitachi published a paper, a research paper with photographs of their engineers and they said that they they claimed they had created
6 nines copper 99.99 99 percent pure copper I’ve heard six nines copper and I do believe it’s better. Yeah, but I have real doubts about how it’s made because Copper purity is a process of electrolysis and
I can imagine how if you had a fine conductor and you were putting it in a bath of liquid and doing the process of electrolysis and the anode drawing impurities from the copper. But if you get a large conductor and even a block, an ingot of copper, I…
see that the impurities can only be drawn from the skin, the surface of the block or the ingot or the conductor. Yeah, that makes complete sense. Yeah. So that’s one thing. I don’t know if you have any comments about that, but that’s the first thing, the nines competition. you know, eight nines, for example, I’ve heard
a ribbon cable company claim that they’ve got eight nines copper and I doubt that’s really possible. I think these kind of claims should be supported by an assay certification. I think if you’ve got to publish this kind of stuff on your website, know, the material, the copper or the silver that you’re using needs to be assayed. That would be my point. Yeah, no, I, well, I
I have to say I’ve really not thought about the chemical process of purifying copper. I guess I kind of thought it was something that happened more during the mining phase or something where you’re digging it out of the ground and I guess you’re separating it from the gunk that it was involved with. But I have no idea. It’s not something that I have stripped a lot of cable. I’ve soldered a lot of copper wire.
I’ve never thought about where it really came from. I’m going to have to leave that one to you, Matthew, unless Brad has got some insight because he’s, you know, he’s part-time chemist. Yeah, in my dreams. the interesting point that Matt made is that if the 6N, you have doubts about the 6N, Matt, in terms of the way Hitachi did it? There’s a lot of claims in
cable in the cable industry. Sure. I don’t think that, and I don’t think most of them are true. You heard it here first. There’s a suggestion. It feels like an episode of Myth Busters. A suggestion for a second. don’t know. think for the, many of our listeners, the concept that claims from cable companies may not be completely true, might not come as a shock.
some it maybe it will. I reckon you’ve got others Matthew you say you’re doubting copper purity but you’re probably sorry to interrupt Andrew when you say doubting the purity to say the 6N
Have you listened to the difference between 4N, 5N, and 6N? Have you reclaimed the claim 4N to 6N? Have you heard that difference? I’ve heard a difference between ordinary copper, 2-9s and 4-9s, and I have listened to 6-9s. I do think it’s better. There’s a lack of harshness in the sound. There’s no doubt in my mind about that. But I question the process that they…
claim to have arrived at the purity. It’s not the only questionable technology. There’s No Continuous Casting, where you’ve got a block of copper going through a dye which is heated to about thousand degrees Celsius. I think that’s about right.
64 some number like that is the melting point of copper so they take molten copper and Extrude a ink and then get a small round
one centimetre in diameter by about six centimetres long, they extrude this rod and this rod is then sold to wire drawing, I’ll explain that in a moment, wire drawing facilities. Right. And you’ve got this hyper pure long crystal without crystal junctions, which we’re going to get to in a minute as well.
The idea being that
with this pure copper rod, passes through, when I say the idea, the fact is it passes through a progressively smaller hole through something called a die. So let’s say the rod is a centimeter or 10 millimetres in diameter. Then it would pass or be drawn through, pulled through a die.
of nine of with an opening of nine millimetres eight millimetres then next seven six five four three two one until you get down to one millimetre and that is how one millimetre wire is made yeah right okay the problem i have is that they claim that they have a single crystal longer than 100 meters right yeah that seems
I mean, is that the claim, Matthew, of some? That’s the claim. You can look it up. I decided I had to look into this, and so I did some Googling. Okay. So 123 meters or some number like that. So then you’ve got to realize that the copper conductor at one millimetre has to be spooled. can’t be pulled.
for 100 meters and left to dry or left to sit there. it gets spooled and somebody’s gonna say, well, how big a spool is it? Maybe it’s a one meter in diameter spool. They’re not. I’ve been in dozens of times, I’ve been in cable making facilities or factories. So typical spool is,
about 30 centimetres in diameter. with that you’re going to have crystals or breakages of the crystal and you will form crystal junctions in the copper that’s being rolled onto the spool. Yeah, clearly. So any bending of the cable will affect the mono crystal or break it?
Yes. This much I know. And also Matthew, suppose Ono Continuous Castings, the old OCC for those… Yes. …copper. So there is that. Have you heard a difference with that, the OCC? OCC? No, I haven’t. I haven’t spent much time listening to OCC. What is OCC for? That’s the single crystal.
The ONO continuous casting. Not to be confused with OFC as in oxygen free copper or whatever. Right, right. Which I guess is any copper, isn’t it? I mean, if it’s any kind of purity, it doesn’t have oxygen in it. that just while we’re on that? Because that’s a, it’s not a high end marketing term, but you know, OFC copper gets thrown around and has done for a long time. it, it’s simply, I mean, that’s just copper, isn’t it?
Matthew? Well, there’s, there’s something primitive in copper called tough pitch copper. And that’s the kind of copper that you would buy as inductors or transformers, magnet wire is what it’s called in the United States. Yeah, okay. So, I’ll say you stand it. So just to cut you off for a second. So your standard
We call it in Australia like winding wire. It’s something like a transformer maker or a motor rewinder would use, like just your standard enameled copper wire, which comes in all sorts of different diameters. So that’s not particularly great quality copper, just for clarity. That’s not… It’s a good but standard copper. Okay. So not oxygen-free. to OF… No, yeah, OFHC is the next step up, oxygen-free high conductivity. Okay.
That’s truly about four nines pure. Yeah, right here. And in your inductors, you’re probably getting OFHC. That would be my guess. Yeah. I don’t think you’re dealing with tough pitch copper when they’re making a winding wire. Right. Okay. So it’s pretty good quality copper then. Yes, it is. Yeah. Okay. I, and what was the other, what was the other, little,
marketing tool that some cable makers use that annoys you? There are things like, we just briefly touched on it, conduct a crystal structure and you know what I think about is theory versus reality, what can we hear? And in crystal structure you’ve got the idea
the claim that the crystals act like diodes rectifying the signal current. Yeah. You know, and we’re talking about a fine crack that can only be picked up by a microscope. And, and, you know, you may say, well, the current is, the small is the atomic structure, but it’s powerful enough that it obviously goes through crystal structure.
and crystal structures don’t inhibit current flow.
Sorry, my eyes glazed over just for a second. I’m just wiping them back. So this is probably well above my level of expertise as far as, which is meant to be of course, and that’s why we’ve got you here Matthew, because you know all this and I know nothing. I guess I just, as someone, I mean, I enjoy the improvement that good cables make in,
all areas of a system, but sometimes the minutia of the subject is, what’s the word? Overwhelming. Yeah, overwhelming. And at the same time, are there other aspects of the system that we could concentrate on that would improve the sound quality somewhat more dramatically? And I think this crystal juncture thing is something that, I don’t know, there was something
I wanted to, something you just said prompted directional cables. I want to jump sideways. I cannot remember, but I think they did. Your TARA Labs cables, the ones that I might have sold in the, I guess the early to mid 90s or something, sometime in the 90s, were they directional? And if they were, please explain why. And if they weren’t, explain.
equally why they weren’t or because the directional thing is kind of, that now that’s I guess to do with crystal structure of the copper, is that the thought? No, not really. No, that’s a different phenomenon. But let’s talk about cable directionality. It’s a big boondoggle. It’s a big one. The bottom line is it’s bullshit. Just once again to cut to the chase.
Use flash, directional cables are bullshit. Yeah, but there’s an exception to the rule. So I want to start with the conductor. If you play the conductor, we’re going to set up a simple speaker cable, 18 gauge, about one meter in length. We’re going to have a positive run and a negative run spaced apart about five or six millimetres. And so we do that with
sticky tape and match sticks maybe. it’s naked. It’s a naked wire. So here’s the thing. That doesn’t have any directionality at all. Back and forth, back and forth. I’ve heard it. The conductors themselves don’t have directionality. So when you hear about, the conductor directionality has to do with the way it’s drawn in the drawing process.
into the finished conductor. So you have to be careful which way you turn the conductor or have them have them set up. So this is this is bogus. Okay. And I have gone to the trouble of making up wires and conductors to test whether there is any directional nature in wires. point. that’s where it is. Quick point. So if you were to just with the naked conductors and just play music
same direction all day for a week and then then change the direction the actual conductor naked. So it won’t sound any different? It doesn’t. Okay. So what happens when does directionality actually apply in any form? When we build up the cable putting primary insulation or dielectric on the conductors
And then we build up the cable with more layers of dielectric or plastic materials. get the electrostatic charges within the layers of the plastic materials. And additionally, the electromagnetic wave, the signal current, the audio signal, has to find its way through these insulators. And the more insulation
cable build up that you have the thick of the cable the worse it gets and that is directional.
So, yeah, so the wire itself, the copper is not directional because yeah, I think you’re right, Matthew. I’ve read where the way it’s pulled or pushed through the die is the reason and the crystal structure is the reason why this cable is directional. That in your opinion, and you would consider it to be a fact, and I like that, I like facts, is BS. But once you create a finished cable,
the dielectric starts to play a role, but can you just throw some light, you’ve said because the signal is coming out through the dielectric in some, to some degree, some leakage or what have you. You know, I guess it’s, you know, on a humid day, it’s drawn to earth or something, I don’t know. But the point is that, to some small degree that happens, but why does it become directional? Is it the way the particular inductors are insulated differently or is it the…
I’m struggling to understand how it would still be directional, assuming, well, you explain your thoughts, please, because I think that’s very interesting. Something to do with the valence bonds in the polymer causes the dielectric material to have different elixir static charges in the dielectric material.
And you’ve got different what is termed today as dielectric permittivity, which used to be called dielectric constant. And sometimes still dielectric constant is used and understood by those in the know to be the same as dielectric permittivity. So what happens here, I like to think of it as absorption. In some cases, a dielectric material may be more prone because of the quality. And we move up the ladder from PVC
to polyethylene, to polypropylene, to Teflon or polytetrafluoroethylene to be precise. And these materials have different rates of absorption and release of energy. It’s a capacitive phenomenon. And it’s not unlike a capacitor. So that if you have
core quality dielectric between the plates in the capacitors, then the
Capacitor that is the, yeah, the capacitor has less strength between the plates. And so it’s not a good quality capacitor. It sounds bad as you guys have experienced, I’m sure. There’s also the case that when you put in a new capacitor, more especially in an AC coupled preamplifier or line stage preamplifier, the capacitors…
take minutes to hours depending on the charge, the voltage and current being applied, the capacitors will change their sound from minutes to hours. And you may have experienced that in loud speaker design. So the same is true for cables. That is the reason for cable burn-in. Yeah. Okay, so here we go. Okay, so cable burn-in.
who’s got more to do with the insulation and the dielectric than it does the wire? Definitely. Okay. All right. Interesting. We’re learning stuff here today, Brad. I don’t know about you. I Definitely. guess. yeah. Bloody hell, Matthew. You’re the guru. So, okay. So that’s, that’s, that’s interesting. Okay. So cause cable, I’ve got a few, I’ve got a few notes sitting here. Cable burn in actually wasn’t one of them, but it is one that I had in my head that I think.
Brad, you mentioned you wanted to bring it up, but we’re here, so why don’t we talk about it. So cable burn-in, so you have, I think you actually have a CD or a file you can download or something, Matthew, that you play, or tell us about that. What’s the story? That’s the Cascade Noise Burn-In Disc. Okay. And I haven’t thought about it for years, so I might.
get a couple of facts out of order here or or not say the right thing. I’m going to take it slowly. Sure. Cascade noise is a compilation of square waves, sine waves and percussive sounds. Overlaid over the square waves and sine waves on the disk. this is in the last 72 minutes long.
This is the best way to burn in or break in audio components, loudspeakers, and especially cables. I sell it and people find it remarkable. I’ve got some people saying crazy things which I don’t believe and that is that they play it before they sit down and listen to any serious music listening session. To break the reason? I wonder.
They say that they will let it play for an hour before they come into the room. the system is fully exercised or broken in. However, I think it takes hours or days to break in a system, maybe weeks. And I find that systems just over a period of time get better, get better sounding all the time. Yeah. You know, I, I
Brad will have strong thoughts on this. I absolutely agree. I have had circumstances where I have just been gobsmacked and wondered what is going on. And I’ve just remembered one circumstance where I had a pair of loudspeakers that were kind of run in, quite an exotic pair, nothing crazy, but $10,000 or $15,000 worth. And they sounded great. The customer loved the sound. They bought the loudspeakers.
I packed them up, I lay them on their back inside their box. I packed them up, I put them in the back of the van, I drove to the job, which was a good way away, I think about two, two and a half hours away. I got them out at their end, I plugged them in, and you know what I’m gonna say, they just sounded awful in every way. Now, there’s lots of things at play here. There’s one that I’ve been sitting in a van for two and a half hours and maybe…
Maybe that hasn’t actually done my hearing any good. It would be the first thought, but I think you can hear past a lot of that. mean, you sort of, you your ear brain compromise interface, you know, adjusts automatically for a lot of stuff. and I’ve got lots of thoughts on this. I, to do with high-fi shows and things and how sound. There is from room to room and why and blah, blah, blah, blah. Any other, point is, but the guy.
the customer loved the sound and goes, they sound amazing. Sound just like they did at your shop. And I’m like, geez, not to me, they don’t. So maybe that points to the fact that I ruined my hearing, two and a half hours in a van, which then brings us back to the running disc. And of course I thought initially you were suggesting the client who bought your CD was listening to the running disc, but they actually just had it playing on the system. do have a funny story to tell you, but I’ll wait. Okay. Well, I think I’d finish mine. The point is that
There are mysteries in why the sound changes. And the other thing you say about it, your system keeps getting better. And I think everyone who’s ever done a hi-fi show exhibited at a hi-fi show feels that their system is sounding at the best on the third day. But is it, know, have you just gotten used to it or has indeed everything warmed up, loosened up, settled, got used to the local atmospheric pressure and humidity?
I don’t know. So many factors. Plus the stress. stress, yeah, you’re obviously more relaxed on the Sunday. The Thursday set up is fraught with anxiety that the room’s not right, everything’s not right. there’s this sort of stress sweat that sort of, well, actually the interesting thing about stress sweat, Andrew and Matthew, and you guys probably, I don’t know whether you used it, I used to use a Odie cologne back in the day called Desperation.
and it didn’t work then and I smell it every time I do a first day show set up and I smell that audio cologne coming to the fore and it’s just fear. Well I think that that’s, I have seen you going through that and I think that that is mostly created in your mind. But, in all seriousness, the point you make is that
the first day you obviously get, you’ve got to get assist, we are going off at a tangent, but the first day you’re coming to terms with the room, the sound of the room, you’re used to your own listening room, et cetera, or the high-fi shops, you might go and listen that. And you lose, then having to adapt to the sound of that room, your brain’s sort of getting used to it. And then you go through the process of getting the system set up and the position of the loudspeakers where you think it works best. And then you get to that point where it’s,
Matthew, you’ve done it quite a few shows, where it starts to sound okay. And to your point, Andrew, that by the sort of Saturday afternoon, you’re starting to sort of, you know, reduce the caffeine intake and you’re starting to sort of enjoy chamomile and start the system settles and people seem to like, generally like what’s going on. Don’t forget every other poor exhibitors going through the same thing as well. By Sunday afternoon, you wish you could just go into Monday.
Yeah, either crazy. know. So, well, there’s, go ahead. I was going to ask you guys, because you do so many shows, what is it like on on the end of the show at the end of the show on the pack up day? The system sounds great, right? And you got a tear it apart. I’ve got one. Yeah, I’ve got one one brief look or thought on that and or fact. And that is that
the last show we were in different room in that hotel than previous and we didn’t feel acoustically it was as nice even though we had the same acoustic treatments and same, well not the same loudspeakers, a newer model, we just weren’t, no one there thought that the loudspeakers sounded as good as they had in different rooms. So we went to some trouble to…
trick up the room acoustics with a bit of extra absorption, a couple of corners and things like that. And kind of forgot about, we felt that that had improved it at the time, but we, yeah, it was partly acoustic, maybe partly psychoacoustic. But then when we started pulling the room apart on the Sunday afternoon, we started pulling some of these acoustic treatments down first while the system was still playing. And wow, there was, we weren’t even thinking about the sound. We were well past.
playing music at that point. was a few stragglers coming in and that’s why the system was going and my God, was hugely obvious to everyone that the sound was becoming much more reverberant, ragged sounding and less enjoyable as we pulled our bodgy extra acoustic treatments that we’d used hotel furniture to achieve out of the corners and what have you. And so there is absolutely something in it.
Of course, mean everyone would agree that there’s something in the acoustic treatment side of it, it was much bigger than you would think. yeah, look, getting fully wound back to the to interrupt Andrew, the point being that going back to Andrew, going back to Matthew regarding a system settling in. Yes. Is it Buncombe that
Cable settle in this big it’s left alone settle over two or three days in your opinion matter Was that a hard one to answer with everything sort of settle now? I think one a couple of points I would make about setting up a system and using cables Try to use cables that have the least amount of construction in them The conductor or the conductors are the most important fact in the design of a cable
The next most important thing is the geometry or the spacing of the conductors. That’s like tuning the response, the high frequency response of the conductors. Obviously you start out with what I call an optimum diameter, no bigger than one millimetre in diameter. then the conductors need to be insulated of course, and the insulation should be high quality and
thin layering of dielectric, nothing greater than a few to five tenths of a millimetre. And then the amount of plastic that is in the construction of the cable will absolutely just make the sound soggy and rolled off. And this is when you’ve got the cable burned in.
If you turn it around, this well built up cable built up with polymers, plastics, etc. Maybe you’ve got cotton ropes in there. They’re the worst. So if you turn that cable around, both left and right channels, you turn them around, the cables are unlistenable.
The fact is that burning makes a difference, but is less of a problem when you’ve got good quality, well-built, well-designed cables. Okay. All right. And all of the things that we’ve been talking about, the Nines competition, Ono continuous casting, crystal structure, all of these things matter when you’ve got the conductors left, not left and right.
positive and negative when you’ve got them set up with a decent spacing between them so you lower the capacitance. If again, we touched on this in the last podcast, if you were to make a twisted pair, an interconnect with a twisted pair of one millimetre conductors nicely insulated, and then you compared them to a pair of conductors that were spaced apart five millimetres,
you would be able to hear the six nines and the ONO continuous casting and the lack of crystal structure in the conductors. But when you’ve got a twisted pair with high capacitance, you roll off all of the benefits that you work so hard to create. Yeah, okay. Yeah, that kind of makes Okay, so can I just make a point? So I just want to go back to your points there.
The Nines competition, feel there’s, subjectively you found that, well has to be subjectively, that there’s an improvement with 4N to 6N? Yes. There’s merit in all of these technologies, but the way cables are made, they ruin the improvements that are brought by these technologies. Right.
So, configuration is important, the way you lay the cable. It’s very important. So, if you see a cable and you notice there’s got a plastic jacket on it, a polymer jacket on it, and the buildup around the conductors, because you’ve got a cross section of the cable, the diagram, or you’ve got a piece of it, if you see a lot of plastic, it’s going to sound like shit. Okay, interesting. And the OCC, that, again, OCC and the…
and the crystal structure, there’s definitely, you’ve heard differences there. I have, but what I said earlier still holds. There’s doubt in my mind as to how it’s done and whether the final result can really be valid. Okay. All right. So… I mean, there’s another one, ceramic dyes. I don’t know if you’ve heard of this, but Kyocera.
in japan makes cut ceramic dies yeah so you’ve got small holes in the center of the dark the wire is drawn through the idea is that instead of using a metal by you use a ceramic die so that fine metal particles don’t get dragged into the surface of the copper conductor but copper is off and metal dies don’t wear out
Yep. what you’re saying is that the copper’s molten when it goes through this? No, it’s not molten. It’s cold dry. So it gets pulled progressively through smaller and smaller dies. And if the metal dies, of course, they’re not getting worn out and having to be replaced every one kilometer of wire is drawn. No, they last for some
considerable time you’re implying Matthew. Of course they do. Yes. Yeah. Okay. So I’ve got, I’m going to, we’re to have a quick break. I want to come back and ask about, cable lifters, litz wire, cryo treatment. Good. And there’s something else and I can’t think you just touched on it. think is it, not sexual and neat.
No, it’s a kneeling. It’s not a kneeling. Sexual kneeling. Brad did it again. Funny Brad. Yeah, it’s a kneeling. Attempting humour. Yeah, we’ll be back in a second. Thank you guys. Talk soon. Thank you everybody for listening to the podcast. It’s really appreciated and even more appreciated is comments, likes, five star reviews, that kind of thing. It’s also very much appreciated. So if you’re enjoying the podcast, please subscribe, follow, like and comment.
Alright folks, we’re back, not an audio file. Segment two of today’s podcast with Matthew Bond, the cable guru, as we’re now calling him, and Brad Serhan, of course, the loud speaker design guru. So, know, room full of gurus. I want to say room, three rooms, we’re all in different parts of the world. So Matthew, you’re okay, you didn’t need a break just now? No, I’m fine. I’ve got my diapers on again.
I’m sure that’s incredibly inappropriate. So smart. So smart. I’m ready for a space mission. He’s a planner. I didn’t have a break, so I’m having a drink now. yeah, so I mentioned, look, I’ve got to ask, I’m going to skip ahead and I just need to know about cable lifters. I have strong feelings on them. I think they are the silliest, stupidest, most ridiculous.
piece of hi-fi bullshit there is. I know why people do it because the cables look kind of prettier sitting up in the air like some kind of monorail of electricity but I guess all monorails have electricity in them but you know I just I just find it hilarious and then they’ve got to be made out of particular materials because the other ones are no good you know. So Matthew feel free to educate me and and turn my
thoughts on these contraptions to a positive one? All right. You know, we touched upon already the plastic buildup, the polymers in the cable and the jackets versus a simple construction where you can judge that the cable is not complex and isn’t round in a jacket with a
twisted pair of conductors, insulated conductors running in the middle of cable. These kinds of cables have electrostatic charges in them. that is something that can be picked up by nylon carpet on the floor. And the cable lifters work, in my opinion, not on wooden floors, but they would work, it seems to me, on…
where you’ve got carpet on the floors. But I’ll be honest with you Andrew, I haven’t sat down and listened to cable lifters. Okay, yeah, but so you think that the electrostatic aspect of it with carpet might be a thing, but I, which makes sense based on your previous thoughts on the whole electrostatic nature of different insulation materials, etc. But what…
So I hear though that most people are using cable lifters because it’s something to do with vibration in the floor or something, which also there’s a sort of a, there’s a slight ring of, you know, at least a story there, which is that I guess the loud speakers are feeding a certain amount of vibration into the floor. And if the floor is, I guess, flimsily constructed or something or resonating at some frequency, which of course it would be.
that that’s what the lifters are about. They’re there to isolate the cable from that. you got any thoughts on that or is your interest in lifters at a fairly low ebb? No, I want to talk about what you’ve been talking about. We would have to assume that the cables are so poorly made that they are microphonic. Yeah, well that would mean that they were poorly made if they were microphonic. I guess it would be, wouldn’t it? Yeah. Yeah. Okay. Just to, can I throw
lob my two bobsworth in. Yes you can of course. the sort of in the past I used to take that same similar stance to you Andrew but dare I drop a my a bomb. No not a bomb Les Davis is a bomb but my dear mate Les Davis from Les Davis audio he has some devices that
which could be used underneath cables. And we’ve done quite a few listening tests with those underneath certain cables, not Matthew Bond cables. And yes, on carpet. And it seemed to improve the sound in a sort of a, seemed to sort of make things cleaner. Now this is us doing.
know, listening test, blind test or whatever, swapping down at Sturman’s Audio. interesting stuff. So to Matthew’s point about the nylon carpets, et cetera, how they might interact with cables, because with nylons rubbing up against some sort of plastic, I assume there’d be something, some interaction, or maybe not. Let’s just throw that in there.
Yeah, and there might be something else going on. You know, when you have two dissimilar materials in the construction of a cable, you can get what’s called triboelectric noise. And, and, and this is a noise generated by, as I mentioned, two dissimilar materials rubbing together, creating an electrical charge. Right. But again, that’s a poorly made cable. Yeah. Right.
So it could vary depending on the quality of the construction of the cable design. Okay. Anyway, I was just throwing that in there because I didn’t, I have heard- interesting, Brad. Yeah, have heard- differences and it was, was, there’s a difference and we thought there was an improvement. That was without Liz in the room as well. So, you know, well, we have to take into account that you’ve got someone there that you know. Yeah. And you know well. Yes. And you, you-
You’ve got to take into account how our brains work and influence. So, you, you absolutely do. And with all of these subjective, even if they’re blind and if they’re genuinely blind and a genuine blind test and you can, you can pick it, then, then it’s absolutely. And if you consider it’s an improvement, then it’s absolutely a real thing. well, it’s real this week. mean, I’ve had Alan March here. Well, he would say that I’m channelling Alan.
Yeah, because Alan is a brilliant engineer. so well, takes a very scientific approach. and which is probably the correct one, but as I always say, I counter my own thoughts by saying, I don’t really care because if you, if the, if the listener, if the owner of the system is trying something and it works for them and they’re enjoying it, go your hardest. mean, I, I don’t, I don’t care. My thoughts are simply my own and are to do more.
perhaps with my priorities in life than whether I… Yes, and that makes sense, Absolutely. I’ve just got other things I might want to do. I go for a walk on the beach instead of playing with cable lifters is to me somewhat And make it look like a really good train set. Let’s not get into it. Woohoo! All aboard! So no one on this podcast owns a train set, I take it.
No, Hornby. yes. Well, in the day. really? No, seven or eight. that’s all right. Acceptable. Okay. So, on a recent podcast and not an, I wouldn’t call them an opposition podcast. I would call it one of the leading, high fire related podcasts on the planet. There was a guest on the extolling the virtues of a cable Matthew that could both,
increased the transient performance of the system. He suggested this was due to less impedance, perhaps. And he also implied that differing cables have a different time signature or a different impulse response. Have you got any thoughts on cables?
and whether some cables are literally faster or slower than others. The velocity of propagation of the audio signal. It doesn’t vary much at all in all audio cables. Additionally, as to cables having different impedances, I would say that’s true, but it’s a microscopic or very small number. Sure.
The thing that again the things that make the biggest difference or the the real differences that that can be proven easily in a be Listening situations is the size of the conductor. It’s the predominant factor in in cable design When you when if you were to have I think I already mentioned this if you had
Six nines if you had OCC, you used ceramic dies and you had long crystals. Continuous crystals, Yeah, but you made the conductor 1.5 millimetres in diameter. You’ve lost all of the things that you tried to create. Yeah, yeah. So if a cable has a particular impedance or a particular velocity of propagation,
It’s certainly not going to improve the sound of the system. That’s an outrageous claim. Yeah. Yeah. So because you want it to be, well, you want the cable to be, you have no signature really and have… Well, you want it to have, I mean, if possible, well, let’s talk about impedance for a moment. Inductive reactance, capacitive reactance, which are we talking about? In a speaker cable, we would be talking about inductive reactance. Yeah.
inductance. Getting that figure as low as possible is the key. So, and then the speaker cables that I make now, inductance is extremely low. And the sound of my cables, I would not go as far as saying improves the whole system, it improves, they improve the sound. Yeah, yeah.
you know, making a preamplifier function better or a power amplifier suddenly has more power? That would be outrageous. So this was a headphone cable. It’s going to sell for 1250 euro for a 1.5 meter cable to put on your headphones. It’s a litz cable with maybe 200 conductors per conductor, per strand, per…
polarity. So there’s two lots of 200 I think or thereabouts. You got any thoughts on litz cable? I guess in this case if it’s headphones it’s a high impedance, you know, low current situation. It’s not a speaker cable so I guess different characteristics. different. litz wire is not good.
The premise of litz wire is that each strand is insulated and it’s not a simple bundled conductor of raw uninsulated strands. if you’ve got a litz wire conductor and it’s greater in diameter than one millimetre, it rolls up high frequencies. Once you individually insulate the conductors and bunch them together again, there’s no audible or measurable
improvement in the roll-off of high frequencies, it actually becomes worse. A three millimetre diameter litz wire sounds bad. A two millimetre diameter litz wire sounds bad. When you get down to one millimetre and it’s litz, it will sound good, but not better necessarily than a solid core conductor at one millimetre.
So it’s a really, it’s a lot of extra effort from your implying no benefit. No benefit at all. Yeah. Okay. I guess other than greater flexibility of the wire itself. Yes. the, what was the other thing I was going to say? cry cry cry. Yeah. so, you know, the story here, the claim is, is that they
take the cable or the conductor, whatever it is, and they take it down to somewhere near zero degrees Kelvin, which as I’ve been corrected is minus 273.15 Celsius. Thought I’d throw that in there, the one five for you Andrew. I directed me in the last podcast. The one five is, well, let’s face it, if you don’t make it, if you just
Was it 273.15? Yes, 273.15 I think I read. I’m guessing because it’s a negative number. If you only get to 273, you haven’t gone far enough. I by comparison. Yes, worn by comparison. What did you say Andrew? Matthew? I said 273 is worn by comparison. And 270 is sweltering.
Well, you’ll you’ll take any degree you can get if you’re you know, if you’re in that environment So you tell us about cryo, what’s it meant to do? I thought it was something to do with crystal structure or something again, but I probably didn’t take it Andrew. Yeah, we’re gonna take the we’re gonna take the material down to 260 270 degrees and Then they say that it will be stepped up in intervals
going up to say minus 200 and then minus 150 and then minus 100, minus 50, ultimately to room temperature again. This sounds like diving. It is like that. Yeah. The thing is, there are many cable companies that claim they’re doing cryogenics and that they have a proprietary stepping up
of the temperatures that they have found makes the product sound better. there’s that claim, which again is just bogus. And I’ve got a funny story to tell. Far away. I was bugged every week with a phone call from somebody who had a cryogenic chamber and wanted me to send a pair of interconnects.
So I got two pairs of interconnects made, put them in the sound room, sent one pair off to be cryogenically treated, got it back about a month later. Well, it took a while for them to warm up again. That’s the Benz treatment. They do the Benz technique. Well, I specified one degree per hour. Just to mess with them. I’m just kidding.
But anyway, I got them back and it took a long time to get them back and I had them in my sound room. So I then picked up the first pair and the second pair, which had been cryogenically treated, listened to them, A, B them. did AA as we talked about in the last podcast, something I do to prove to myself that the second time around I hear differences and not audible and not acoustic differences.
that I noticed different things from one 30 second listening to the next 30 second listening test. Yeah. So anyway, the bottom line is I got the two pairs confused. Yeah. Okay. you actually got them confused, confused. Like you didn’t get them audibly confused. I couldn’t remember which pair was which. The ultimate blind test. No, no labelling. So how did that work out?
They sounded the same. Yeah. Okay. That’s, you know, that’s kind of cryogenic treatments. Yeah. That’s, guess it’s one of those things that it sounds kind of interesting and cool and a bit special. mean, you know, you could have cryogenically treated all sorts of things, I guess, but yeah, it sounds great. So you, it, so you,
I mean you’ve done the Admittedly the one degree per hour raising of temperature, which I know you say was a gag, but that would have been… I mean if you’ve got this guy hassling you with his cryogenic facility, you go, yeah I’ll get it done, but only on the condition that you raise the temperature one degree an hour.
What was even better is the fact they offered the Disneyland alternative as well. yeah. The Disney one. You could stow them away and bring them back to life years later. Boom boom. Any other thoughts on cable myths? I guess we’re calling them myths because you’ve kind of, well, you’ve laid a lot of light on the ones that kind of work and how they could work. Then there’s the cryogenics in your experience has not been effective.
And but what else have you got Matthew? Have you got any other little gems of information? Let me think for a moment. Can I log in a kneeling? yeah, we should log in a kneeling, something that I know works. OK, well, tell us about that then. So there’s something called resistance and kneeling, which is to say you take a length of copper wire section by section, it goes into an ammonia chamber.
the conductor is heated up and it softens and becomes more conductive by eliminating crystal junctions I suppose. I don’t know why it becomes audibly superior to be honest but it’s softer you can bend it more easily it takes more bending than a normal one millimetre conductor can and
Yeah, I find it works. A kneeling is something special. Okay, so tell me, I’m a bit confused. just set me straight. If you get a length of copper pipe that’s not annealed, it is very stiff and very fragile. You can’t bend it. It will, it will tear if you like. You then if you’ve got to bend a pipe and I’m no plumber, but you know, maybe I’ve
Maybe I’ve built a piece of equipment once that needed pipe bent. so you get annealed copper and you can bend it around a large piece of PVC pipe or something and make a very nice coil, which you might use in this said piece of equipment. the, so, but therefore what
kind of copper wire is not annealed. felt like copper wire because it’s flexible mostly, although not house wiring. I mean, obviously that’s quite stiff, but your one millimetre preferred conductors are annealed or not annealed? They are annealed, yes. well, okay. Well, that kind of explains that. And they’re coated in a material made in Japan, that originated in Japan called polyester mica, which is…
which is 0.08 of a millimetre thick. So we’re talking about an extremely fine film. They make mica powder, mix it with polyester and extrude that over the copper conductor. So it’s an inaudible dielectric material, the first one I’ve heard or haven’t heard. Okay. right. is this, okay, just…
I’ll insert an ad here for you then Matthew. this some of these ideas are something you’re using on your new Ranger cables or what? Yes. okay. Yeah, yeah. So answer yes using them on my and the middle of the right from the bottom of the range through to the middle of the range and and above polyester mica is my preferred installation material. Okay. Okay. You heard it here first. And you possibly did hear it here first.
because this is all new stuff, isn’t it? Yes. Okay. Brad, have you got anything else to add that you or anything? You’re far away. Thanks. Thanks, Andrew. The floor is yours. Thank you, sir. And it’s interesting how annealing and getting the sort of mono crystal with OCC. It’s interesting that also cryogenic, which goes the opposite way. yeah.
So Matthew, I’m sort of thinking, well, okay, what’s the so-called advantage of cryogenic treatment when it supposed to give you a mono crystal or? Yes, Brad, the claim is that you get mono crystals and that it’s like, they liken it to annealing, but I know annealing works and my opinion is that cryogenics doesn’t work. But heating the actual conductor helps.
and make potentially helping with eliminating crystal junctions. Yes, it heals the conductor making as I said it more conductive and this is measurable this is not something that and it’s only a few percent in terms of conductivity but it makes the difference between tough pitch or four nines copper to have six nines copper soft annealed. okay right right.
And I guess these extra processes are what adds a significant cost to an audio cable. Is that right, Matthew? Yeah, that’s right. I don’t know the price at Bunnings for a one millimetre conductor. I haven’t, I’ve never been into a Bunnings. I was just told some time ago that that was the equivalent of Home Depot here. Yes, it is. Yes.
And so one day I might get a job. Well, I’m going to retire back into us back in Australia. I’m going to go work in. I’m going to work in Bunnings in the wire department. Wow. Actually, Andrew and Matt, there is a in Sydney, there’s the Turks Electrical Center. A lot of Turks around the place. And you might be better at Turks where they’ve got like a whole lot of that electrical cable. OK. And.
I appreciate any suggestions you have Brad. That’s great. My question is, I’m not sure my resume is going to help me. Just put yourself down as a young Turk. love that. My question is why would you, why would you move back to Australia? Other than obviously the wonderful weather and the, the beaches and the. I’ve got a little spot.
picked up in on the Sunshine Coast. no. He’s very close to you Andrew. yeah. Okay. The Sunshine Coast, eh? I’m very familiar with that wonderful part of the world as I lived there for many years. What part of the Sunshine Coast, Matthew, have you got selected? Moffat Beach near Caloundra. Well, okay. I mean, it is a wonderful part of the world.
The only catch with the place is there’s a whole bunch of other people that also think it’s wonderful and choose to live there. So it’s lost a little bit of its charm perhaps over the years as it’s become more and more busy. When was the last, we’re obviously changing subject, but when was the last time you were there, Matthew? About two years ago. okay. All right. Well, I don’t think it’s changed much in the last two years. So yeah, so it’s interesting. Okay. So
Yeah, what can I say? I mean, it is a beautiful part of the world and the whole strip really is, I mean, the whole strip, Southeast Queensland, probably from Byron Bay up to Teewanton is an amazing part of the world. then you live in an amazing part of the world at the moment. So, but I guess you get bored with everything, right? So you, I mean, you have a hell of a winter there, I would guess, would you, or is it just foggy and humid, but cool? It’s mild. The temperatures.
Temperatures get cold down to 32 Fahrenheit, zero degrees Celsius. And we get some snow. Okay, yeah, right. So, less of the fog and more of the snow. Yeah, well, there’s certainly no fog or snow at Moffat Beach, but there are tourists. I feel like there was some other cable business that we had to discuss, but maybe it’s done, and in which case we can go on to general business.
I have no idea what general business is, but if anyone’s got anything to discuss, I’m happy to. I that you might call that sundries. Sundries, indeed. So I had a sundry, but I didn’t write it down and now I’ve forgotten what the hell it was. Well, okay, well, while you’re thinking that, Andrew, I might just throw something at, well, not a question, but a summary, I suppose, of what we’ve been discussing.
Essentially, Matthew, a lot of this stuff that not all you feel make a difference, but it comes down to the way you design the layout, the internal structure, if you like, the wire and the installation, etc. A whole lot of stuff goes into the composition of a cable to the end user. This is poorly worded, but it’ll do. The bottom line is that less is more.
Okay. yet… That’s probably true for loudspeaker design. I’m no loudspeaker designer, but I am sure that if I was building a loudspeaker, I would try to build it simply and maybe some things are complex like crossover design, filter networks, the choice of filters. I’m sure there’s a lot to it. I have no idea.
Well, I think it’s a little bit like cables and that the tiniest of the timber you use, the how you treat it, the glues you use, the area of the material. If we’re just talking about cabinets, there’s so many little things that will affect the resonant nature of the cabinet and how it will react when vibrated upon, etc. Blah, blah, blah. It’s a, I don’t know.
It’s a bit of a mess with your head. You know when you got it right though because as you do with cables, Matthew, it’s magic happens. Well, I think we’ve seen to have wrapped that up and I have a feeling, Matthew, we’d like to get you back at some point to discuss general audio stuff because you’ve got a very interesting take on things and I like your honesty and I think the audience probably does as well.
And I think also, as we mentioned in the previous episode you were on, you do have some new cables coming out that are fairly affordable. And I guess we might have you back to discuss those and drop a bit of an ad into the conversation so that people know they exist and may want to give them a try at some point. on that note, yeah, no. So feel free to sum up Matthew and Brad and we’ll call that a take.
Well, I appreciate your time, Andrew, once again. I really enjoyed talking with you both. it’s been very illuminating. just find the, guess it’s something that cables, you sort of listen to different ones or whatever, and you sort of gloss over what’s actually in them, and you’ve drawn, you’re thrown a light on what the construction actually is and perhaps the ideal. Well, your experimentation has shown what the ideal way is to do it.
and that you’ve shown off in your new models. But, you know, there’s clearly a lot more to it than one would initially expect. And I found that very interesting. Brad probably knew it all already, but… no, I didn’t. You didn’t? No, don’t. I sort of had hints. Yeah, okay. A little bit, but that’s only through Matthew chatting to me about it. no, know bugger all. Like you, Andrew, I’m…
I’m sort of as fascinated as we went. You probably got busy. You’re busy with other things. Now, this podcast, not an audio file, needs some love always from everyone who’s listening. So if you’ve enjoyed today’s illuminating episode, feel free or would you please maybe give us a five star review or write a short essay or, you know, like and subscribe depending what platform you’re listening to.
Yeah, well, it depends what platform you’re on. mean, we’re on three or four different ways you can listen and they need a different little different subscription or follow function. But the idea is to follow the podcast and that way when there’s a new episode, you’ll be. What are we on? You’ll be informed. We’re on iTunes or Apple podcasts it’s called these days. Spotify, YouTube are the three key ones, but also Amazon, Audible and a bunch of other.
podcast aggregating websites have us listed. So we’re everywhere basically. That’s wonderful, Andrew. Yeah, that is good. It’s and yeah, so far it’s a new podcast, course, but many people following and enjoying and giving us positive feedback. that’s very much appreciated and we’re happy to hear more. Comments, by the way, folks, are best made on YouTube where you can just get on there and say whatever you want. And we’d be, you know.
positive or negative, we’d be keen to know what you think. thank you Matthew Bond from Tara Labs and Matthew Bond Audio, ex of Tara Labs of course, and now of Matthew Bond Audio and Brad Suhanna, Suhanna Swift. Thank you for your input today and questions. And we’ll talk to you all again, guys. Okay, Andrew, bye bye. Bye Matthew. Bye Andrew, marvellous stuff mate, thank you. Thank you Brad.