Not An Audiophile – The Podcast featuring Morris Swift from Serhan Swift. “I get more excited at the idea of putting together a system for under ten grand that blows people’s socks off than I will ever get excited about a megabuck system.”
Podcast transcripts below – Episode 006
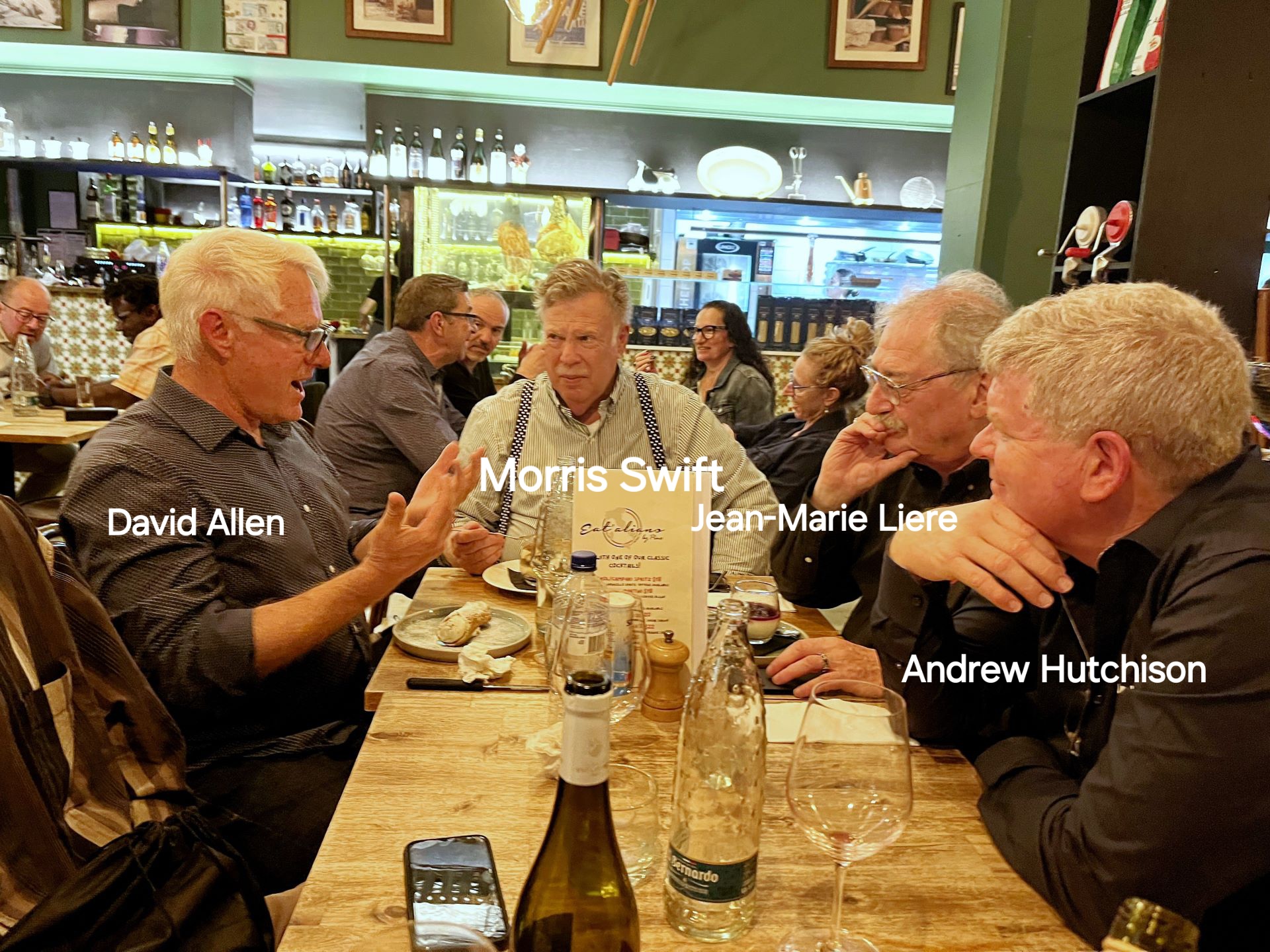
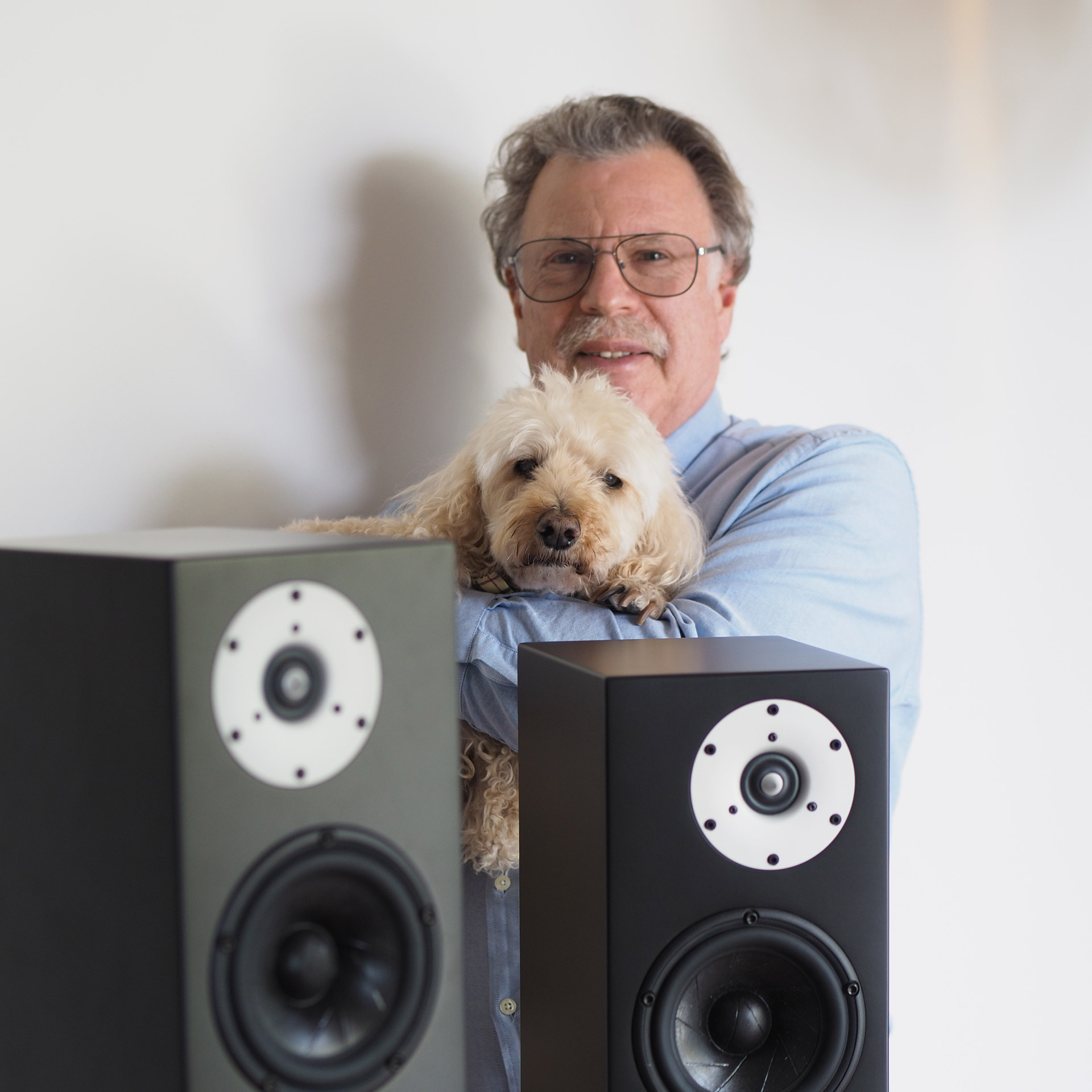
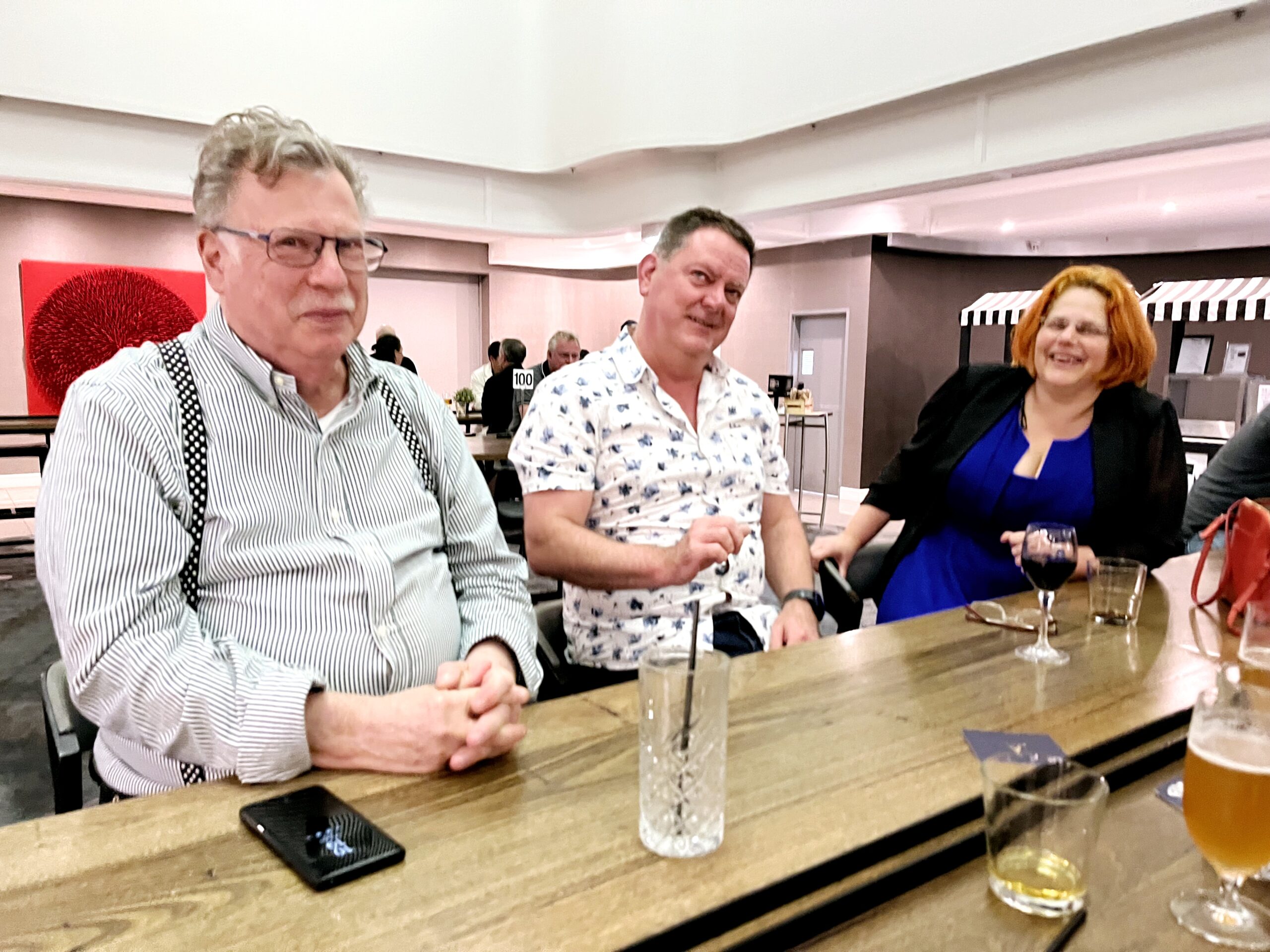
TRANSCRIPT
Morris Swift from Serhan Swift & electronics past & present
Morris Swift is a lifelong electronics engineer and has interesting stories to tell
Morris Swift: And you know, squiggly lines and wires and meters and all that sort of stuff. So my parents were devastated because I was going to be a doctor or a lawyer, but, not anymore.
Andrew Hutchison: And hello, welcome to Not An Audiophile. The podcast today is episode six of season one and our guest is the wonderful Morris Swift, of course, partner, of, Serhan Swift, loudspeaker manufacturing, but also a lifelong electronics engineer and he’s got some interesting stories to tell. Morris, are you there?
Morris Swift: I think so, yeah.
Andrew Hutchison: Okay, you are. and all parts.
Morris Swift: I don’t know if I’m all there, but, I’m there.
Andrew Hutchison: Well, the audio’s pretty good, so we got that. Right. And So look, appreciate your time. it’s great to speak to you. You have, a wealth of knowledge about all things audio and audio engineering or electronically engineering related. And I never know whether to say electrical engineer or electronics engineer. Is there a difference?
Morris Swift: I think the title is still electrical engineer as in be, but it comes down to your speciality because a, be can be a power engineer or a computer engineer or whatever. And I mean, I never studied audio at uni, even though audio was a passion from when I was, you know, like six.
Andrew Hutchison: Yeah, okay.
Morris Swift: But somehow professional, professionally and at uni? no, I never really did audio. I did a undergrad thesis on developing a music synthesizer, but, not audio per se. Our uni didn’t have people like Neville Thiele and those sorts of people running courses. We were at New South. I was at new South Uni, the better uni, but, we didn’t do much, much in audio at the time. Although I was in my final year, I was working in the communications, division and we had people there who were doing research into audio audibility of phase. There was one guy doing amplifiers. but no, I was never really professionally. I kind of skirted around the edges, but it was always a passion and always a hobby. And in my spare time I did a bit of speaker and amplifier building, not professionally until, you know, sort of got to a stage where, well, it’s a passion. Why not, you know, why not do something, a little more, a.
Andrew Hutchison: Little more active trying to try to spin a hobby into a business perhaps, which is, kind of, sort of, kind of, sorta.
You say you had an interest in audio from the age of six
Hey, so you say you had an interest in audio from the age of six. How did that come about? Or what makes you say that? Did you have a, you know, you had a childhood experience?
Morris Swift: Yeah, I think I think what happened was, we moved into a new house that my father had built from scratch, and custom furniture, as was the fashion in those days, and a built in so called radiogram.
Andrew Hutchison: The radio.
Morris Swift: And. And it was stereo.
Andrew Hutchison: Okay.
Morris Swift: And I re. And I remember, you know, one of the first stereo albums which had a big warning on the front, will not cause damage to mono equipment, you know? So that gives you an idea of how far back we were.
Andrew Hutchison: Yes.
Morris Swift: but I was fascinated by all this stuff and, watching the system get built up by an engineer at the time, and he had an oscilloscope. And once I saw all these squiggly waveforms on the oscilloscope, but that was it. I’m an electrical engineer. I’m in.
Andrew Hutchison: Okay, so it wasn’t just. It didn’t just. The whole radiogram custom building exercise wasn’t just or didn’t just create an interest in music or audio reproduction. It was. It was the trigger to get into electronics. Full stop as a car.
Morris Swift: I think so, yeah.
Andrew Hutchison: It’s interesting. Hey, I mean, yeah, I can point to how I got a start in it. It’s a very similar thing. Not quite as young. we did have a horrible radiogram, but not custom made, but, So this radiogram. So we’re talking late, fifties, mid.
Morris Swift: Sixties, early sixties, 1960 or 61.
Andrew Hutchison: Yeah, okay. Yeah, so 1960 or 61. So tubes, obviously. So he, This gentleman who created this system, needed an oscilloscope at the house because. What do you think?
Morris Swift: I think. I think. I think he was repairing something. TV and, And,
00:05:00
Morris Swift: you know, squiggly lines and, wires and meters and all that sort of stuff. So my parents were devastated because I was going to be a doctor or a lawyer, but, Not anymore.
Andrew Hutchison: Yeah, you decided to choose a much more difficult profession. So that’s,
Morris Swift: Right.
I hated computers with a passion, because those were the days of mainframes
Andrew Hutchison: So I guess we could, we could fast forward to university, although we’ve kind of visited there. But you. So. So. So you were doing engineering, specializing in. Well, was there a special. I mean, you probably don’t specialize in first year, I guess, but,
Morris Swift: No, no, but towards the end you have a number of electives.
Andrew Hutchison: Yeah.
Morris Swift: Okay, so I always loved circuit design.
Andrew Hutchison: Oh, yes. Yep.
Morris Swift: not so much. I hated computers. Hated them with a passion, because those were the days of mainframes, you know, you didn’t have or maybe minis. Certainly personal computing was not a thing.
Andrew Hutchison: No.
Morris Swift: and so you did batch jobs where you had to fill in these little cards, you know, color in the squares. And they would be scanned and, you know, boring programs like, you know, all written in Fortran and, you know, to do simple accounting jobs. And. No, that was not for me. and then you’d sort of come back and you had an error because you colored in the wrong dot. And then you’d have to start all over again. It was a pain in the ass, and I didn’t see the point of it.
So, then we get to thesis time.
Andrew Hutchison: Yes.
Morris Swift: Okay, year four, you had to do a project of some sort of thesis, a major work. and, I looked at all the topics and I thought, that doesn’t interest me, but I had an idea for a polyphonic synthesizer when synthesizers in the early days of Moog or Moog were single note. And I had an idea of how you could maybe do a multi note one. And then I picked up a paper from Stanford, and they had a polyphonic synthesizer, one of the first.
Andrew Hutchison: Ah.
Morris Swift: And they had a full on synthesizer based on an integrated circuitous one per note. So literally a rack of gear and 64 note keyboard, 64 synthesizers. And I thought to myself, probably based.
Andrew Hutchison: On, there’s got to be a better way.
Morris Swift: I thought, well, last time I looked, I didn’t have 64 fingers, so do I really need 64 synthesizer? I think that was partly triggered by some work I was doing in the holidays for the overseas telecommunications Commission, where we did a lot of work on time division, multiplexing and resource sharing. And, you know, trying to get more into our, communications channel might have been partly triggered by that. But I thought if we had ten synthesizers, but we sort of allowed them to be reallocated where they were needed, we wouldn’t need all this hardware.
Andrew Hutchison: Indeed.
Morris Swift: But how to do it?
Andrew Hutchison: Yes.
Morris Swift: so I designed some hardware, and it actually, you know, after spending a lot of time on it, it actually got simpler. and I came up with a. With a system. I mean, it still had lots of chips in it, but the operating principle was quite straightforward. And so I said to the guy who was going to be my supervisor, I said, well, I don’t really like your topics. I’d like to choose my own. And he sort of. You what? You what? You want to choose your own topic? He said, well, what topic would you choose? I said, I want to build a polyphonic synthesizer.
Andrew Hutchison: Okay.
Morris Swift: And he looked at me like I was from another planet. He said, that’s a PhD. I said, no, I don’t think it is. I actually think it’s pretty simple. And he said, ah, well, you know, show me a schematic and we’ll talk about it, okay? And I showed him the schematic, and he looked at me and looked at the schematic. He said, this will work.
Andrew Hutchison: Okay, wow.
Morris Swift: He said, but he said, now bear in mind, I hate computers, right?
Andrew Hutchison: Yes.
Morris Swift: So he said, okay. He said, I tell you what, the university has just been given by Motorola some of the very first microprocessor chips in existence, okay? And these things were like $400 each when you could buy a Holden Commodore sedan for under four grand. So these were not cheap.
Andrew Hutchison: No, they weren’t.
Morris Swift: He said, I tell you what, I’ll let you do your polyphonic synthesizer based on a computer, okay? So this was like, oh, come on, you’re just screwing with me now, aren’t you? And then he saw my reaction, you know, oh God, with a computer? Are you out of your mind? He said, but to make it interesting, he said, I’ll give you an exemption from all your computer subjects. Where do I sign? Come on. But, you know, to give you an idea, Andrew, this was a computer chip. We were loading these things in binary opcodes. Assembler, yes. There was none of the things where you could sit
00:10:00
Morris Swift: down and write a program in a high level language and then have it compiled.
Andrew Hutchison: No.
Morris Swift: so this was real grassroots computing. But I suddenly realised, hey, this is kind of cool because I don’t have to pull out a soldering iron every time I want to make a change. I just have to load a different set of opcodes.
Andrew Hutchison: Indeed.
Morris Swift: And I started to sort of think this sort of computing, I like real time systems, signal processing, doing that sort of stuff. Not writing in Fortran with punch cards and God knows what else. This is kind of cool. you know, and that gave me, I, guess, ah, an affection for, you know, embedded computing and real time computing. And that continued on for many, many years. And that became something that I did a lot of consulting work in and designed a lot of products around embedded systems, but that was where it started. And, you know, so, so that was, you know, not really an audio project, but that was a direction that I went in.
Andrew Hutchison: I mean, it’s a product, I suppose.
So you, so how did the, the, the project, go? Did you end up with a successfully running machine or.
Morris Swift: Absolutely.
Andrew Hutchison: Okay.
Morris Swift: Absolutely. So, so I did. I only wish I had patented it at the time, but, hey, I was just an undergrad. What did I know?
Andrew Hutchison: well, yeah, just to clarify what time it was in the scheme of things. Now, obviously, the Fairlight is a. Is a different type of.
Morris Swift: Interestingly, interestingly, Fairlight was also working with the university. But the university was more involved with the Fairlight originator, who was Tony Furse. He came up with the idea of using computers to do signal processing. And he did the original Fairlight architecture. But then Peter, Peter’s brilliant. and Kim, who’s also a very good out of the box thinker, they came out with the idea of sampling.
Andrew Hutchison: Yes.
Morris Swift: You know, and that was my.
Andrew Hutchison: I mean, it’s a different product in that sense that it samples.
Morris Swift: Well. Well, the main thing that, I mean, what I was really working on the keyboard side of it, you know, developing a keyboard that could generate the signals. And unlike Moog, which did everything using voltages, I was doing it digitally as well.
Andrew Hutchison: Okay.
Morris Swift: So it was sort of contemporaneous. M. but I knew nothing about Fairlight at the time.
Andrew Hutchison: Yeah.
Morris Swift: Other than, the fact that Tony Furze and the department that I was working with we were collaborating on how to use computers to compress audio and how to use a simple mathematical seed to generate musical, sounds and so on. but then fairlights were running and they were sort of state of the art and developed, the CMI. But that was, I guess, invisible to me at the time. And But you know, look, it was just an undergrad thesis and something I wanted to do. but then my first job outside uni had nothing to do with any of that. it was designing integrated circuits at AWA, which is one of the few, one of the two silicon foundries in, Australia, other than Phillips. And they were doing. They were doing all sorts of application specific type ICs. you know, nothing like what we do today in terms. I mean, you could count the transistors. You know, it wasn’t like today where you got a billion and it was all done by hand. You were designing the circuits from scratch. again, most ICs these days are designed using software. You know, you design the functionality and the software then takes it and does all the, all the hard work. Now, in those days we actually, designed the circuits and even the masks were done by hand. You actually, you know, you drew them. You drew the masks.
Andrew Hutchison: Okay.
Morris Swift: And then, and then somebody, they had a thing called a ruby list cutter, which was Which was, you know, like a clear celluloid with a red layer on top. And you cut these to make the pattern.
Andrew Hutchison: Wow.
Morris Swift: A bit like how we used to do early, you know, how hobbyists used to do printed circuit boards. Yeah.
Andrew Hutchison: Sort of attack it on a tiny scale. Obviously, you’re still fitting it into a.
Morris Swift: well, you did it thousands to one, and then you reduced it photographically.
Andrew Hutchison: Yeah.
Morris Swift: The masks that, that did the silicon.
Andrew Hutchison: Yeah.
Morris Swift: Ah, but it was a totally manual process. We weren’t using computers. No, we didn’t have access to those sort of computers. they just weren’t available.
Andrew Hutchison: Cad was, because to put a year on it, which is where I was draw, we’re talking 1978 or 1980 or something.
Morris Swift: Yes, you’re talking, you’re talking the late seventies now. and then probably a decade or so later, they got more into CAD design. but again, using minis and mainframes, you know, the idea of personal computers. No, and, you know, we’ve gone right off audio.
00:15:00
Morris Swift: but it’s, it’s quite interesting because.
Andrew Hutchison: You know, we’ll come back again.
Morris Swift: We, we take that. We, we take for granted the amount of computer power in a phone.
Andrew Hutchison: Oh, and.
Morris Swift: Absolutely, yeah. And you know, it’s a bit like, you know, my first hard drive was five meg. Does m. Anybody know what a meg is anymore? We don’t talk in meg.
Andrew Hutchison: You must be older than me, because my first hard drive was 20 meg.
Morris Swift: So, my first was five meg and it cost $5,000. More than a cardinal, more than a car. Okay? So that puts it in perspective. And I remember also, for example, you would have a. We used to build, we built our own computers then. We did had a thing called the s 100 standard bus. And we had these big cards. So a memory card which would measure probably about ten inches by five inches, chock a block full of chips, pulled about five amps around stinking hot, and it gave you a grand total, 16k. Enough, enough for an emoji. Okay, just enough for an emoji for a low res. And our engineer came back from the states and he had proudly showed us this 16k card. And everybody in engineering is rolling their eyes and saying, tony, you bloody wanker, what the hell are, ah, you gonna do with 16k?
Andrew Hutchison: Ah, how would you possibly use it?
Morris Swift: You’re never going to feel that, you’re never going to fill that. Because we were writing an assembler and we could build an accounting system into 16k.
When you look at how the computer generation has evolved in our lifetime
We had, and then we graduated to 100 kilobyte floppies, 100 kilobyte floppy disks. And you would run your business on that. You could run a whole business on that. But then we got into windows and graphical user interfaces and suddenly we were chewing up kilobytes tomorrow. And, But this is where we started, you know, this is, and this was when you look at how the computer generation has evolved in the space of our lifetime, in the space of 30, 40 years, it’s mind boggling. And, you know, the stuff that we do today, I remember going to a, lecture by a guy from intel, and we had the 80286 processor, and he said, that’s it, folks. That’s it. I, that’s as far as we can go. It’s the limit of physics. We will never go further than that. That’s it. Well, I think we’re about a thousand times faster and smaller, already. And I don’t know if you might remember this, Andrew.
Andrew Hutchison: Sure.
Morris Swift: Do you remember, do you remember memory chips with built in parity because the alpha particles were knocking out the bits.
Andrew Hutchison: Now I do not remember that. Now I do not.
Morris Swift: Okay. Size of the cells got to a point. They were getting smaller and smaller and smaller. And the natural alpha particles that come from the sun or the atmosphere or wherever were actually knocking out computer bits. And we had to build extra parity in there with error correction to cope with alpha particles. Well, we’ve gone probably a thousand times smaller than that. And I look at this stuff, and I’m going, does this stuff actually work?
Andrew Hutchison: So what are you saying? If you took, you took your computer out in the sun, it would,
Morris Swift: Oh, just about anyone. It was recognised that there was an error rate, and it was partly related to stray radiation. And that’s how I remember it anyway. or maybe they had the theory wrong, but I do remember that eight bit memory cards had a 9th bit.
Andrew Hutchison: Yeah.
Morris Swift: And that was because the error rate was so high, they had to detect errors in the memory.
Andrew Hutchison: All m. Right. All right. Okay. Well, yeah.
Morris Swift: And now we have in a thumb drive. Now we’ve got gigabytes where the cell size is absolutely tiny. And it’s amazing that it works. because I remember when we were doing meantime, between failure analysis, and we got to a stage where we said, no, there’s too many components. This is going to fail every five minutes. Well, again, we’ve gone way past that. Millions of transistors, okay? There’s redundancy built in. There’s clever architectural things going on. But when I think back to that time and what we’re doing now, it’s, no, it’s not possible. It’s beyond the laws of physics. Well, guess what? we are doing it. We are doing it.
Andrew Hutchison: I guess the goalposts and the possibilities continually move and become smaller. But it’s an interesting thing that we’ve made such inroads in computing and yet people are now playing music on records, which probably the same records that you were playing or your parents were playing on that custom radiogram in the in the what was it? Early sixties, 1960s.
Morris Swift: Well, that’s a great point.
00:20:00
Morris Swift: And of course there are some people who will not listen to anything that isn’t tube.
Andrew Hutchison: Well, yeah, there is that as well. That’s right. Yeah. Yeah. Which, I mean, I guess the tubes. There are no, correct me where I’m wrong, it does happen, but are there any new tube designs or. All the tube designs basically were set in concrete in the fifties, sixties and seventies or something.
Morris Swift: I think the ones that are still coveted are still basically old, old design stuff. I don’t think there’s been any, any major inroads. I mean there was new vistas that came out, which are your little tiny tubes.
Andrew Hutchison: That’s right.
Morris Swift: That originally came. Things like car radios used them.
Andrew Hutchison: Yeah.
Morris Swift: And I think, I think if I’m not mistaken, musical fidelity was one example where they had them in a preamp or something.
Andrew Hutchison: Yeah, yeah, yeah, yeah.
Morris Swift: They were almost
Andrew Hutchison: They sort of solder into a board almost from memory.
Morris Swift: Yes, yes. Yeah. They didn’t have pins. They were, they were wired in.
Andrew Hutchison: Yeah.
Morris Swift: So. Yep.
Andrew Hutchison: Okay.
Morris Swift: So, you know, everything old is. Everything old is new again.
Andrew Hutchison: Yeah, except old computers. I mean there’s no, I mean, you wouldn’t even be able to find one. I mean that’s it’s a bit like a CRTV. If you wanted to know what one looked like and see one in the flesh, you. I’m not even sure if there’s one in a museum, but I guess there is a few floating around, but they’re really all gone underground, which is kind of a shame.
Morris Swift: Well, we are forced to upgrade because of the software and the incompatibilities. And it’s actually quite frustrating that the rate of progress in computer design, if you bought, if you used to build a computer around a particular motherboard m and a particular processor, and you’ve got all these peripheral cards built in and the thing fails to, you could never buy another motherboard. You’d have to basically throw the whole thing out and start again.
Andrew Hutchison: They have,
Morris Swift: And that was, and it used to happen, surprisingly in a surprisingly short time. You know, the life cycles were incredibly short.
Windows is rewritten to force you to buy new hardware
and that was quite frustrating. And of course then, you know, the software the software doesn’t run on those older processes. None of the drivers are compatible. So you’re kind of forced to, to move on even though there probably was enough computer power, to do a lot of things that you are forced to move.
Andrew Hutchison: I think everyone feels like windows is rewritten mostly to use up resources to force you to buy new hardware. But Hey look, I’m going to take a quick break, and we’re going to come back and speak about we’re going to skip forward in your, in your long career to audio and to I suppose briefly cover your interest in very high quality audio and you’ve been in it a while and we’ll talk a little bit about that.
Andrew from Dellichord loudspeakers speaking at Melbourne HiFi show
So back, back very shortly folks. Great Andrew here from Dellichord loudspeakers. we’re at the show, the australian HiFi show that is in Melbourne at the Pullman Hotel, Albert park from the 11th to the 13 October. In other words a few days, although that would depend when you’re listening. If you’re listening sometime early in 2026, you missed it. So. yeah, because this is 2024 and So we’re in 2204. I think I mentioned that we’re displaying with Alex from Audio Fix Distribution, who imports EAR, Yoshino tube amplifiers and exposure electronics, both from the UK. And we’re probably almost certainly releasing a new model. it’s an affordable model, we’re very pleased with its performance and we’d love you to come and have a listen to it. So. Yeah, 2204 Dellichord ear and exposure electronics. See you at the show.
Morris Swift is an electronics engineer and lover of high quality audio equipment
And we’re back at Not An Audiophile, the podcast today we’re with Morris Swift, an electronics engineer and lover of high quality audio equipment and of course designer of various equipments. But I love to say equipments and gears because people seem to use that expression these days, because it obviously drives some people mental. is various ah, equipment and of course involved most notably with the sir Han Swift, loudspeaker, manufacturing concern. And of course my question is how come your name is second?
Morris Swift: I wasn’t expecting that.
Andrew Hutchison: Well we’re going sideways from old computer talk, by the way, that that previous segment of people were skipping ahead. I mean the old computers, it just, the numbers are astounding, both the price so ridiculous and the abilities or the performance so poor compared with modernization. but and of course the other thing that we mentioned that you told the story of was your Polyphonic synthesizer project which Just happened to almost cross paths with A very Famous australian synth in the form of the fairlight. Which I think was pretty much the world’s first sampling
00:25:00
Andrew Hutchison: synthesizer. I think. Or something like that. Not my area of expertise so I could be tripping over my terminologies. But,
Morris Swift: Look, it did. It had a whole lot of world first. You know, all digital computer controlled sampling. It had composition in it. It was truly. I mean, we overused the term but it was truly a game changer. It was a whole new paradigm in music synthesis and Audio processing. You know. It was quite, quite phenomenal.
Andrew Hutchison: Now that is the definition of a game changer. Because it changed the game. I mean it’s It these. Everything’s a game changer these days. But really the game isn’t changing. But that that was a benchmark. So,
Morris Swift: Absolutely.
Brad Serhan developed new name for law firm based on military rank
Andrew Hutchison: So, all right.
Morris Swift: Why is my name second?
Andrew Hutchison: Well, I mean, did you draw straws or what happened?
Morris Swift: No. Well, I could say it’s because you remember dessert more than main course. But, No, no, I think. Look, It was interesting because we had another name. Brad. It’s hard to do this without getting into the whole history but I guess in a nutshell there was another name that Brad was working under called brigadiers.
Andrew Hutchison: Yes.
Morris Swift: Which he. Based on the british comedy about the military. And there was a rank called Brigadier. And so that was where that came from. And I hated it. But it was also a case of. Well, we were looking at. Okay, how can we, you know, develop the brand and getting brigadiers known? Developing the brand. And I said, brad, you’ve been doing this for 30 years. Everyone knows Brad Serhan. Indeed, you know, everyone. It’s just the way he is. He’s very, you know, personable.
Morris Swift: And Everybody, everybody knows Brad. And he, I think, as you said has, you know, very prolific designer. And I said, why are you doing this? Why don’t you use your own name? Why are you developing a new name? You know, it just didn’t make logical sense to me.
Andrew Hutchison: Yeah.
Morris Swift: And You know he was a bit reticent. You know. Didn’t like the idea of, you know, putting the name there. And neither did I for that matter putting my own name there. You know, I don’t necessarily like this every. Everything, you know, surname, audio. You know, I didn’t like that idea.
Andrew Hutchison: But.
Morris Swift: But I said, look, you’re a known brand. Let’s just put, you know, let’s just call it Serhan and Swift. But I want to make it different. It’ll be Serhan plus Swift with a plus sign because I like the graphic and all the rest. Then we suddenly realize that you can’t put plus into a browser.
Andrew Hutchison: Yeah, yeah, yeah.
Morris Swift: So, you know, and, and it’s going to be very confusing if it’s Serhan plus with, and I, the browser name will be different. I said, now, let’s make it easy. Just Serhan Swift. Yeah, it sounds like a law firm, but, you know, let’s, let’s, let’s just do that.
In audio, people love to know the people behind the brand
And, you know, what I also realized afterwards, which was all new to me, is that in the audio game, people love to know the people behind the brand. I mean, I think, you know, I.
Andrew Hutchison: Think they do, particularly with, a small to medium sized brand that’s a bit more personable and a bit more bespokey, I guess, is that, I, mean, you may as well expose the personalities behind it because it allows you to understand how the sound might be, how the product’s made, the care, the attention.
Morris Swift: well, I can tell you now that when, you know, people ring for service and they say, oh, I’m speaking to one of the principals. Oh, wow. You know, I’m not being, I’m not being put down to the, you know, just somebody who just answers phones.
Andrew Hutchison: I mean, it is, it is, it is exactly the opposite these days, isn’t it, that all of, all of the corporates.
Morris Swift: Yeah.
Andrew Hutchison: Don’t have anyone answering a phone. There’s no phone.
Morris Swift: Talk to our, talk to our, What is it? Our, chat bot. you know, and look at the faqs. But what I’m getting to is, you know, look, if you talk to me, it’s, well, there’s the bloody speaker. You either like it or you don’t, you know, but that’s not the way this industry works. people get a lot of cache, a lot of confidence, a lot of, you know, they want to know that the guy that designed is prepared to stand up and, you know, either take the credit or copper beating, you know, for the product that they’ve designed. and so, you know, from that point of view, having the names there I thought was a good thing. And out of respect to Bradley, he’s got a lot more experience in this area. Brad has just done nothing but loudspeaker design for decades, whereas I’ve been consulting in everything from Department of Defense to communications to medical to, you name it. but as a consultant, but he is the loudspeaker guy. And I can sort of look at something and say, okay, I can talk about manufacturing, and I can maybe do some mathematical analysis and, modeling and, you know, how we’re going to build this thing.
00:30:00
Morris Swift: And I’m, you know, I’m very much into reliability, consistency, and yeah, I know my way around audio stuff, but I would never claim to have what 30 years of experience in tuning loudspeakers gives you, because, you know, it’s a bit like you can know everything there is to know about the human body and physiology and hydrodynamics. Doesn’t mean you can jump into the pool and win olympic gold.
Andrew Hutchison: No.
Morris Swift: You know, you’ve got, you’ve got to do it. You’ve got to do it.
Andrew Hutchison: There’s a lot of little tricks to learn, and he’s learned them, I guess.
Morris Swift: Well, he has, and he has a great ear. And, you know, people develop a way of tuning speakers. You know, speakers is something that you tune. You don’t talk so much about tuning amplifiers, although we do to some extent. But speakers are the big, speakers are the big variable. They make the biggest difference. This is why I say to people, buy the speakers first, because they make the biggest difference. But they’re also a spatial device. You know, back in the sixties, we didn’t talk about imaging, did we?
Andrew Hutchison: No, we didn’t talk about imaging.
Morris Swift: If we could get the sound tonally correct and we could get rid of, distortion and we could have clean treble and powerful, clean bass, we thought, job’s done. Then all of a sudden, along comes the realization that a lot of the listening experience has to do with space and imaging and soundstage. And where are the performers and do they sound the right size? Are they too big? Are they too small? that is part of creating that idea of something that sounds realistic. and that’s where the craft, you know, that’s where the craftsmanship really is. and you can only do so much with modeling, you know, having that ear and having the experience and knowing, how to design a loudspeaker, is based on experience. I don’t want to call it a black art because I don’t think it is, but I think you have to learn what the numbers mean. you know, and designing speakers in accordance with a straight line, it just doesn’t work. you’ve got to know what the thing’s going to sound like. And Brad is one of these things. Guys who can rare guys who can listen to something and say, okay, I know what’s wrong and I know where to look, and I know what to do to fix it. And not many people can do that.
Andrew Hutchison: No, no, no. In fact, it. I mean, it’s a skill. It’s not a. It’s the black art bit. Well, the black art is. Is, interpreting both numbers into what you feel that might sound like, and vice versa, I guess. you know, as far as. As far as getting to the. To the finish line and producing a product that’s exceptionally good. and then there’s all these other aspects to it. I mean, if we started talking loudspeaker design specifically, we would be here for weeks. so we probably won’t. but, you know, it’s this just. I don’t think people for a second realize, you know, just how many angles you can come at with all aspects of the design.
Morris: Just because you have good drivers doesn’t mean you’ve got good speaker
Which actually brings me to one of my pet subjects. Not that we were necessarily preempted that we would discuss this today, but we, both know the other part of the speaker equation, which is, you know, where is the time, where is the money really contained in any, loudspeaker design? And there is a perception amongst some that, you know, those drive units, I’ve just looked them up on the Internet and I can buy them for, you know, $176. So, your speaker is not worth, you know, three grand, five grand, whatever. it’s a gross oversimplification, I think. Have you kind of got any thoughts on that? I don’t probably want to go into the finest of details, but there are so many other things to get a speaker happening.
Morris Swift: I couldn’t agree more. I think good drivers are expensive, but there’s two sides to it. Just because you have good drivers doesn’t mean you’ve got a good speaker. But I often say I wish the crossover was on the outside and people would realize how much cost and expense goes into crossovers. why do I love active speakers? I’m a big active speaker fan because I can build three amplifiers and an electronic crossover for about the same price as it costs us to build our simple passive crossover.
Andrew Hutchison: Yeah.
Morris Swift: You know, in an, in an active system, a capacitor that costs $0.10 when you translate the job into a passive speaker running at much higher current, much higher voltage and much lower impedance, that capacitor is now $5.
Andrew Hutchison: Yes.
Morris Swift: And if you want audiophile grade m, and yes, they do make a difference. It’s now $50.
00:35:00
Morris Swift: In fact, I’ve been looking at a capacitor recently, it’s $500.
Andrew Hutchison: Oh wow. Okay.
Morris Swift: And you know, things like terminals. I remember sitting with Colin Watt now and he was showing me these speaker terminals and saying how good they were. And you know, this was early on and I sort of bit my tongue, thought, oh come on, you know, the typical electrical engineers thing. And this goes to cables, connectors. It’s only 20 khz, mate. Come on, how much difference can it make? Yeah, but our terminals cost us a bomb. And it’s not that we haven’t tried other stuff. We don’t like the way it sounds. And yes, it does make a difference. And then the cabinet, cabinet engineering multi layer cabinets, bracing the way you do the cabinet structure. and it’s not just a matter of making it dead because if that’s what it was, we just make the cabinet out of granite. But you’ve got to absorb and manage the energy too. if a tweeter has a, ah, diameter of one inch and it’s moving a certain amount of air, well, the cabinet has a surface area of hundreds of inches. So m if the cabinet’s vibrating, even in microns, it is coloring the tweeter. And then think about how much energy is in a room. You’ve got a room that’s, you know, thousand, cubic meters and you got 20 people in there and you’re blasting them with audio while the back of the speaker is putting out just as much energy in a box that’s ten cubic, that’s 1010 liters.
Andrew Hutchison: That’s right.
Morris Swift: So yeah, that energy has to go somewhere, otherwise it’s going to bounce straight out through the driver.
Andrew Hutchison: Yeah, that’s absolutely.
Morris Swift: And so now we get into, you know, not just bracing but multi layered stuff trying to absorb the energy before you move. And that’s where a lot of engineering goes.
Andrew Hutchison: Stop talking. So your analogy is superb. You’ve got a one inch, round tweeter, hardly moving. Visually, it doesn’t move, it creates tweet sounds. Why doesn’t the box create almost the same sound of a tweeter? In a way? I mean, obviously I guess it’s resonating at much lower frequencies. But that is such a great analogy because everyone understands that if you put your hand over your tweeter and your speaker, you no longer, have the same balance. It sounds dull and dead because you’ve just blocked out everything above three or 5000 hz or something, or more or less blocked it out, certainly absorbed it with the back of your hand or the inside of your hand. So, yeah, that’s a. Ah, that’s probably Morris. One of the best analogies I’ve heard for cabinet control and the care that you need to design into it. And it’s a slightly. Well, it’s, it’s. It’s a good analogy, but I. We both know that there’s different frequencies probably being handled, but, all produced by the box. The box is not producing ten, kilohertz, I guess we hope. It’s certainly not. Some boxes probably do. But, yeah. How far does a box have to move to create sound? Not far at all. Does it? You know, it’s,
Morris Swift: That that is. That is the point. It. It can color the sound. you know, when people do this rap test with the knuckles, m. I call it audiophile tire kicking, because it doesn’t tell you much information at all other than unless the cabinet is, you know, absolute rubbish.
Andrew Hutchison: Yes.
Morris Swift: And often when people are designing bracing, they think they’ve gotten rid of vibration, but all they’ve done is push the frequency up.
Andrew Hutchison: Yes.
Morris Swift: Where it’s actually worse.
Andrew Hutchison: Yes.
Morris Swift: Than if they had left it alone. And then that’s not to say that a cabinet can’t vibrate. It just means that you have to tune everything to, I guess, somehow utilize the coloration. But if you’re after accuracy and low distortion and low noise. And of course, speakers are where noise and distortion. The terminology gets quite confusing. But if you want speakers that are really clean, you’ve got to manage all that energy. And so this is where the, you know, it’s not just sticking them in a box and making it out of anything. it’s. This is where the engineering goes. And the better the drivers, the better the engineering has to be. Otherwise, you’re just wasting your money.
Andrew Hutchison: Absolutely. Yeah. Yeah. And I guess my point was not so much the cost of the drivers, but people drawing. Conclusive drawing. Well, there is one part of the argument which is that they see what they know to be high end drive units and then could make, you know, not so much an analogy, but could be led to believe that, therefore, that speaker must be excellent or that they could build their own excellent speaker just by buying those drive units when.
Quite simple drive units can’t produce exceptional results
Exactly nothing could be further from the truth. And then vice versa.
Morris Swift: Exactly.
Andrew Hutchison: Would dare to suggest that quite simple drive units can’t produce exceptional results. The actual difference in drive unit performance between very good quality and exceptional quality is. Is the finest of differences, really. And it’s the difference that matters
00:40:00
Andrew Hutchison: when you’re aiming very high and the rest of your engineering is at a high level and you’ve got it right. But, if you’ve made mistakes elsewhere that perhaps the benefits of those drive units to some degree are those more expensive drive units, the benefit is lost.
Dellichord loudspeakers are at the Melbourne HiFi show this month
Andrew here from Dellichord loudspeakers. we’re at the show, the Australian HiFi show that is in Melbourne at the Pullman Hotel, Albert park from the 11th to the 13 October. In other words, a few days, although that would depend when you’re listening. If you’re listening sometime early in 2026, you missed it. So. yeah, because this is 2024 and so we’re in 2204. I think I mentioned that we’re displaying with Alex from audio fix distribution, who imports ear, Yoshino tube amplifiers and exposure electronics, both from the UK. And we’re probably almost certainly releasing a new model. it’s an affordable model. We’re very pleased with its performance and we’d love you to come and have a listen to it. So. Yeah, 2204, Dellichord ear and exposure electronics. See you at the show.
We were talking about loudspeaker component cost or the real costs
And we’re back for segment three of the Not An Audiophile – The Podcast. we did come to a very abrupt end in the previous one as the batteries managed to run out, modern technology and all that, or the opposite of modern technology. We were talking about, loudspeaker component cost or the real costs of, designing and manufacturing any loudspeaker. And I think the point I was going to make before I was so rudely interrupted by my batteries was that, there are many other hidden costs and to you, know, suggest that speaker a, b or c should cost a certain amount based on the perceived value of the drive units or the actual value of the drive units, if you know which ones they are. is kind of wrong. and it probably leads you to. It indicates perhaps how high end a product it is. But the, implementation of those parts is what matters. And, as, Morris, our guest today, Morris Swift, was saying, the crossover, the cabinet, these are, these are terminal posts are all important things.
Getting people who want to build speaker cabinets is difficult, Morris says
well, let’s finish that conversation, I suppose, since we were interrupted. Do you have any closing remarks on that, Morris? And I mean, you’re at the sort of mechanical engineering end of the speaker thing for Sir Hannah Swift. You make it all fit together, at least that’s my understanding. And then organise the manufacture of all of bits. what have you found to be the most distracting, sorry, time consuming and annoying thing to be, to be organising in an Australian made loudspeaker.
Morris Swift: Oh, gosh. well, as you know, we do our cabinets here now. I’ve always wanted to support the Australian industry, but, you know, getting people who want to build speaker cabinets is difficult. We outsource our manufacturing, and so, most of our suppliers don’t just do speaker cabinets.
Andrew Hutchison: No.
Morris Swift: So, for example, we have a high, end joinery company doing our, cabinets. And, you know, if somebody walks in and says, hey, I need to do, you know, a high end kitchen worth $100,000, well, guess what? Our cabinets are going to be put on hold for a few days. you know, it’s, it’s just the way it is. There’s nobody doing it specifically. but at the same time, the kind of is, well, aside from yourself. But then again, you do up, you do other products as well.
Andrew Hutchison: all sorts of things. But yeah, there is actually, I mean, probably the biggest cabinet maker in the country for loudspeakers would be, clearly would be cricks in South Australia. But, they do their own track. That’s right. They don’t. They do their own, which is a shame.
Morris Swift: So, you know, well, that gives us a choice, you know, do we, I mean, the CNC parts easy. You can buy a CNC for not a lot of money, but then, you know, maybe 20 grand. But you. But then you’ve got to get the pieces, you got to put them together, and you’ve got to have skill. You know, you can’t do this stuff without skill. And, painting in particular, you know, spraying a speaker box is not like spraying a panel. and a lot of the painters, you know, love, you know, when they do a kitchen, they’re painting panels, doing a three dimensional object with cutouts, you know, having to spray from underneath, for example, or rotate the object as you paint it. I mean, look who I’m telling. you know, the way the paint flows around corners and edges. And then in our case, we flush mount our drivers. So we need absolute precision in the cutouts. So you’ve got to then control how the paint flows around the cutout. and which is one, you know, one reason why, you know, in some ways, timber finishing is perhaps a little bit easier, maybe, but then you need, you know, skill in finishing it well. And, you know, we’re just finding that a lot of those skills are disappearing or people just
00:45:00
Morris Swift: are not as interested. They are, in doing things to the standard that we want. And you know, I’m convinced that, you know, dust has a consciousness because, you know, dust can think because when you get a speck of dust on your enclosure, it will always work out how to go on the front panel where it’s the most visible. It will never go underneath. That just does not happen.
Andrew Hutchison: No.
Morris Swift: So I’m convinced these things have a, have a consciousness. So, you know, being a bit facetious, but it’s not an easy process. You know, we have to often respray cabinets to get the finish that we want. and I’m not saying that we couldn’t invest a million dollars and get it all done by robots and all the rest of it the way the big boys do, but as a small scale producer, those things are just not available to us. But at the same time, we’re extremely fussy about the stuff that we do. so that’s part of the difficulty, getting people who understand that and are willing to do it when they can be making a lot more money doing other stuff that’s easier to do.
Andrew Hutchison: Well, perhaps there’s a big difference between manufacturing things in Australia and perhaps say, ah, in Europe as an example where you have specialist cabinet makers that just do loudspeakers, that you can basically send them a drawing and get a price and have a conversation about how it’s going to be made and they’ll give you some kind of indication of cost. This is not something that we have available to us in this country other than really only just ourselves. And sure, we do it in a tiny way, and we’re not going to be doing it in a bigger way because I can’t get the people that I need to help me do it. So there’s only so many hours in a day. And that’s the problem because I imagined when I started stereotech that I would employ one or two talented, young people with lots of enthusiasm and excitement for doing quality, cabinet making and painting. And this is not worked out. So, the lack of interest in getting one’s hands dirty is, not to be, discounted. It’s a problem and it’s something that I think the whole world is going through. It’s to change. There’s so many career opportunities where you don’t get your hands dirty and you don’t breathe in the occasional bit, of chemical, when the math. Well, but you know, it’s, well, you.
Morris Swift: Just write an app. Just write an app and sell it. Sell it for a million bucks.
Getting reliable supplies and getting consistent quality is difficult for small manufacturers
You know, but the other point that I want to make, and I’m sure you know all about this, is when you get into more exotic materials. For example, like birch ply. You know, not everything’s made out of chipboard and MDF. Try and get consistent grade birch ply throughout the year. Every shipment is slightly different because it is a natural material. It’s grown. And particularly since COVID you know, getting reliable supplies and getting consistent quality is really, really difficult. And yes, what you make the cabinet out of, it matters. It matters a lot. So that’s another headache is, you know, consistency of the materials that you’re using and, you know, how you, how you deal with that in manufacture and in design. you know, so, and, you know, little things matter. For example, our crossovers are fully hand wired. And we were. I was surprised at the difference it made sonically. In fact, we changed the way, I looked at the crossover and I made a few changes, partly for efficiency, but partly because I thought it would be electrically better. And we didn’t tell anyone and we just incorporated that change. And then the phone started ringing. What have you done? And I thought, oh, no, we’re in trouble. And it was, no, these are way better. We can hear the improvement without telling anyone, anyone, anything. So it actually worked out. It worked out well.
Andrew Hutchison: It could have gone the other way.
Morris Swift: it could have gone the other way, but, you know, but then you also go down this rabbit hole where, you know, how much detail engineering do you put into a speaker? You know, it’d be nice if it all went together like Lego and if none of these things really mattered and if you could get, you know, some kid who just, who had just learnt what end of a soldering iron is the one you hold to do your soldering. it’s just not that easy. There’s a lot of skill, and, you know, feeling that goes into assembling a quality loudspeaker. And yet, you know, I spoke to one company in the states at one of the trade shows and I said, gee, that’s, that’s a pretty impressive speaker for the money. I said, how many of these do you make? And he said, oh, 20,000 at a time. Wow.
Andrew Hutchison: Yeah. Okay. And this, yeah, you’ve just reminded me of my point where before that we
00:50:00
Andrew Hutchison: had the battery, incident, that was, that exactly was where I was headed. Is the small manufacturers up against it as far as simply the amount of, pieces they’re going to make? And if you divide your R and D into 100,000 pairs versus 100 pairs. you can spend a year developing a model, and, it really only costs, you know, it’s an hour’s worth of time per pair of speakers, if that. Whereas small manufacturers, obviously the R and D, because the same amount of time is spent developing the product, it’s not like you can spend less time. In fact, you probably spend more time because you spend it slightly less efficiently than a larger manufacturer’s bigger laboratory, etcetera. So, yeah, they might have.
Morris Swift: Well, I’m going to contradict you on that. Okay. you see, the big guys have economy of scale.
Andrew Hutchison: Yes.
Morris Swift: But they also have momentum.
Andrew Hutchison: Yes.
Morris Swift: They cannot change things on the fly. and in fact, I did a project some years back, nothing to do with audio, but we had taken a product from concept to reality in six months, and we had a component supplier say it would have taken us five years.
Andrew Hutchison: Oh, wow. Okay.
Morris Swift: Simply because of the momentum, the red tape, the cost of setting up, the way they did things. So to some extent, we have a flexibility. No, we don’t have their economy of scale, but at the same time, we also don’t have their overheads. I mean, if their business just hiccups, they’re out the door backwards. I mean, what do you think happened to compact computers? They didn’t predict things correctly. What do you think happened to some of the big semiconductor manufacturers? They didn’t see, you know, they didn’t predict things adequately. In some cases, they said, oh, there’s going to be a downturn. They got rid of their skilled staff, then all of a sudden there’s an upturn and they can’t catch up. They don’t have the staff anymore. So we have that flexibility. And also we can do things in manufacture that they cannot afford to do. They’re more highly, highly automated. There are processes that they just cannot afford to do. Every set of speakers that we do, and I’m sure same with you, is every pair is individually tested, individually measured and listened to before it goes out the door. Now, if you’ve got customers that understand that and are prepared to pay for it, look, I often compare it to Aston Martin. Aston Martin still hand beat their panels, do they? Everything, everything is done by hand. Well, that was the last documentary I saw, which was a while ago, showed them hand beating their panels, maybe. Yeah. But a lot of stuff is, is still done by hand. You know, the leathers are selected.
Andrew Hutchison: Oh, absolutely. I think, yeah, a lot.
Morris Swift: And there are going to be cut. There are going to be customers who, are prepared to pay for it. The only difference is with audio, much of it you can hear. I mean every component that comes in we measure, we remeasure and calibrate every component and hand match all the, all the components that go into every pair of crossovers. Now the big boys are not going to be doing that.
Andrew Hutchison: No, no. I want to make a point about the big boys is that and this is where the end user, the person buying the speakers and enjoying the music through them may not realise the big difference between a large manufacturer making 20,000 pairs and you or I making you know, a six or twelve pair batch or whatever is, is that consistency, that quality, not just quality control, but the fact that every inductor is, is trimmed and is the exact value of the next one etc. Etc. And, and also the complexity of how the product fits together. It’s. We are ah, less concerned about you know, how difficult or easy it is to put together. If the result, you know, the sound quality is worth it, will take the harder path. Whereas a large manufacturer, I’m sorry but everything is just literally thrown together and very much thrown together in a it has to be because they’re using semi skilled staff to screw everything together and has to be done in such a way that that person who’s not an electronics guy can fit it together adequately well. And so everything sort of slung together with connectors and hot glue and a few staples and that, that’s that product and that’s not exactly bespoke. Well I call bespoke’s not the right word, but small volume manufacturers are potentially ah, doing a much nicer job of actually you know, putting the product together and Some, some are some aren’t. Ah, but I mean most, absolutely, that’s why they do it. They want to make a first class product. And I think you know, the old days of buying a pair of speakers and it lasting 30 or 40 years
00:55:00
Andrew Hutchison: is most likely to happen now with a, with a small manufacturer where the quality of the product, the components used is very high and the care with which it’s screwed together is very high.
Pulling other people’s manufacturing apart is becoming less common
And as someone who for a living has to pull other people’s manufacturing apart and try to make it work again, this is something we’re seeing less and less of. you know there was a time back in the day when it was everything, you know, well it wasn’t fancy but it was used, it used good materials and it was and it was screwed together in such a way you could get it apart again. And this is less the case now. And of course, in the bottom end of the market, forget it. You just drop it in the wheelie bin. I mean, if you think that you’re, repairing a JBL, I guess I’ll use a brand, or some other harmon $369 product. Just drop it straight in the bin. I couldn’t even tell you how to take it apart. It will clip together in a way that no one would understand except the person who designed the, plastic clips.
Morris Swift: I often say we don’t want to see our product in the council cleanup. we want, we consider our product of investment. But the important thing is that we don’t just do this for the hell of it. Most of these things, to some degree, are, audible. If you put these in a high end system with good electronics and everything fine tuned, you will hear. It’s extraordinary, the things that you do hear. It never ceases to surprise me. how. Just little things. you know, how you mount the drivers, you know, how you put things together and all the things that we’ve been alluding to, they’re audible. That’s, that’s the whole, that’s the whole crux of it. We’re not just doing it. So we say, oh, it’s better made, but it is audible. And if you, if you start to slip up.
Andrew Hutchison: Yeah, that’s right. That’s what’s annoying.
Morris Swift: You’re going to know. Yeah, you’re gonna know.
Andrew Hutchison: So I, So we’ll sort of, we’ll stop the, the unpaid ad at that point. which, which it isn’t, but, it’s, you know, we are harping on about our own efforts a little bit.
Sir Hannah Swift has been working in audio since childhood
I’m interested to know. So you got that interest in audio at a very young age, and then you sort of worked in all kinds of industry related to electronics, but then you’ve come back audio, you know, later in life, I guess. But, have you. I mean, what’s your, what’s your audio highlight other than being part of. Here we go again. Another ad. Sir Hannah Swift team. other than that, what, what’s, what’s some of your highlights in the audio side of things that, you know, things that have, You look back and go, wow. And I could be, I could be talking about something you’ve heard of. I could be talking about some, product that you’ve owned, or what have you.
Morris Swift: Look, I think getting excited about some of the technology. I mean, if somebody had said, you know, years ago that you could have a gadget like an, like a, like an ipod nano the size of a credit card, not just storing thousands of tunes, but doing it with quite outstanding fidelity, that, impresses me. you know, I’m impressed in what with what you can do with silicon. And I’ve got a saying which is silicon is cheaper than copper. And this alludes to things like what you can do with digital processing, what you can do with the dreaded class d amplifiers, which I’m a huge fan of the technology in terms of, you know, what you can do with it. M, you know, 200 kilogram amplifiers just don’t impress me. But a thousand watts that you can lift up in the palm of your hand, that impresses me. I’m about elegant engineering stuff that people have sat down and really had to think about to make it work. But once they do make it work, once you make some of this stuff work, it’s like, aren’t it, you know, baking biscuits, you know, it’s all pick and place. Robot surface mount.
Andrew Hutchison: Yeah.
Morris Swift: you can make it so cheaply. And what I love about that is now high quality audio is accessible to just about anyone. And I love the idea. I love the idea of accessible audio. I get more excited at the idea of putting together a system for under ten grandd that blows people’s socks off. Then I will ever get excited about a megabuck system, which don’t really excite me much at all.
Andrew Hutchison: Well they can, they can be exciting, but yeah, either way, you know, they are not exciting.
Morris Swift: But who’s going to buy it? No, no, the sad thing is, the sad thing is I think a lot of people buying that stuff are collectors.
Andrew Hutchison: Yeah. Okay.
Morris Swift: They’re not people who want to listen to music. What I love is, you know, when we have a ah, difficult customer, as we had a while back, the husband wanted the speakers. The wife clearly didn’t. Yeah, but when she heard them, when we went to their place and did a demo, yeah.
01:00:00
Morris Swift: The wife just said, oh my God, I’ve never heard it like that before.
Andrew Hutchison: Is that right? Yeah, that’s good stuff.
Morris Swift: And you know, and when that happens, I thought this is why we do it, because it isn’t for the money. I could make more money flipping apartments, much more money. But we do it because, you know, there’s a certain passion and an art. And at the same time, what I love about audio is the, is the number of times you go, well, shit, that wasn’t supposed to happen. And aside from smoke pour. Aside from smoke pouring out of an amplifier, which not so good, but, you know, the fact that you’re always learning and you’re always finding out, I don’t know quite as much as I thought I did. And, that, for me, that’s the excitement. Because if I thought I knew everything, then I’d take up basket weaving or something else. I’d be bored.
Andrew Hutchison: There’s something to learn every day, isn’t there?
Morris Swift: That constant journey of discovery. and the fact that, look, at the end of the day, I’m not going to use the old cliche, it’s all about the music, because it’s not. But we enjoy, we love the fruits of our labors. You know, every time I put up a pair of Mu2’s to the listening test, I think, you know, they’re pretty bloody good. You know, they really are.
The industry just has not adopted active and, and dsp
Andrew Hutchison: Well, you’ve sort of created a small, a small piece of a small offspring, really, haven’t you? I mean, I mean, that’s, that’s. I guess that’s why manufacturers are in manufacturing to a fair degree, is you’re making something, you know, it’s a tangible thing. You can hand it to someone, they can plug it in and get it to make music. And I mean, I. There’s this, you know, you talked about writing an app earlier and that’s what a lot of people are doing, so much apps. But you know, whether it be software, anything software related, ultimately it’s kind of cool for a second when it does what it does and it does it well and does it hopefully without crashing. but then it’s kind of nothing, isn’t it? It’s just vapor and And that’s you know, electrons zinging around or whatever. And Yeah, it’s tangible products and making them is a, ah, is a very rewarding, thing. And I guess it’s something that a lot of people are going back to. I mean, there’s, there’s plenty of, 2030 and 40 year olds who, you know, brewing beer or something or making cheese or.
Morris Swift: Well, I tell you what we’ve omitted. And that was that. The Mu2 almost didn’t happen. Because when I approached Brad, it was. Well, I’ve built these. I already had some active speakers I had built back in 2005. And everybody who heard them said, you’ve got to capitalize on those. They sounded fantastic. They were also huge. They were huge. They were like one and a half meters tall. You know, a meter wide. you know, they were big things. But then, you know, I won’t go through the whole history, but the Mu2 was done as a stopgap because, well, we needed some cash flow and our active speaker wasn’t quite ready. And then we learned at the time, audio files and even people into high quality audio were not buying active speakers. And the Mu2, everybody that heard it loved it. So it was kind of, well, this speaker almost didn’t happen because we didn’t actually set out to build a passive loudspeaker. Or at least I didn’t when I said, brad, I want you to help me build a speaker. you know, so it’s quite funny how the Mu2 did evolve. And you know, it was the customers that ultimately created the pool. because our original intention was to go active, active dsp and all the rest of it. So it was going to be a stopgap, but it kind of took over.
Andrew Hutchison: Yeah. It’s an interesting thing that the active dsp is such a great solution and of course is almost universal now in pro audio. but it hasn’t at all made, a place for itself in, in HiFi audiophile home listening circles. It’s it’s a, Lots of people have got it and those people love it. But I would say that that is less than 5% of customers. I mean, clearly you go to a giant audio show and it’s, it’s 95%, if not more passive loudspeakers. maybe that’s not quite right. When I think of some brands, they, you think, think of them as passive, but perhaps they’re actively, driven, but by giant class ab amplifiers. But.
Morris Swift: Well, what’s interesting, I don’t interrupt you, but what’s interesting is it’s taken off at the low end.
Andrew Hutchison: Yeah.
Morris Swift: So you’ve got your thousand dollar active speakers, but as soon as you go up in, in price and performance, aside from exceptions like maybe meridian, you know, the industry just has not adopted active and, and dsp. you know, it’s, it still is, it still is. The vast majority are still passive loudspeakers. And I think, you know, that’s interesting in itself, given how other areas of technology have moved and also, as you pointed out, how the professional, people have gone.
Andrew Hutchison: Yeah,
01:05:00
Andrew Hutchison: well, not everyone in pro. I don’t think. But it’s certainly the majority of pro audio in all areas, whether it be studio monitoring or in, obviously in, you know, in big venue systems. Oh, yeah. Absolutely active. But, yeah, they. And I guess they’ve just gone, yeah, this is the best way to do it. Whereas we. I mean, that’s. I guess that’s home. Hi, fights. Hardly surprising it hasn’t taken off and away because we’re still playing records and using tubes, as we both mentioned earlier. So it’s perhaps not surprising. but look, it is. It does. Of course, I believe this is the reason. The key reason is that you can’t then experiment with different amplification. And, that’s an integral part of the hobby, if you like.
Morris Swift: You know, I think if audiophiles were building a car, they were buying a car, they’d probably buy the engine from one company, the brakes from someone else, the suspension from someone else, and probably end up killing themselves. That’s another story.
Andrew Hutchison: Well, yeah, it would be. There would be some interesting cars driving around, that’s for sure.
Morris Swift: There certainly would.
People like different things. Remember that what you’ve also touched on
Andrew Hutchison: The homer comes to mind, if you.
Morris Swift: Remember that what you’ve also touched on, and I think it’s very important, is there’s no absolute different. People like different things. And you know what? That’s okay. And if you are a tweaker and you are into the equipment more than the music, that’s okay, too. It’s just a different aspect of the hobby. It’s like the people who buy a Ferrari, but they never drive it. It’s in a museum. They just want to look at it. And m then there are the people who want to buy it and pull it to pieces, you know, from the get go and think they can make it better. And then there are people who drive it and don’t care if it gets scratched or dinged because they love the driving. So they’re all Ferraris, but they’re different aspects of that particular, thing. And I think the same thing happens in audio. If some people are into just the sound more than the music, well, that’s okay. Who am I to judge? That’s fine. It’s just not my aspect of the hobby. Ultimately, I want to listen to music, and I want the music to sound beautiful and to create an experience rather than an experiment. When we work developing our products, we are doing an experiment. When you listen to music, it’s an experience. Yeah. I think that’s what’s unique about this, those two aspects of what we do. you know, the measuring and all the precision and all the engineering. And at the end of the day, you just sit back and you enjoy it. And that’s what makes this so special.
Andrew Hutchison: Agreed. Absolutely. and look, I think on that note, we might wrap up, but unless you’ve got some particular point you want to cover, because obviously we’re going to have you back on the show because there’s a whole bunch of things that you and I have spoken, about on previous occasions that we feel strongly about, and yet we’ve managed to not mention any of those things today. So, I don’t know quite how that happened. the inability to stick to a script would probably be the main reason, on my part at least.
Andrew: Morris, thank you for joining us today on the podcast
So, I mean, there were things that we mentioned in a brief phone call earlier today, who are talking about noise, of all kinds, in an audio system. And I think that’s a subject in itself, and how some of the noises that we’re referring, the types of noise, are things that people probably don’t realise exist. In fact, perhaps the least important one is the one that they spend the most time concerning themselves with, which is, you know, electrical noise in the mains power, when there are many other noises, in my opinion, that are more important. So look, keep going, Morris.
Morris Swift: No, I was going to say that, you know, noise is just one word, but it is such a complex subject. And it’s not just the noise itself, it’s our perception of it and how we process it. And it’s often key to how we perceive something. It’s a huge topic.
Andrew Hutchison: It is. That’s where I’d like to go next. So,
Morris Swift: Okay.
Andrew Hutchison: I’d like to cover that in some detail because you’ve got a great grasp of how it works. And I’ve got things I want to complain about. So I thank you again, Morris, for joining us today. It’s been greatly appreciated. Very interesting. and I would like the audience, if you’ve enjoyed the last four and a half hours or however long it went. if you’d like it to. It’s. Yeah, anyhow, I’m, I think it was actually quite short as, Not An Audiophile – The Podcast go. This is a shorter one, but any just we’d like you to follow, and like, and subscribe and all of that stuff on, on the various platforms that the podcast is available on, whichever one you’re using. That would be much appreciated, so that other people can, then find us and Yes, thanks again, Morris. We’ll, I would say we’ll be talking again within the next week, or three, and, discuss the, issue of noise, among, amongst other things.
Morris Swift: Terrific.
Andrew Hutchison: Thank you
01:10:00
Andrew Hutchison: again. and we’ll see you later, folks.
Morris Swift: Much appreciated. Thanks for the opportunity. Andrew. A pleasure, a pleasure.
01:10:06