Not An Audiophile – The Podcast featuring Andrew Hutchison from Dellichord loudspeakers. As well as hosting Not An Audiophile, Andrew designs for Dellichord and chats about his loudspeaker design philosophies. In this episode, we specifically explore Andrew’s step back to a time where sound quality was the ultimate goal in a loudspeaker. With the 70S Model, unnecessary “bling” is nowhere to be seen. Instead the design is a 70’s aesthetic with a quality of sound that far exceeds expectations. Andrew has also broken the mould by offering this model as a 70S RTA (ready to assemble kit) and a 70S RTP (assembled requiring painting) as well as a 70S retail ready model.
Podcast transcripts below – Episode 009
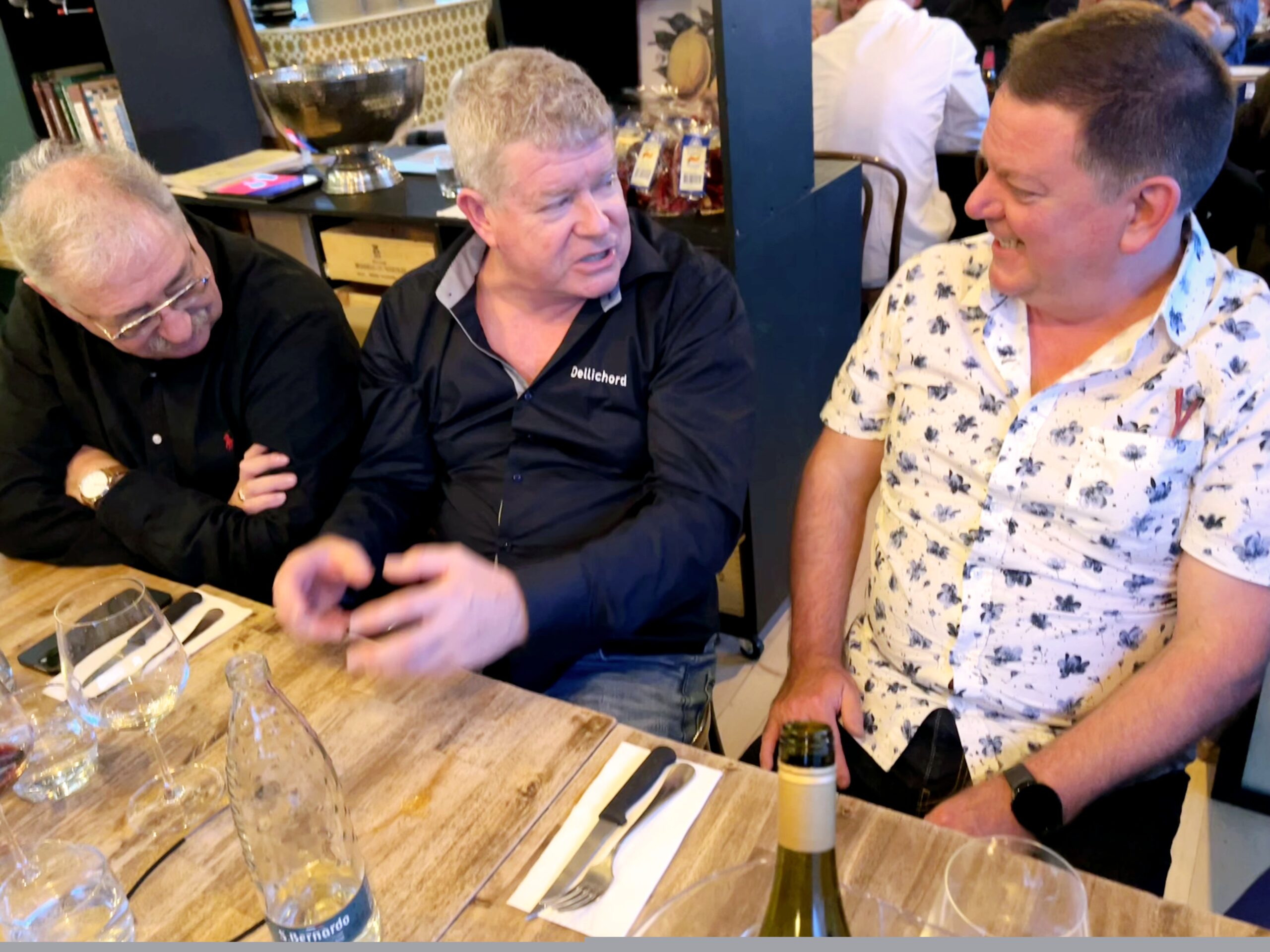
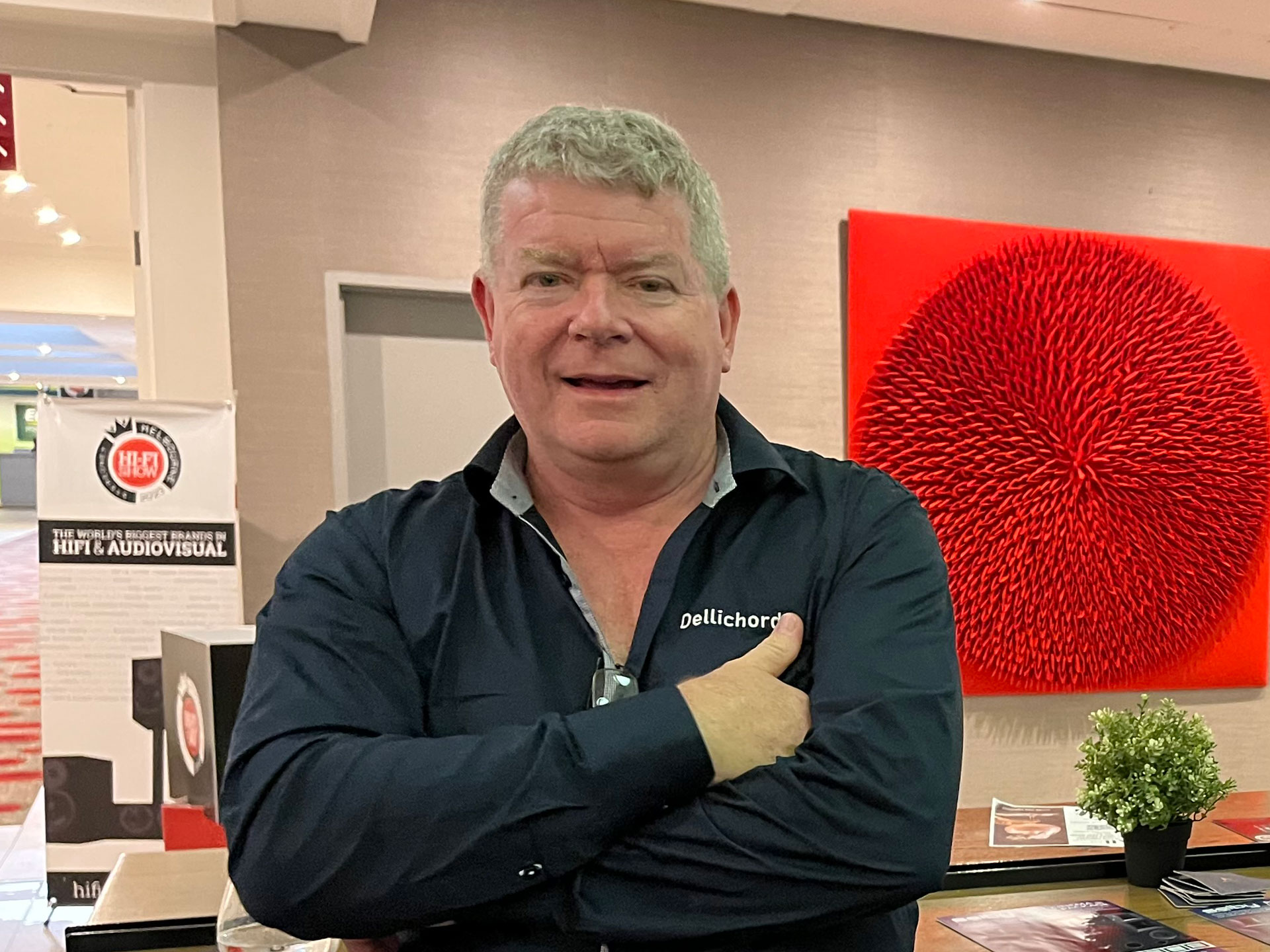

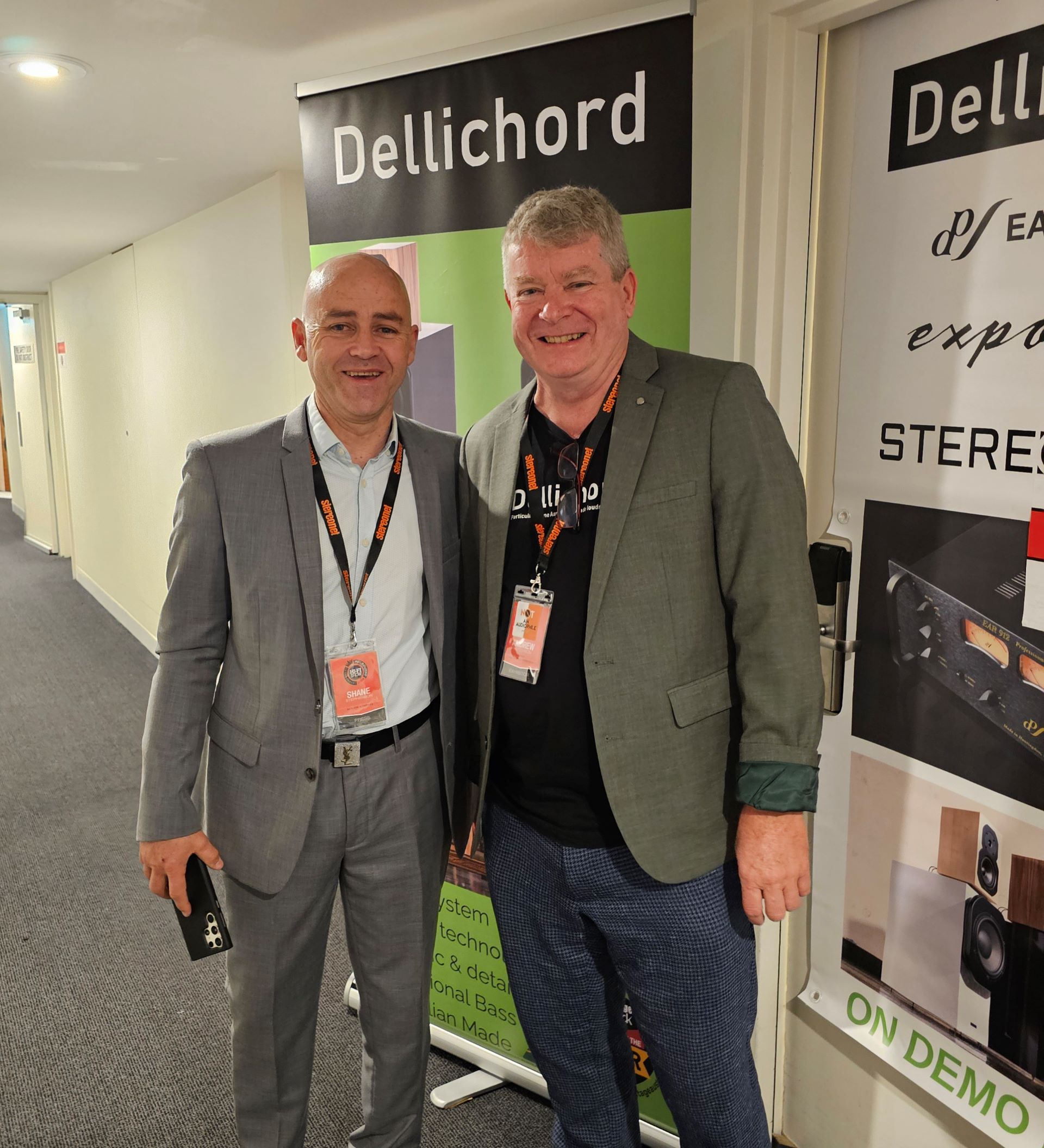
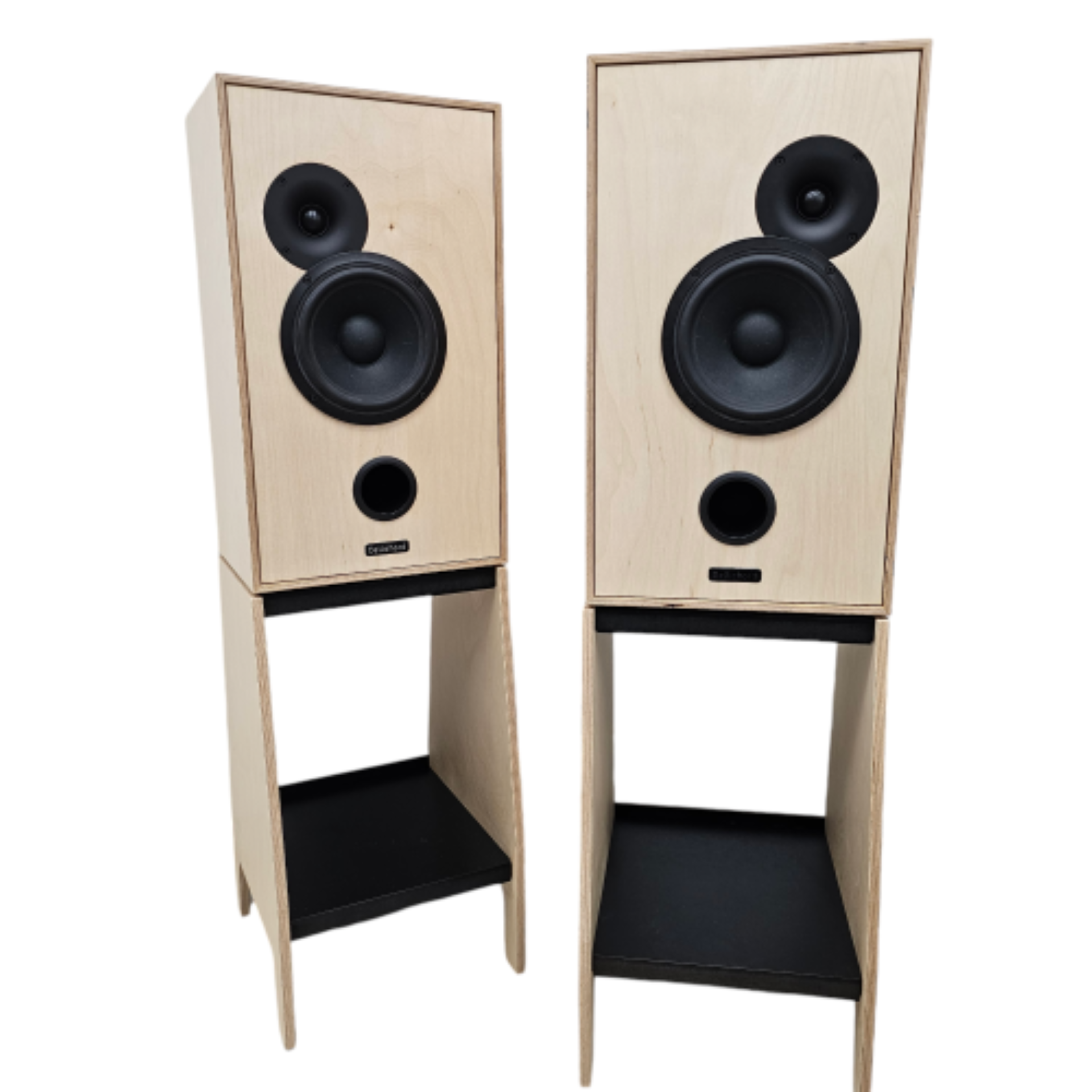
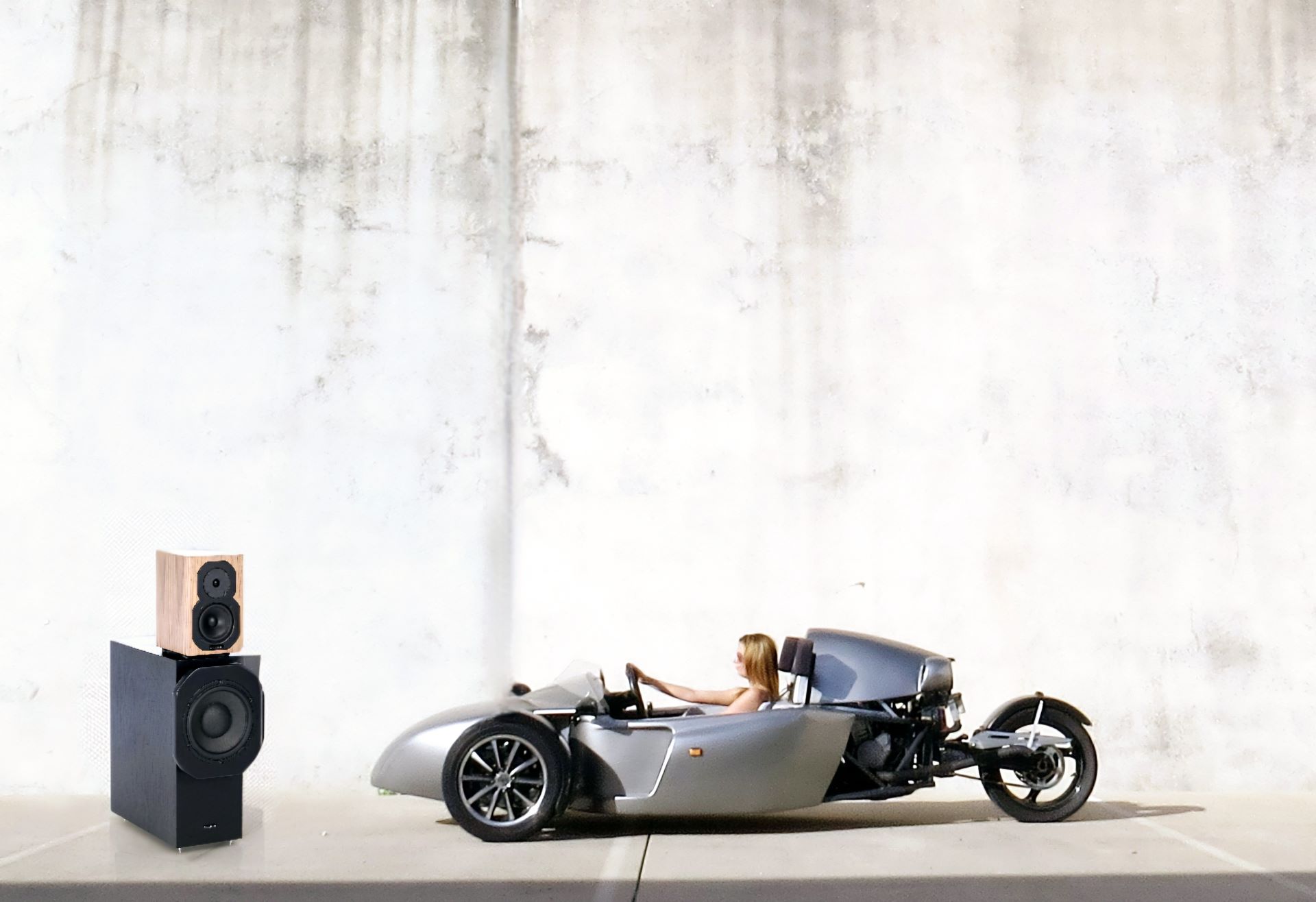
TRANSCRIPT
SEASON 1 – EPISODE 009 – Andrew Hutchison on Dellichord design decisions
Today I interview myself about the new Dellichord 70S Model
Andrew Hutchison: Well, what else? That’s right. So the next step is. Well, okay, so grilles. grilles are the stupidest things. And loudspeakers.
Sharron: I hate grilles, bar none. grilles ugly.
Andrew Hutchison: They perform no useful functioning except keeping children and cats off your speakers. My advice is, and hello, this is not an audiophile. Episode nine. Today I interview myself. No, that’s not quite true. Sharron’s here. Sharron’s going to interview me. We’re going to talk about the new Dellichord 70S Model, which I have been working on and off on for some years, actually. But, we have finally got it finalized and are displaying it and releasing it, for that matter, at the stereonet australian HiFi show in Melbourne at Albert park in the next few days. Sharron, how are you going?
Sharron: I’m good. How are you going?
Andrew Hutchison: Oh, I’m going good. So you’re going to be the host today?
Sharron: I’m going to be the question asker.
Andrew Hutchison: the question asker.
Performance is the number one thing when designing a loudspeaker
Well, would you like to ask the first question?
Sharron: Sure. So tell me, as a small manufacturer, ah, for Dellichord, you’ve already got three loudspeaker models. Why do you need another?
Andrew Hutchison: Oh, well, you always need another. you can never have too many loudspeakers, otherwise no one would be making loudspeakers because the world has thousands of them. Right? So beyond thousands, no, no. There’s a particular goal that I had in mind, which was building a loudspeaker in Australia, of course, as, as I do in our own factory. But, the goal, design goal being only for performance. Performance is the number one thing, with the second goal being the lowest possible cost. So for that, you know, different priorities suddenly become a, ah, priority.
Sharron: So this new, brand new loudspeaker that you’re revealing at the Melbourne HiFi show, on the 11th to the 13 October, this is completely different to the other three models, or it has similarities.
Andrew Hutchison: Nice plug you got in there for the show. yeah, completely, different. And I could go on and on about the differences, but it’s best that I don’t because it’ll take hours. Because the reality is that designing a loudspeaker, there are so many questions, so many things to think about, so many tiny aspects and large aspects. So in this case, if you want to increase the performance, well, you’re going to have to design with performance only in mind. That’s going to be the only way. So a lot of modern loudspeakers, have performance, I would suggest, as a low priority. That sounds ridiculous.
Sharron: So you’re saying that a lot of other loudspeakers are made to look pretty, and that’s where most of their money goes.
Andrew Hutchison: That’s part of it. It’s just, it’s. It’s probably more technically fundamental than that, where, you know, there is. I mean, there are, outrageous examples where a speaker is six or eight foot tall and has 27 drive units on the front. I mean, clearly, that is utterly ridiculous. That’s. That is not how you get a better performance. It’s how you make a crazy looking speaker. so the best loudspeaker is one with one drive unit that if, in an ideal world, you would have one drive unit that would go from 20, would have perfect dispersion on and off axis, well controlled across the whole range of its output. So that’s, that’s the ideal goal. There’s zero box resonance. I’m speaking fast because I want to cover a lot of stuff. There’s so many things. But that is, everyone knows that’s the ideal loudspeaker, one that has these imaginary attributes. Now, that never happens in the real world, but. So then you want to refine. Well, what’s the laundry list of the most important design attributes?
Sharron: what’s the laundry list?
Andrew Hutchison: If you’re designing a laundry list, I think it’s something. I don’t know. It’s an americanism, which we seem to be using more than we should. Something to do with going to the laundry. I mean, I really don’t know what is on the list.
Sharron: What’s the important list of things that you need to tick off as a loudspeaker designer?
Andrew Hutchison: No, I can’t answer that question, but, it’s too long.
The FR, uh, 35 is a smaller speaker designed for music
But, okay, maybe we’ll just talk about this model and maybe versus the other three models we currently have. So there’s the little fr, 35, which is kind of like a sort of a modern interpretation of
00:05:00
the classic BBC ls three five a using slightly different materials and I and cabinet vibration reduction ideas, but similar drive unit sizes. Same 19 mil, 20 mil soft ohm tweeter, same five and a quarter inch base, mid out of, similar materials. Sounds, a little different because we’ve applied a slightly different priority as far as how we wanted it to sound. because a smaller speaker designed for music, whereas the three five a was originally designed sort of for, mainly voice monitoring in a small environment.
Sharron: So it’s an improvement on the ls three.
Andrew Hutchison: It’s an improvement, but that would depend on your outlook. So you’ve got that and that does the job well. And then that works rather well. Placed on top of the Fr 20 bass module to make it full range and active. So that becomes a bigger. I, mean, it’s a huge sounding loudspeaker in a relatively small, footprint.
Sharron: Yes. So this is the fr, 2035 is a three way with two pieces.
Andrew Hutchison: Yeah.
Sharron: Separate enclosures, monitor on the top and the bass module on the bottom.
Andrew Hutchison: Well, the goal there was to reduce cabinet issues, vibrations, resonances. What have you ingested? The frequency ranges that those two speakers output. So the idea was to get the resonances in the small box as low as possible. And the resonance is in the base box, probably higher than the base range that it’s actually outputting. and it was also about footprint. It’s quite narrow, it’s deep, doesn’t take up much space. And that’s what a lot of modern speakers are trying to do. You know, narrow fronted, deep, tall floor. Standards are all about getting box volume, but not width. But this is where the other. The newer model comes in.
The fr six is our original, um, better known loudspeaker
But before we talk about the new model, let me just cover the fr six, which is our original, better known loudspeaker.
Sharron: That. ₩1. A couple of awards, right?
Andrew Hutchison: Oh, thank you for mentioning that. yeah, look, it’s a pretty good loudspeaker, to say the least. I think it does well on the bass because it’s an isobaric design. So two drive units doing the job of one. It has great extension, for its size of enclosure. It uses a passive radiator on the back to avoid the volume that a port takes up and the turbulence that a small or too small a port would create. So, that design goal for the fr six was the smallest box with the greatest base extension.
Sharron: And that’s a classic look box.
Andrew Hutchison: Yeah. It is what people think a speaker looks like. So the new. And we’re glossing over those attributes of those three models to some degree because we want to move on to the.
Sharron: New one because the new one is different. Again, it sounds different.
Andrew Hutchison: It sounds. Okay. Here’s the thing. clean sheet of paper. performance is the absolute goal. Appearance, not a priority at all. So there’s your biggest difference, although I.
Sharron: Have seen it, and I really, really like the way it looks.
Andrew Hutchison: Well, that’s great. and thank you for saying that, Sharron. that $50 I gave you earlier was well spent, but the reality is it may or may not be anyone’s cup of tea to look at, but it really sounds great.
Sharron: And, that’s because there’s no guarantee that any loudspeaker is going to be everybody’s cup of tea.
Andrew Hutchison: No, absolutely not. No, everyone likes a different thing and I’m fine with that. but the goal, the overriding goal was sound quality. So I didn’t care how it looked. Which is. Which is a ridiculous thing to say. No, but it’s. Because you don’t have to. Because the reality is the. The little three five a homage. Homage is it’s the same size and it looks like a slightly better or more modern proportioned three five a and it’s quite cute and nice. Comes in premium veneers. It’s very well made, if I say so myself. And it. And it sounds pretty good and it’s. It’s a bit sharper price than a three five a and it’s a. It’s a great loudspeaker. But the performance, believe it or not, was not the number one goal. The performance or the goal. The number one goal was to actually make it look a bit like a three five a to make it integrate.
Sharron: For the 2035 and make it the.
Andrew Hutchison: Right size to fit on the bass module. Yeah, sure. That was always in mind, even at the start. The fr six. The goal was that it looked well, very well finished. that it looked as well made as any other loudspeaker and it looked fairly normal. I’m doing inverted comma marks. Classic, in the sense of what loudspeakers have been since the early nineties. So
00:10:00
Andrew Hutchison: narrow. narrower than, the depth. And in the case of a stand mount. This is a fairly large stand mount, but it’s not a big box.
New MDF speaker is a relaxed hark back to the seventies
Now, this new speaker, to cut back to the chase is. Well, let’s just cut to the chase. It’s a wider baffle. It’s called. The play on seventies is, of course, the seventies. So it is in the early seventies. And here we get to the philosophy of why it is the way it is. The seventies loudspeakers were simpler in design. it was an experimental time. They were somewhat, you know, random, but they were all similar and that they were wider than they were deep. As a general rule, not all, but many. they had larger drive units, which is maybe one of the reasons why they were wider. They had, in many cases, pretty, mediocre cone tweeters that could go quite low. And so a simple crossover was all that was required. Now, the advantage of that. The advantage is a simple crossover but, the sound is quite often a bit coloured, not super accurate, but it has this certain charm, this ease, this relaxing nature. And people, humans can detect that and they display that desire for that sound in the strangest of ways by wanting to restore radiograms and other awful speakers from the late sixties and early seventies.
Sharron: Which seems to be a current trend.
Andrew Hutchison: Which is been around for a while. But the point is you listen, and here’s the thing. You listen to AM radio on a valve radiogram through the full range, eight inch or six by nine or seven by ten oval speakers, and you go, that is not high fidelity, but it has this ease, this charm. and the charm is the relaxing. It’s kind of, it’s kind of like listening to live music from a distance nature where all of the top end is dissipated.
Sharron: So you’re saying that the new speaker is a relaxed hark, back to the seventies style, simple, live from a distance kind of sound.
Andrew Hutchison: Live from a distance? Yeah. Not a nightclub, just nightclub with no bass.
Sharron: You didn’t pay to get in. You stood outside the fence and heard.
Andrew Hutchison: It from something like that. But, the answer is no. It’s nothing. But the thought is absolutely to capture the ease, the lack of fatigue, the simple sound that washes over you and you don’t have to think about it and it doesn’t immediately sound HiFi. Although maybe there’s a bit of that because it is because the new speaker is quite uncoloured, like we’ve been throwing around the on axis and or some of the frequency response measurements from it. this morning I did up a chart with the off axis, some off axis measurements as well. It’s incredibly smooth, but let me get to why that’s the case. But the original motivation though was the wide baffle. I initially thought bigger cones. this design originally started three or four years ago using a ten inch base unit. And the reality is.
Sharron: So what size base unit does it have?
Andrew Hutchison: Well, the new one is a six and a half. So we’ve got a box that’s big enough to put a ten inch driver in it, but it’s actually got a six and a half inch drive unit in it. And there’s, there’s a, there’s a. The people listening who know a bit about loudspeaker design will know exactly why I’ve chosen to do that, because the ten inch, a ten inch two way is kind of almost impossible to make work. So you can. And that’s where I came unstuck. So this design is a spin off of two loudspeakers that I’ve actually done before. Ten inch two a, which never made it to production. And our first production, speaker, the m six, which, I mean, m kind of stood for monitor. It was quite an accurate loudspeaker, but at the core of its design was that it had a particular drive unit in it with a paper cone. Has a very smooth response, well north of its usual, pass band. No nasty breakup modes. And the enclosure was built from plywood. Birch ply.
Sharron: Okay, so birch ply instead of veneer.
Andrew Hutchison: Which is what you used for the others. Well, yeah, I’ve used a veneered MDF. So, we could talk about MDF versus plywood. We could talk about paper cones versus hard aluminum
00:15:00
Andrew Hutchison: or beryllium or, you know, magnesium or ceramic or all.
MDF is used on 99% of the world’s loudspeakers
Sharron: Let’s talk about that. The difference between what you’ve used, the birch ply, and an MDF, which is what’s used on most other speakers.
Andrew Hutchison: Absolutely. MDF is used, I would say. Bye. 99% of the world’s loudspeakers at any price. There, are, of course, exceptions. At the super high end, there’s aluminium, notably at the moment, is in fashion. And various, composite, materials, the likes of Wilson audio use, etc. Which, are, ah, very expensive to manufacture with and reportedly have reduced resonances, but at the cost of, in most cases, well, enormous cost, but also weight. so that’s not a perfect answer either.
So plywood versus MDF. Why use plywood over MDF for loudspeakers
So plywood versus MDF. Well, MDF is quite heavy. It’s a sort of a. Well, it’s a fake material, right? It’s basically sawdust, very fine wood dust, and glue or resin.
Sharron: Okay.
Andrew Hutchison: Whereas plywood’s wood. It’s as simple as that. Plywood is timberland, and, it’s not full of resin. It is glued together in layers. And birch plywood, or multiply or whatever people want to call it, is usually about a 1.2 to 1.6 millimeter thick veneer, cross laminated for however many veneers you need to make up the thickness of the board.
Sharron: Okay.
Andrew Hutchison: So it’s got a completely different set of properties to MDF. MDF is sort of a. It’s a wonderful material. I’ve always liked MDF. It’s so good to machine, it’s so good to paint. You know, if you want to do a painted box in a high gloss lacquer finish, it’s the stuff that you want to use. It primes beautifully. It sands, you know. Well, you know, it sands well enough, but then once you prime it, well, that you’ve got this eggshell of paint on it.
Sharron: The birch plywood then, that you’ve used on the new 70S Model model, is more difficult to use, more expensive to buy. Why use it then over the MDF?
Andrew Hutchison: Well, here’s the key thing, right? So if you prioritize performance, so the sound quality is your number one goal, not your pretendy marketing goal, but your real goal and the design, you will, of course, use birch ply or some premium plywood. It’s sometimes made out of other timbers, and we are experimenting with other timbers at the moment, which we’ll talk about in a future podcast. But for the moment, it’s birch ply, usually made on the other side of the planet, out of, birch, which is a, you know, impressively light hardwood. So the, the, And I’ve forgotten what the question was. Oh, the interesting thing.
Sharron: Why use?
Andrew Hutchison: Why use?
Sharron: Okay, it’s more expensive, more difficult, doesn’t cost MDF, which is what everybody else.
Andrew Hutchison: Uses, doesn’t cost any more money, right? So here’s why it doesn’t cost any more money. It’s actually, compared with MDF, it’s five times the price. So, birch ply is five times the price of MDF. MDF is dirt cheap. Even in Australia, we make tons of it. Every kitchen is made out of it. Well, every good quality kitchen. Obviously, particle board is what poor quality kitchens are made from. But I mean, you know, particle board, moisture resistant, is actually quite an okay material, and probably in some ways better for building loudspeakers. But let’s not go there just at the moment, because it’s got actually more wood structure to it. But get back to MDF, which is.
Sharron: What loudspeakers are, let’s not add another timber.
Andrew Hutchison: So, MDF is a fifth of the price until you put a fancy veneer on it. So to make MDF saleable and to make it look like something, you can either paint it or you can veneer it and veneers, if you’re making loudspeakers in Australia and using australian materials, is the same price, if not more expensive, than birch ply, in fact, somewhat more expensive. So we use it because we want the box to look pretty normally, and retailers like it, customers like it. We would not be selling loudspeakers through HiFi dealers if we were making boxes out of plain plywood, which is to wind back is what the m m six was. It was a stained and clear coated plywood box, which I thought looked okay. But a number of dealers very quickly made me aware that looks like shite. Don’t come back here with that. You’ve got to make it look pretty. And then the fr six was invented. So. And the reason why I didn’t veneer the plywood, the m m six was made out of and do that was because then you’re talking huge amounts of money. So.
Sharron: So the new. The new model then is made from birch plywood because it sounds better.
Andrew Hutchison: Well, to get back to that. So the structure. So it’s actual timber now, people will say, oh, you don’t make speakers out of real wood because it’s all different and it’s got resonances
00:20:00
Andrew Hutchison: and knots in it and you don’t want to. And they’re right. But all of that goes away with Plywood. So you gain incredible strength and stiffness. But it’s incredibly light because it’s not full of resinous. So. So the board is bits of wood cross laid, you know, to create this very stiff structure of, whatever thickness you need. And we use quite a thin, plywood because that’s another design attribute that I like. And we’ll get to that. But so you end up with this board that I’d say is about two thirds of the weight of MDF, just based on how much muscle power is required to lift a sheet onto the router. And, never actually weighed it. but it’s dramatically less and, dramatically stiffer. It doesn’t move, it doesn’t bow. And, maybe it does eventually, you know, under difficult, you know, australian humidity, high humidity conditions. But it’s. It’s very stable compared with MDF. So. So the point is it absorbs energy, I guess the same amount of energy off the back of the drive unit as MDF. It doesn’t do much with it. It doesn’t weigh as much. And you can control the resonances in a way where you can both vary the resonant frequencies of the panels quite, easily with, damping materials. And because it does ring a bit, you know, with it undamped, it rings kind of more than MDF because MDF is internally damp with all that resin. I don’t want to get too bogged down on this, but if you. The result with an MDF box is it always has a certain, you know, it does. It has a certain boxiness to it. It sounds a bit leaden. It has a certain tone in the vocal range, probably in the lower to mid part of the. Well, just the vocal range sort of, you know, 200 to 600 hz or something in that range. And that’s where most of the resonances are. And they. I don’t know. I’ve compared the same loudspeaker design with the two different materials. The plywood is so much better. You can.
Most speakers under $10,000 are made in China
It just doesn’t sound. It doesn’t have the sound of a box. It doesn’t sound like it’s in a box.
Sharron: Right. So we’re not hearing the box. We’re hearing the music.
Andrew Hutchison: You’re hearing the sound that’s coming off the drive units on the front of the box.
Sharron: Okay. And that’s what speakers are supposed to do, right?
Andrew Hutchison: Yeah. Yeah. Well, in an ideal world. But you’re also hearing diffraction, reflection, what have you, off the front of the box, which is, we address those issues with the wider baffle to some degree, and. And, we’re, of course, hearing reflections off other parts of the room. So you’ve still got your room problems, but that’s where the wider box comes in as well. But the, wind back and finish put a line under the MDF versus birch ply thing, because everyone would naturally be saying, oh, no, this guy’s a lunatic. Clearly, you know, the likes of XYZ speaker manufacturer, insert name of favorite speaker manufacturer of this particular audio file. and surely, you know, they use MDF because it’s the best solution. No, they. They just don’t. I’m sorry. MDF is so easy to machine, so inexpensive to buy. And if you’re building speakers in Europe or China, the veneers are nowhere near as expensive as they are here. So let’s take China, because most. Let’s face it, most speakers under $10,000 are made in China. The vast majority, certainly any manufacturer with any volume manufacturing in China or somewhere in southeast Asia, where materials are just cheaper. So, they, they do it because it’s cheaper, and it’s. It’s. It’s quite effective and it’s consistent. But like a lot of things, it’s. It’s not the perfect answer, but it is the convenient answer. So, plywood is a pain. It’s a pain to machine that. It, it requires nice, sharp tooling. MDF, you can machine quite effectively with blunt bits. Get away. Just plow on through, and then sand off the edge. This does not happen with plywood. It’ll just tear through the board. So you need to machine, you know, keep the machine in tip top condition with fresh, fresh machining bits. Nice and sharp. So, because, you need to tool it.
Sharron: Stereotech manufactures your boxes. Youre loudspeaker cabinets, for Dellichord. Then you’re aware of these things about the timber work that perhaps other manufacturers wouldn’t be because they don’t get involved in the actual manufacture of the cabinetry, I think.
Andrew Hutchison: Yeah, absolutely. Now there of course, are a few speaker makers who make their own boxes. I mean, notably locally. Krix, would be, you know, the obviously, comparison. I mean, they’re sort of the same manufacturer, except they’re 1000 times bigger than we are, if not 10,000 times bigger. But the.
00:25:00
Andrew Hutchison: They do, they may, to my knowledge, use plywood. I don’t know. But I know in their HiFi home, you know, home HiFi speakers, I believe all MDF. And it’s. Hey, we’ve been using it as well. It’s, it’s great material.
Sharron: But because you’re a bespoke style, artisan style, quotation marks, manufacturer, you can do the plywood option and get a better sound.
Andrew Hutchison: We can use whatever we want. Now, it depends on our priorities. Now, in this case, like I’ve mentioned a few times, the appearance of the box is irrelevant. So we’re not going to spend money.
Sharron: On veneers of the box. The design of the box, the design of the loudspeaker. The way it looks is a particular look which nobody will see until the show when we take the. Take it out of the box for the first time. But I think people will like the way it looks.
Andrew Hutchison: Yeah, yeah, no, that’s fine. That’s a decent point. And that’s. That’s one. It’s okay for you to like the look of it. What I’m trying to draw attention to is that I didn’t care what it looked like because I just. This was a design exercise in the best possible sound for the least possible cost. But the product being made in this country. Right.
Sharron: So you’ve managed to make a less expensive speaker with better sound than you would expect from a more expensive speaker.
Andrew Hutchison: Well, that’s, I guess, always the goal. But it gets easier if you throw away the, the aesthetic values because. So let. So we’ve already said that birch ply costs less than MDF with a veneer on it. So first box ticked. So as far as the materials to build the enclosure from, we now have a better material. Tricky to work with, but when you optimize it, both the construction and the internal dampening of the panels, you get an amazing sounding box. So, job done.
Sharron: So what else have you done?
Andrew Hutchison: Well, what else? That’s right. So the next step is.
grilles are the stupidest things. They perform no useful functioning except keeping children off speakers
Well, okay, so grilles. grilles are the stupidest things. And loudspeakers I hate, bar none, ugly. They perform no useful functioning except keeping children and cats off your speakers. My advice is throw a tea towel or do something or lock up your children, put them in the soundproof cage, whatever. The point is that if that wasn’t meant seriously. Of course, there is no such thing. I don’t think maybe on Temu or something has a soundproof child cage. I don’t know. But anyhow, the point is the grilles, what would be cheap? You probably get three for $12. I don’t know. Anyhow, the free freight on your first order. So the grilles gone. Because no grilles. grilles can have their uses. If you design the box to work with the grilles sound best with the grilles on, that’s fine. And they’re an okay thing. It raises the cost of the box, though. And then when you take the grilles off, it doesn’t sound as good. If you design the box to have no grilles and sound at its best, that is, the grilles off. That the loudspeaker sounds correct as per the designer’s intentions. As soon as you put the grilles on, it doesn’t sound as good. And the difference can be quite large. And the, amount of loudspeakers that work well with the grilles off, in particular in a low volume model where there’s no plastic mouldings or high tech grilles that have had their cost reduced to nothing by making 50,000 pairs. If we ignore all those, there’s very few smaller brands. And I probably don’t need to mention them. But, you know, they’re kind of, you know, Spendor, Harbeth PMCs of the world. very rarely would they be designed to work, you know, in. In both scenarios, they’ll either be grilles on. In the case of, I think, well, the LS3/5a works best with its grilles on, for instance. And most, are designed for work best with a grilles off. So grilles are gone.
Sharron: So no grilles.
Andrew Hutchison: So there’s a saving. There’s 10% saving straight away.
You can gain a small performance advantage by using slightly less expensive posts
the, next step is fancy terminals. Now, you know, it’s a bit of a pet subject of mine. I appreciate the terminals that we use. Normally, the ETI, which is a largely locally crafted, certainly locally designed binding post that’s exceptionally good, world standard. Very well priced, actually, for what they are. And that’s why we use them. They’re local and they’re sharply priced for that kind of, you know, solid copper, you know, machined from copper, not just some gold plated piece of tin or brass or whatever. They’re a very high quality binding post and there’s certainly a small advantage in performance from using them. Plus, you know, you can put bigger cables on them and there’s other practical benefits.
Sharron: So we’re not using ETI on the new model?
Andrew Hutchison: No, absolutely not. We’re still
00:30:00
Andrew Hutchison: using a high quality terminal post that’s made in the UK, but we’re not using the ETi one. We’re using a high volume production one. It’s an old design, probably from the seventies. so it looks a bit seventies, but actually it works pretty well. No, it’s not made from solid copper.
Sharron: So we haven’t lost. You haven’t lost any m, you know, of the high grade music, little sound that you’re trying to get out of this Sharrony using slightly less expensive posts.
Andrew Hutchison: I think the trade off is very small and I think, like a lot of things, you know, we. Okay, so we’re using quite an expensive tweeter. So, you know, that’s where the money has been spent to gain a much bigger improvement in performance than you would get by using a less expensive tweeter, but a more expensive post. So it’s a case of priority. So the tweeter. And, We’d be jumping sideways to talk about that yet, so I won’t. But the, The, I should say, I’ve actually made a list here for my own, just to jog my memory.
Sharron: So we’ve gone birch plywood.
Andrew Hutchison: we’ve birch ply because it’s actually cheaper than MDF with no veneer. With veneer. With no grilles.
Sharron: We’ve gone,
Andrew Hutchison: No fancy terminals.
Sharron: No fancy terminals.
The biggest cost of designing any loudspeaker is research and development
So what else have you done to keep the price low but the quality of sound high? U 70S Model?
Andrew Hutchison: Well, the biggest cost of designing any loudspeaker is research and development. So the R and D was already done. So tick. We’ve taken sort of sunk sunken costs in the development of the ten inch two way that doesn’t even have a model number. And I forget what I was going to call it, but something unimaginative, like m ten, I think, from memory. And then the, And then the, which I spent about a year on, on and off, kind of getting not nowhere, but certainly understanding the problems of melding a ten inch or a large diaphragm driver that’s pretty much lost its off axis output by 15. Trying to meld that with the tweeter that is, you know, doing the opposite, it just doesn’t work. You create an enormous dip in the off axis response, and the power response in the room, the all encompassing, just general output power of the speaker over a broad range of listening angles, is lumpy, and unpleasant. So manufacturers managed to pull it off. But this is where we come back to the wide baffle. The ones that have been most successful have used a very wide front baffle. So, baffle meaning literally they’re just the front of the box. And so they, you know, if the baffle is three foot wide or a meter wide, to use, apparently the new dimension, measurement methodologies, rather than feet, is, you know, you get, you get this advantage, in a number of areas, but I’m not, still not sure that that really helps with the, off axis performance at around 1.52k. So I don’t know, but they make it work. But they do. One thing that we’ve done as well, which is you use a tweeter that’s slightly horn loaded. So that actually reduces the, off axis output of the tweeter at the lower end of its range, so you can more easily meld it via the crossover to the output of your larger base mid range driver. And of course, that’s why we changed it to a six and a half rather than a ten, because the, the, six and a half has quite an even response up a little bit higher. And so, in fact, we’ve successfully crossed it over at 3000 on the, on the dot to this, some would call it a wave guided tweeter. It’s a 25 mil soft dome, which is, you know, the most probably common tweeter on the planet these days. And that, works really well. I mean, it just, it makes the bit of difference. Plus, we’ve got the wide baffle, which we’ll come to in a second as to how that really helps. And, and, we’ve set the tweeter in flush, but the bass mid sits on the surface of the baffle, just trying to get a bit more of a time alignment thing happening.
Sharron: Right. So, and you’ve heard these and you like the way they sound with all of these challenges that you made?
Andrew Hutchison: Because I designed them.
Sharron: Yes. You’ve heard the finished product.
Andrew Hutchison: Yeah.
Sharron: And they sound pretty damn good.
Andrew Hutchison: Well, I want to go on about what I would like people to do if they’re hearing this podcast and they’re going to the show, or in fact they’re not going to the show, is give me a call or something and we’ll chat about it. But we. We certainly can send them out to you to have a listen. But the
There’s another aspect of this price thing that I want to talk about
Because there’s another aspect of this price thing that I want to talk about which is how we actually go about selling them. Because the biggest cost is
00:35:00
R and D. The second biggest cost is just how the product is marketed and sold.
Sharron: So you did your R and D over years and years and other speakers and other models and other things. So the R and D Washington done. You just made it better.
Andrew Hutchison: Basically I looked up my notes from those two designs, went back through the crossover designs for them and went why did I do it like that? And then with my Somewhat greater success with the current production models, applied some of those ideas. But I think I’ve skipped ahead. I was talking about. So we used a six and a half inch. I said that 3000 hz crossover. Yeah. we will have a break because I’ve forgotten where I was up to. Sorry folks, back in a second.
Andrew Hutchison is the designer and manufacturer of Dellichord loudspeakers
Sharron: So we’re back, not an audiophile, the podcast. And today we’re talking to Andrew Hutchison who is the designer and manufacturer of Dellichord range of loudspeakers. And we’ve been talking about the new model, the 70S Model, which is being unveiled for the first time at the Melbourne HiFi show. Eleven to 13 October. and we were talking about costs and how costs have been minimised in the seventies, but the sound quality has been maximised. Andrew?
Andrew Hutchison: Yes. Thank you, Sharron. Yeah, I’m just checking my notes because, you know, I’ve got all these complexity, unreadable, handwritten notes. we were talking about all of the ways that we go and stuff it. Let’s remove all these fancy accoutrements, and just go for performance.
Sharron: So do we have bling?
Andrew Hutchison: Well, we’ve got rid of the bling as well. Our loudspeakers generally don’t have much bling and most low volume loudspeakers don’t. Bling is not really possible when you are making, 100 pairs of loudspeakers a year. If you’re making 10,000 or 100,000 you can have all sorts of fancy, you know, faux gold plated plastic rings and trim rings and rubber parts and things that clip on here and press in there. And certainly makes for excitement for the poor person who has to pull it apart and repair it someday. Because pulling all these things back out is almost impossible without damaging them. And that’s another story. it’s also not immediately obvious how the speaker comes apart, which is always exciting, too. But, I guess speakers are generally reliable, but the small volume ones, generally are very reliable because they’re made from premium parts because that’s basically all you’ve got access to. So, yeah, we. So, no, no trim rings and bits and pieces.
Sharron: No shiny bits.
Andrew Hutchison: No shiny bits.
Sharron: Okay.
Andrew Hutchison: So, yeah, Veneer brings nothing to the table and. Yeah. Ah, I’m just going to hark back. I forgot to mention, and this is a funny fact. or fun fact about. A fun fact about MDF versus plywood is that you can suck air through MDF. You know, MDF, because you mentioned the veneer, doesn’t affect anything. Well, what the veneer does is it seals the box. So an unveneered MDF box actually is not airtight because MDF is completely porous. You could connect an air compressor up via a bike valve or something to a MDF box and blank off the drive unit hole so that they don’t just push out and pump it up. And you’d never. If you pump it up like a tire, is what I’m trying to say. So you pump it up to 50.
Sharron: I have a vision of you pumping.
Andrew Hutchison: It’s actually a thing that I’ve done. So you, you pump up a box.
Sharron: Right.
Andrew Hutchison: Then you pump it up to tyre pressure, say 30, 40 psi. Don’t ask me what that is. In millibars.
Sharron: So you’re saying the MDF will leak?
Andrew Hutchison: Oh, it won’t hold pressure for more than a 10th of a second.
Sharron: Right.
Andrew Hutchison: So it’s completely porous.
Sharron: Plywood is different to that.
Andrew Hutchison: Plywood is completely sealed.
Sharron: So if you pumped a plywood box full of air from a bike pump, it would hold pressure.
Andrew Hutchison: Absolutely.
Sharron: Okay.
Andrew Hutchison: Not for forever and not for very long, but longer than MDF, which is completely porous. So, of course, the, the MDF is ultimately made airtight by painting it or veneering it or both, of course, because you’re putting a clear coat over the veneer. But it’s an interesting thing that MDF, by itself is not even airtight. So clearly unusable for loud speakers.
Sharron: Yeah.
Clear coated plywood looks a little bit retro in a boat interior
So what have you done then with the new seventies from the birch ply? That, isn’t just plain birch ply. You haven’t veneered it?
Andrew Hutchison: No, we have. What we’ve done is we’ve just sealed it, and sanded it and painted it with just clear lacquer. And so it looks quite nice,
Sharron: Looks a little bit retro.
Andrew Hutchison: It looks a little,
00:40:00
Andrew Hutchison: looks a little like, what it is. It’s actually quite a nice. I was going to say semi industrial. I mean, there’s a look that you see in interior design where people use paint, clear coated plywood as a sort of an architectural feature, I guess, quite often in ceilings, feats, things like that. This is, And there was a fad in the seventies, maybe, building kitchens out of plywood. You know, it’s a look.
Sharron: It’s, a good look.
Andrew Hutchison: It’s a boat interior look in a really poor person’s boat. you know, with no fancy veneers. But it is.
Sharron: It’s almost a scandi.
Andrew Hutchison: It’s actually no such thing as a poor person’s boat, when you think about it.
Sharron: No.
Andrew Hutchison: well, they probably might end up poor.
Sharron: They are poor now. They own a boat. They weren’t poor when they bought the boat. I think it’s a quite a scandi look. It’s very. It comes up very light. And it works very nicely in interiors where you have light timbers, whites, natural look, you know, maybe some cane or some, you know, grays or whatever. But it’s, I like the look of it. I. I like the way it’s slightly retro, slightly vintage. It’s an aesthetic that I like. I think other people will like it too.
Andrew Hutchison: Well, not to be put off by.
Sharron: The fact that it’s not. It’s not fancy. It doesn’t have to be fancy.
Andrew Hutchison: Well, no, because it’s to make music. And, to get back to that, it, does a hell of a nice job.
Diffraction on a front baffle is, uh, a problem
So let’s just summarise the actual key features that, rather than save cost, actually make it sound good. And maybe we should have done this first. So the wide baffle thing. Okay, so diffraction on a front baffle is, a problem. basically, the change of pressure, I guess, as the sound meets the edge of the front of the box, actually causes reflection, which we call diffraction. But really it’s kind of just reflection. And so because it’s such a short period or short distance from the tweeter and mid range driver to the edge of the box, on a normal narrow baffle box, it happens both at a high frequency and, it’s. And because it’s at a higher frequency, it’s more ruining of, the sweetness of the sound, just to sum up the effect, but also the quality of the stereo imaging. So when you go to a wider baffle and perhaps a taller baffle, in, this case, not taller, because it’s a large stand mount box. Just to clarify that, it’s further away. So the diffraction artefacts happen, because they create nulls and peaks in the response. they happen, at a lower frequency. And then when you do, when you achieve that, you are also getting less diffraction because there’s less to some degree. Well, less. I don’t want to get myself tangled up in a. There’s so many things going on. Let me just say that you. You have less trouble with diffraction if you make the box wider. And that’s pretty much a fact. But if you then do what I’ve done and move the drivers around to sort of, optimize the disturbance to be less. Less, annoying. So if the drivers are mounted symmetrically on the front baffle, you’ve got bigger, troughs and peaks in the response because it’s all happening at least left to right laterally. If the driver’s on the centre line, it’s both. Both edges are causing the same problem at the same frequency. So if we move the drivers around a bit.
Sharron: So this one has an off center.
Andrew Hutchison: It does. It has an asymmetric but mirror image, which is important.
Andrew Hutchison: Pair. So, you know, the left one. And you set them up with the tweeters on the outside is the way the thing is designed. And so there’s a couple of things going on with that. But if you have mirror image, you certainly end up with the same. Assuming you’re sitting, you know, more or less in the sweet spot. You get the same frequency response, from both speakers. And so you get excellent stereo imaging.
Sharron: Okay. And they don’t have to be angled in, do they? They can be. They can sit forward.
Andrew Hutchison: They have pretty even off axis response up to about 40 degrees. And then. And then, like all speakers, things happen because, you know, that’s good. Getting quite a way off axis. But, the point is that you can toe them in a little bit or a lot. That’s your preference. But, I find them to be lightly toed in and they work. The imaging is really. And the imaging is great because these diffraction artifacts that are left are at a lower frequency. That messes less
00:45:00
Andrew Hutchison: with the, stereo imagery. and it’s a less, less annoying part of the frequency spectrum as well. So it’s just. But there’s also the crossover, right. So we haven’t cut any corners on the crossover. So the crossover is the. No matter what you do with drivers, the baffle size, the box materials, how you set your system up. doesn’t really matter what, how good your amp and your turntable cd player streamer are. It just doesn’t. Tape deck dear radio tuner doesn’t really. It doesn’t really matter. The crossover is the thing. Well it’s still just a bad.
Sharron: Yeah.
Andrew Hutchison: Bad crossover.
Sharron: Using, still going to get bad sound.
Andrew Hutchison: The crossover has to perfectly combine the output of the two drive units. In this case it’s a two way six and a half inch two way loudspeaker has to combine that output in a way that is both phase correct frequency response correct. And it has the correct balance between the output of the two drivers. So this is quite time consuming to get right. the thing that people like Brad Sirhan is highly regarded for because the.
Sharron: Tweaking of the crossover.
Andrew Hutchison: Well it’s the, it’s. I mean he does a lot of things right but the thing is he, it’s. It’s a skill that he’s got I guess practices some of it. So. So I’ve been practicing and I got better.
Sharron: And so you can hear the minute differences in.
Andrew Hutchison: Well I knew. I think the thing is that there’s umpteen ways to go about it. There’s no, there’s probably 20 different ways you could implement a crossover in a two way. Different steepness of slopes, different topologies, different ways you can equalize aberrations in the response. there’s so many. It’s a conversation you would have with Brad and you could run through all of the ways you could do it.
Design of the box and the choice of drive units is critical
So I’ve gone about it in a very particular way because the goal was to keep the crossover as simple as possible but to get as well as Brad would say the stitch up to be perfect. In other words where the two drivers meet they do it in a way where they kind of sound the same. So this is where the design of the box and the choice of drive units is critical. So, so I’ve chosen a paper cone base mid with minimal if any nasty breakup modes at higher frequencies than you would normally use it because this is what happens in a six and a half inch driver. So a hard cone like aluminium or carbon fiber or what have you has some quite nasty 1015 decibels spiky bits probably at five, six 7000 hz which you have to filter out when you implement this crossover. Otherwise it will sound dreadful. Now the other. So we’ve used a paper comb because we get rid of that now. Yeah there’s a few trade offs with a paper comb, but. But, fashion is probably the biggest trade off. It’s not fashionable, you know, so, you know, something new is, you know, anything carbon fiber is better than anything else.
Sharron: Right. You know, all things old and new again.
Andrew Hutchison: Right there is that as well. But why? Why is that the case? Why? Because sometimes people hear something old, like a turntable, and go, that’s got a real charm to it. I love that. That’s. That sounds nice. You know, you know, open real tape. An analog recording has this ease, this lack of digital haters would say lack of digital hash, if you like. It’s not as clean, it’s not as punchy, it’s not as detailed, but it has other qualities. So this. So this paper cone business is a little bit about. Yeah, it’s a look back to the. It comes back to that desire to get that easy sound, that sort of. That fatigue free. Charming is a terrible word in a way. It doesn’t really say much about the balance or the way it sounds or the technical aspects of it, but it does imply that you hear it. It’s a bit like you’re walking down the street. You hear music, you immediately know whether it’s recorded or live. Okay, so that’s, that’s, that’s the difference. Now, the human is so good at picking up all of the flaws in recorded music and played back recorded music that it can easily tell when something’s live. Right. There’s all sorts of reasons which
00:50:00
Andrew Hutchison: someone like our, well, previous guest, David Spargo, could explain more eloquently because he’s a guru of these things. But there are, ah, it’s to do with, dynamics, lack of distortion. Harmonic structure is intact. All of these, these key things. So this is where a paper cone, well, it gives you a head start. So this is, if you’re going to design a speaker for performance, you want to make everything work towards performance. So, the wide baffle, the paper cone, it means there’s less to deal with in the crossover. So then the next thing is the tweeter soft dome. Tweeter textile dome. Some used to call them a silk dome. I don’t think they were ever made from silk. Maybe they were, maybe they were, but they’re not anymore. So, it, once again, it has not got some difficult breakup modes outside of its pass band at very high frequencies that we don’t have to deal with, and we may or may can’t hear because they’re above, you know, the human hearing, range, but maybe not above your dog’s range. I always wonder about beryllium tweeters and dogs. The dog is putting its paws over its ears whenever you turn your pair of focals on.
Sharron: Anyhow, so we’ve got, we’ve got the right box.
Andrew Hutchison: So we’ve got the right box, the right driver.
Sharron: We’ve got a simple crossover that should be.
Andrew Hutchison: We haven’t got a simple.
Sharron: We’ve got a crossover.
Andrew Hutchison: Simple crossovers don’t generally work if you’re aiming for a smooth genuinely flat response at various listening angles. So getting back to the live music analogy, so that lack of coloration, we all know what a saxophone sounds like and when it’s amplified suddenly of course it takes on to some degree the color of the PA system. If it’s played outside a sax, a busker playing a sax is amazing. Some would say it’s even better if they’re in a tunnel but, well it does because it adds, you know, more reverb, it adds a color. So no, colour is not necessarily bad. Right. Which, you know, is where I’m getting at, where I’m coming to.
Design goal was a very natural sound. And you achieve that by all other things
So that’s not to say our speaker is coloured. It’s not. But the crossover, the goal, yes, was to use all these correct ingredients. So the crossover hopefully could be as simple as a seventies crossover. Well that of course is just not going to work out because it was a different time. Yes. People were more accepting of a more coloured sound and by coloured I mean less even in its respect. And obviously the designers had very carefully judged these response anomalies to be as non annoying to humans as possible. And so I’ve done a similar thing but really in the end just really gotten rid of most of the colouration but used a crossover frequency that the drivers enjoyed. It worked out well for them. But it also is at around 3000 hz. It’s not a bad place to put a crossover if you can get away with it. I find that 1000, 1500 is maybe even 2000 is a danger zone for a crossover and a two way. I think it doesn’t, it sometimes sounds unpleasant or very hard to get. Right.
Sharron: Well we want pleasant, that’s why we’re listening to loudspeakers. We want pleasant.
Andrew Hutchison: So they ended up. So we’ve basically got. I’m going to go into the topology of the crossover because it’s a secret, but.
Sharron: Well the whole thing is a secret until we take the box off it on the 11 October.
Andrew Hutchison: But the. I think when people hear the loudspeaker they’ll go, oh, that’s kind of clean and sweet, and very natural sounding. And that was the goal. So that, to cut to the chase, finally. What the design goal was a very natural sound. And you achieve that by all of the other things that we’ve just mentioned.
Sharron: So it looks good.
Andrew Hutchison: You’re saying it looks good.
Sharron: It sounds amazing. we’re taking it to the show. Dellichord is not retailing this loudspeaker, though. As in through retailers?
Andrew Hutchison: Well, yeah, yeah. In fact, Dellichord is retailing.
Sharron: It’s, Dellichord is retelling.
The speaker comes with a custom stand that’s optional
Andrew Hutchison: So here’s the final thing. Here’s the ad. Because, because we’ve got to wrap this up. So we’re selling it direct, as mentioned. But we’re also, here’s the weird, here’s the twist. We’re selling it a couple of different.
Sharron: Ways because nothing can be simple.
Andrew Hutchison: No, no, no. I like to make things complicated. So you can buy the speaker as a finished product, comes in a box, comes with a money back guarantee. If you hate the sound of it, you, of course, send it back in perfect condition and all the other require, you know, and comply with all the other terms and conditions.
Sharron: What andrew hasn’t mentioned is it comes with a custom
00:55:00
Sharron: designed stand that’s optional. Yeah, there, is a custom design stand, but it’s optional, which is optional.
Andrew Hutchison: Because the loudspeaker and, people are going, well, what is this thing? Three grand, two grand, ten grand? It’s, it’s $2,999 complete. Arrived well at your door.
Sharron: Plus, plus freight, plus the custom stand.
Andrew Hutchison: And if you need stands. But let’s not talk about the stands. People will see those at the show. They’ll see them in the follow up advertising, etcetera. But the, but there are, you can store records in them. So a bit like, certain other stands that are out there, which it’s quite, I think, a smart idea. it’s a, it’s a wasted space otherwise.
You can make your own speedgate speaker with just a few screws
So here’s the way you can buy the speedgate. So you go, well, I don’t like the look of your scandi, clear coated speaker. It looks ridiculous. It’s not going to suit my house. Can I have it in another finish? and the answer to that Henry Ford style is, yeah, you can have it in any color that you want, as long as this is it. Okay, so the, so the way around that is to, because you can’t have it in black Henry Ford style, but you can make your own black ones. So what we suggest you do is you buy the less expensive version of the seventies, which is what we call, well, I don’t actually don’t know what we call it. But let’s say it’s called the raw finish version. So it’s a fully assembled loudspeaker ready to go. You can plug them in and listen to them.
Sharron: Comes in a box.
Andrew Hutchison: It comes the same way as the normal 70S Model.
Sharron: But with raw birch ply. Raw birch ply rather than the clear coat.
Andrew Hutchison: Now, we’ve designed the speaker. So you can pull it apart really easily. You can completely disassemble, assemble it with just a few screws. There’s no soldering. You just unplug. I mean, we’ve soldered the wires to the drive units. Because that’s kind of important. Because for various practical reasons, I won’t go into. But the, other end of that cable plugs into the crossover board. It’s a fiberglass crossover board with premium components on it. Which I don’t think we just talked about that. But it’s so boring. Just there’s no corners cutting the crossover. The design is actually more complex than we would have liked to, but very elegant. And it works extremely well. And it’s made out of premium components. And it’s all mounted on a custom designed fiberglass circuit board. Which, in turn, screws to the rear panel that your terminals are on. So you unscrew those six screws, having unscrewed the front four screws out of the drive unit base mid. And you just pull it all out and pull the tweeter out. So you’ve got four screws for the base mid, four for the tweeter, six for the terminals. Pull the foam out. Boom, you’ve got an empty box. You can paint yourself. That’s the problem.
Sharron: So I can paint, I can buy that version, and I can take it home, and I can paint it fire engine red.
Andrew Hutchison: Yes. Now, here’s an interesting thing. I don’t think anyone’s ever done this before. Because no one is stupid enough to do this. And maybe no one will buy it, but it’s the perfect answer to I want a different color. Or I don’t like your, your clear coated, birch ply, very light, scandi colored finish.
Sharron: Or I don’t like the fancy veneer that you’ve put on your.
Andrew Hutchison: Well, there’s that as well.
Sharron: And maybe it never comes in the same in the color that people want. If you give it to them in walnut, they want maple. If you give it to them in maple, they want black.
Andrew Hutchison: Yeah. And maybe you want to touch the speaker and make it your own.
Sharron: Maybe you want that, that little, you know, home job that makes it your special project.
Andrew Hutchison: Yep. So we give you a spare set of badges. You peel off the, I guess, I guess you could just.
Sharron: You could tape around the badge.
Andrew Hutchison: No, you wouldn’t do that. You want to. We actually give it a very light sand before we give it to you. But, you will want to. So let’s say you want to stain these black. Japan black, which is actually a good choice. you, give it a light sand. You’re going to have to give it a sand. We’ve given it a bit of a preemptive sand because it’s hard to get into some of the corners. So that’s, so that’s, that’s taken care of for you. But, before we, before it’s assembled, we give it a bit of a quick machine sand. So it’s in pretty good shape. you could do it. It’s a Sunday afternoon job, basically, so. But you could wax it. You could oil it, you could, What’s that other thing you can get? You can stain it, you can clear cut it.
Sharron: So you can paint it, wax it, furniture oil it. I mean, you could wax and.
Andrew Hutchison: Polish and dust with Mister Sheen or something like that.
Sharron: You can do pretty much anything that you can do with a partly DIY timber project that makes it look the way you want it to look for the aesthetic in your home.
Andrew Hutchison: Yeah, absolutely. That’s that.
You’re going to spend half a Sunday painting your furniture. So that’s $22.99
So that’s the raw version. So that’s $22.99. So you’ve saved $700. You’re going to spend, I don’t know, half a Sunday. Half a Sunday. And a materials and some.
Sharron: But. And a visit to Bunnings, getting your paint or even a proper painting or proper paint store or a furniture guy.
Andrew Hutchison: I would highly recommend you go to a proper paint store and talk to them about the possible. You take a box
01:00:00
Andrew Hutchison: in and go how, you know, what, what are your thoughts? Because, nothing against Bunnings, it’s a great place to shop for yourself. But if you want advice, I think the days of them employing ex tradesmen seem to be over.
Sharron: You could go to a furniture guy and you could get beautiful furniture oil or furniture wax or something like that. That would give it an absolutely unique finish.
Andrew Hutchison: Okay. So you got that.
Siberia provides you with a fully finished crossover for $16.99
So here’s a, here’s a more technical option again. And, it’s going to sound like a kit Sharron cause that’s what it is. So we supply you. It’s not a kit. No, but the box is a kit. So the, so what we do is, and this is at less money again, so this is $16.99. And you end up having shipped to you a flat pack enclosure. So pieces of board straight off our, CNC, router. And we’ll give them a lightest of scuffs to, tidy them up a bit, if required, as far as sanding. But basically it’s up to you. So this is for the woodworker who, is comfortable with glue and clamping. you put the boxes together yourself. It’s pretty obvious how they go together. What we do is we supply you a fully finished crossover. No soldering. So, the wiring loom is ready to plug in. The terminals are labeled on the crossover. It’s pretty obvious how everything goes. obviously, we haven’t created the video for this yet, but we’ll create a video that allows you to understand how it fits together. But it’s very, very simple.
Sharron: So, this kit, that’s not a.
Andrew Hutchison: Kit, but it’s for a woodworker.
Sharron: It means that you can put together your own cabinet, but the crossover. And it basically just plugs in to your finished cabinet the way it plugs into the other two options.
Andrew Hutchison: Absolutely. I mean, it would make no sense to do it any other way. We’re building the crossovers in production volumes anyhow, and we just take two of those. And, you’ve got your little, terminal plate piece of timber. It attaches to that. It screws to the back of the inside of your box once you’ve built it and the drivers screw in. Drivers, once again have the wiring attached to them ready to plug into the board. we supply you the t nuts, the screws, of course, we give you everything.
Sharron: You get everything that you need to be able to do a proper diy job on this at home.
Andrew Hutchison: But I’m going to say it again. if this is your first woodworking project, it’s not because it’s hard. It’s maybe because you just. We wouldn’t like you to stuff it up. but woodworking doesn’t get any easier because the bits are machined to 0.1 of a millimeter. They just go together. The tolerances are just, open enough so that everything fits up together beautifully. And, there’s a pretty simple, straightforward technique to bring the box together with fully mitered corners on the outside. The front and rear baffles just fit in it’s ah, easily joints together nicely. it’s simple but you don’t want to stuff it up, I guess probably.
Sharron: the bonus of Dellichord being manufactured, in its own cabinet factory essentially is that you can put together a kit or a part kit, like the 1699 version that where, you know, everything fits together, that the pieces haven’t been machined by some overseas company and they’ve just shipped them to you and you don’t know whether they go together or not until the person on the other end is trying to put it together and they’ve all been machined upside down or back.
Andrew Hutchison: The front, there’s that. But there’s. The worst thing about speaker kits is that the speaker kit is generally never sold as a finished product. You can’t listen to it. You have, no idea how it sounds. It may be a thoroughly developed design or it may be a thrown together half okay thing.
Sharron: So in this case you can listen to the finished product and then decide if you want to downgrade from the finished product to a, to a paint yourself, finish yourself or from there to a build it yourself alternative.
Andrew Hutchison: Absolutely. So that’s I don’t think this is really a thing in the world. And there’s probably a bit. Probably it is now. It’s probably a good reason for. And we’ll find out, I guess. but for us it’s, it’s not a, this is no more work. We’re just handing off some of the work to the person who wants to listen to the speakers, let them do it and give them a saving in cost. It’s
Sharron: And we are talking. Ah, aud, right. Because you haven’t meant if you’re listening to this podcast and you’re in Siberia, the costs obviously, I don’t think we.
Andrew Hutchison: Can ship them to Siberia at the moment. But the The You’re right. If you are in Europe, the we are talking australian dollars. So.
Sharron: So you need to send us an email and go, I’d like a pair of these. How much would this cost?
Andrew Hutchison: Well, it’d be very inexpensive. The freight of course, is expensive, but the flat, pack kit is quite affordable.
Sharron: And these costs are also not including inclusive of freight.
Andrew Hutchison: So I mean, euros 1699 is probably a thousand euros, just as a quick, very quick and dirty
01:05:00
Andrew Hutchison: calculation. so, and probably 900 pound and probably about thousand on us dollars. So.
Sharron: So all these prices are aud plus freight and shipping.
Andrew Hutchison: And plus freight shipping. Yeah, but they include GsT. So there’s a saving there. So export sales, actually, they work out to be really sharply priced. But the, But this to clarify. So as a kit, this is a rare bird because this is a fully developed production model that we’re very proud of. The sound as a finished product, it’s completely. It’s more than competitive. It’s not necessarily competitive on the aesthetic states, but it’s made out of first class material.
Sharron: Andrew keeps saying that.
Andrew Hutchison: Don’t harp on about it.
Sharron: People who love. Who love the way it looks, the way it is.
Andrew Hutchison: And that’s maybe because it’s real. The real deal, I mean. And what I haven’t said, we’re gonna.
Most affordable loudspeakers are made out of cheap MDF
Sharron: Have an argument about how it looks. I think it’s great.
Andrew Hutchison: What I haven’t said, I’m not even gonna enter into it. What I haven’t said is most speakers you buy for this kind of money, $3,000 a pair, are just made out of crap. Let’s face it. They’re a high volume thing. They’ve got inexpensively produced, mediocre quality. But, but cool looking drivers, they’ve got inexpensive parts in the crossovers. you know, very poor quality cord chokes, that saturate easily. very poor quality electrolytic or really super cheap film capacitors. yeah, they’re chucked together on a lightweight circuit board, probably, but not exit executed particularly well. just all self tapping screws into MDF, which clearly you take in and out three times and the screw doesn’t work anymore, obviously, because the MDF is just chewed out. The, MDF quality itself is rubbish. I remember once during the MDF, the famous, MDF crisis we had in Australia about 18 months ago, where one of Laminex’s production lines and one of the other guys, production lines both broke. And, was in the middle, of course, of a housing boom. And to cut to the chase, I had to basically buy whatever MDF you could get. Now, some smarty, for the first time ever, decided importing MDF from China, would be the way to solve the, australian MDF crisis. So some turns up on the back of a truck, this dark brown looking stuff, which I had never, seen before. Most australian MDF is tan in color. I said to the guy, what’s that? He goes, I said, because he’s the truck driver, right?
Sharron: But he’s just delivering.
Andrew Hutchison: He’s just delivering us. That looks like China spec crap to me. And the reason why I know what China spec crap looks like is because that’s the color of the inside of most of the affordable loudspeakers that I’ve ever worked on, is they have this dark brown color MDF.
Sharron: When Andrew says he works on it, he works on it as HiFi and stereo. The, HiFi repair and service.
Andrew Hutchison: Arm, that is our repair division.
Sharron: Of the whole thing.
Andrew Hutchison: So you see inside these things, and the thing is, you know that the board is poor quality because you have to unscrew the drivers to perform a repair, and you don’t get to put them back in more than twice because the core of this, board. And by the way, so we got the material off the, truck. I machined a sheet some week or so later. It was for acoustic treatments. So, the quality of the board was m not critical, perhaps, but interestingly, when you machined it, so you open up the core of the board, it’s just dry and dusty, and it’s like a cross between, I was going to say weed bix, but that’s more particle board, but it’s like, it’s just brown dust. So there’s less resin in it. So they’ve made it cheaper. Surprise, surprise. They’ve worked out how to make it cheaper by putting less resin in it. And they’ve worked out to make it faster by putting less resin in it. And so on the outside, it looks like normal MDF, but it just isn’t. And you machine it, and as soon as you machine it, you can just break it over your knee so it has no sideways.
Sharron: Now, complaining about chinese spec MDF.
Andrew Hutchison: What we were trying to say was that what people don’t realize is for $3,000, you basically get a piece of crap now that it may produce quite reasonable sound, and it probably does. And, and that’s what its main chore is. But if you want something that’s actually made out of very nice materials that will simply last and in turn, I think, perform better in the first place, then this is more the product you.
Sharron: Should be looking at, and you can call the manufacturer,
01:10:00
Sharron: the designer, and you can talk to them about the product. Any questions that haven’t been answered on this long and involved podcast? I mean, that’s one of the pleasures of buying direct, is that you actually get to talk to the designer. You don’t have to go to a HiFi, show. And in order to speak to the designer of the product, you can call him up and ask him about the order one to take home and listen.
Andrew Hutchison: Just the one.
Sharron: Well, you’d like to have they come.
Andrew Hutchison: In left to right handed pairs, you.
Sharron: Know, we’d have one. When I say one, I mean one pair of the 70. Yes. but you know, people are going to have to, originally, they’re going to have to come to the HiFi show in Melbourne and have their very first look and listen. and so see what the hell we’re talking about.
Andrew Hutchison: Yeah, look and look. Thank you for listening. I think we have rambled for over an hour. yeah, well, I like a good ramble. It’s I’m good at it and I like to do it. there’s a. I think part of the problem is there’s so many things to cover and I don’t want to sound, by the way, that I’m down on chinese manufacturing. I’m not. They make fantastic things. I just mean products made with price as the number one goal and, you know, profit as the number one goal. And to achieve that, you will make it in China. Because people don’t realize just the scale that they do things is, it just makes things so much cheaper. So that’s what that’s about. It’s not about having a crack at China, it’s having a crack at. The philosophy of the manufacturer is that they want 90% of the retail price to represent profit and 10% to be the cost of the product. And that’s what they do. That’s the reality. And that’s not what this is.
Sharron: No. This is, if you’re doing artisan bespoke manufacturing, then you are your product. And I, so everything that you do say are, becomes the product becomes an extension of you. And, you know, if you are interested in quality, in sound and quality in manufacturing, and quality in raw materials and being australian and supporting australian, then, you know, an artisan bespoke manufacturer is a very good option.
Andrew Hutchison: I can only agree. I mean, well, partly because that’s what.
Sharron: We are and that’s what we are.
Andrew Hutchison: So we’re naturally pushing out our own barrow. So, look, thank you everybody, for listening.
We will see you all at the Melbourne HiFi show on Sunday
I will, hand over to Sharron to wrap up because she’s the host today. I’m the guest.
Sharron: goodbye. But I guess we will see you all at the, Melbourne HiFi show. And where you will see the new set of Nesdez and you will hear the new seventies and you will know what the whole podcast has been about, because right now it’s a great big secret. and you also will have had a chance to listen to all of the other podcasts on, not an audiophile. and you can come and tell Andrew Hutchison and Brad Serhan, who will be roving around the show, what you like, what you don’t like. what you’d like to hear, what you wouldn’t like to hear. what we’re doing wrong. And, you know, and if you’re inside HiFi, if you’d like to be a guest, you can waltz over and put your name down. And, Andrew can have a chat to you about perhaps appearing on not an audiophile as a guest at some stage. goodbye.
Andrew Hutchison: Thank you, Sharron. And, of course, if you wish to meet Sharron, she’ll be, Guarding. Guard. Guarding.
Sharron: Standing in the hallway at 2204.
Andrew Hutchison: All right. See you soon, folks. Bye.
01:13:47